Front Page
2019,10,01
掲載開始
Clone PRUSA 備忘録
読者の役に立ちそうな記事へのリンク
PINDAをSuper PINDAへ交換
PrusaSlicerとOctoPrintのリンクを設定
PrusaLinkのインストール 失敗
TPUフィラメントを試用
熱電対でノズルの温度を正確に測定
運転騒音の低減
GT2ベルト用張力計の製作
OctPrint用TVカメラにLED照明を取付けた
PrusaSlicer 2.4.0 導入失敗
黒Prusaの点検と整備
白Prusaの点検と整備
フィラメントの継ぎ接ぎに失敗
インサート・ナット使用記 ( 3Dプリンターで作った円筒形SP 完成)
PID Calibrationのすすめ
P.I.N.D.Aにプロテクターを取り付けた
減速ギヤ付きE軸モーターへ交換して細部の解像度向上
代替PEIシートでコスト削減
純銅製ヒートブロックで印刷品質向上 白PRUSA PID calibrationを加筆
純銅製ヒートブロックで印刷品質向上 黒PRUSA PID
calibrationを加筆
固体ポリマーベアリングで騒音軽減 純正品を試し
固体ポリマーベアリングで騒音軽減 海賊版を試した
Nylock-Spring Levelingでベッドの歪みを修正
歯付タイミング プーリーへ再交換して騒音軽減
OctoPrintの組込みで利便性が大幅に向上
停止時のX軸傾斜対策
Trianglelab製 Bear Upgrade PRUSA キットを組み立てた 黒PRUSA
炭素繊維入りPETGの試用 黒PRUSA
概 要
中国製のPRUSA i3 MK3Sの互換機を作った。費用は約6万円掛かったので廉くはない。
本家が販売する
Original PRUSA i3 MK3Sのキットが10万円弱で買えるのだが、
購入意思を固めた時点で在庫切れだったので中国製Bear upgrade PRUSA Kitの購入に踏み切った。
組み立てる過程で仔細な問題が在ったが適切に対処し、納得できる性能の3Dプリンターが完成した。
実際に印刷してみると不便な点が無い。従来の機械では面倒だった印刷準備の作業が殆ど自動化されている。
Bear upgrade PRUSAは、Original PRUSAの良く考え抜かれた素晴らしい機能を継承している。
左の黒いPRUSAは
Trianglelab製のKit、右の白いPRUSAは個別部品を買い集めて組立てた。
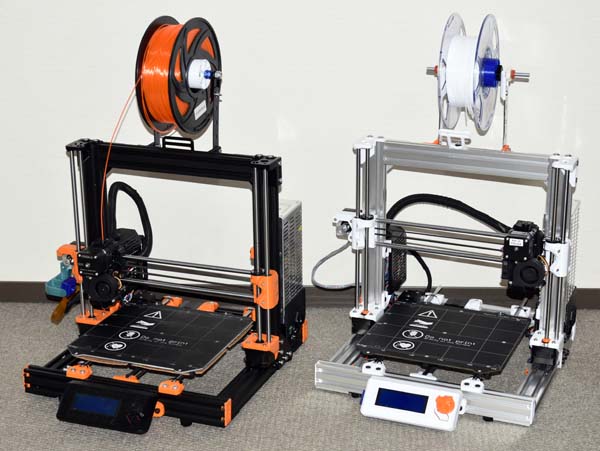
注1:写真のスプールスタンドは自分で設計し印刷した物で付属品ではありません。
1. 購入理由
過去2年半に亘って
JGAURARO A3を使った。問題の多い機種だったが、3Dプリンターのノウハウを得る事ができた。
しかし以下の問題を解消するためにBear upgrade PRUSAを導入した。
1.1 スクレーパー不要
先日、PLAで少し大きな物を印刷した。印刷を終え強くベッドに着いた印刷物を取り出す際にスクレーパーを使った。
スクレーパーを使っても剥がれず強い力で押したところ、印刷物が剥がれた直後に力が余って手をベッドにぶつけ
怪我をした。加齢で不器用になったのだろう。
今後怪我をしない為にバネ鋼板を磁力で吸着させるベッドを備えたBear upgrade PRUSAを買った。
大きな印刷物でもバネ鋼板を撓ませるだけで取り外せる。凄く簡単だ。
1.2 低騒音
JGAURARO A3ではXYZ軸を動かすモーターの騒音が大きくストレスを感じていた。
PRUSA i3MK3ではモーターを一度に動かす角度を小さくして動作音を可聴周波数よりも高くした。
その結果、モータの動作音の無音化に成功した。耳障りなピロピロピューピューは無い
1.3 PETGが上手
フィラメントにPETGを使った場合に最下層を印刷する際のギャップが正確でないと印刷に失敗する。
PRUSA i3 MK3では可動部を枠に衝突させて基準位置を決めているので位置決めの誤差が少ない。
JGAURARO A3のようにマイクロスイッチでゼロ点決めをする機種では印刷の失敗が多い。
PRUSA i3MK3には、ベッドの高さを調節する4個のネジが無い。
ノズルの高さは磁気近接スイッチで自動的に合せるので最小の労力で済む。
ノブを回して位置決めを0.001mm単位で設定できる。工具は使わないので便利だ。
2. 機種の選定と発注
通販サイトAliExpressでは多数のClone PRUSAが売られている。
その中から日本製のベアリングを使っていると謳っていたTrianglelabの製品を購入した。
自分が買ったのは
Cloned
PRUSA I3 MK3S Bear full kitと呼ばれる品だが、
同社は
Cloned
PRUSA I3 MK3S
full kitと呼ぶ品も売っている。
両者の違いが判らなかったが、骨格が頑丈そうで少し廉い
Cloned
PRUSA I3
MK3S Bear full kitを選んだ。
骨格がアルミのV溝棒なのでスプールスタンドなどの取り付けが簡単だ。
またOriginal PRUSAと同様に3Dプリンターで印刷された部品を多用しているが、
Originalと同じようにPETGで印刷されている。
安価なClone PRUSAではPETGとは謳っていないのでPLAかもしれない。
支払いには、りそな銀行のVISAデビットカードを使った。とても安全性の高いカードだ。
スマホのアプリで件、日、月単位での支払い上限が設定でき、引き落としが在ると即座にスマホヘ通知が届く。
通常、海外からの買い物にはPayPalを使うのだが、AliExpressではPayPalが使えない。
AliExpressで注文してから6日程でFedexが届けてくれた。
3. 到着と開梱
8月28日に発注した物が9月3日に届いた。10日間は掛かると踏んでいたので早くて驚いた。
荷はダンボール箱でベタベタと貼られた伝票が経由地の多さを感じさせる。
中身は個々の部品がプチプチや小箱に入れられていた。夫々が何かは書いてなかった。
箱の中に入っていた書類は6頁の梱包明細書だけで組立て説明書等は一切無かった。
つまり、この商品はキットと謳っているが実体は
Bear upgrade PRUSA用部品集だ。
この商品には制御用コンピューターは含まれていないので別の店から調達した。
たぶんRepRapやGitHubの著作権ルールに抵触しない為だろう。
梱包明細書に記載された部品は117点だった。実物と照合したところ不足は無かったが
下の写真の不思議な形をしたものが余計だった。
4. 組立て
組立て方法はYoutubeに動画が在ったので活用させて頂いた。
◎
PRUSA i3 Full Bear Upgrade Kit - Part 1 - Frame
動画でアルミ製V溝棒による骨格の組立てを説明している。
下の不思議な形の物は、縦の柱を固定する際に位置を決める定規だった。
自分はノギスを使ったので不要だった。
GitHubにも骨格の図面がある。
PRUSA i3 Bear Full Upgrade MK2.5
◎
PRUSA i3 Full Bear Upgrade Kit - Part 2 - X-Axis and Extruder
動画では、X軸右側のベルト用プーリーに使うシャフトはM3のビスを切り出して使うように説明している。
しかしキットには専用のシャフトが入っていた。しかし直径が僅かに太くてプーリーの穴に入らなかった。
仕方なく電動ドライバーの先にシャフトを取り付け、回しながら砥石に当てて少し細く削った。
下の写真はシャフトがプーリーの穴へ収まったところだ。
動画にはエクストルーダの最上部にあるフィラメント検出器の説明が無い。
そこで試行錯誤しながら組み立てた。この部分は2個の棒状永久磁石と1個の鋼球で構成されている。
2個の磁石を吸引するように組み込まねばならないが、これが判らず反発するように入れてしまった。
下の写真は左がフィラメント無し、右がフィラメントを入れた状態だ。長い永久磁石が開いている。
下の治具はエクストルーダー内に組み込むテフロンパイプを加工するための道具だ。
長さと端部の加工をカッターナイフで行えるように工夫したようだ。
しかしキットに付属してきたテフロンパイプは加工済みだったので使わなかった。
補修作業の際には使うかもしれない。
◎
PRUSA i3 Full Bear Upgrade Kit - Part 3 - Final Build
この動画ではX軸とY軸の取り付けや電気配線などを行っている。
Y軸のキャリッジへリニヤベアリングを取り付ける方法が、
キットでは動画と違ってUボルトだったが他は同じだ。
この動画では組み立てて完成のような雰囲気だが、実は違う。
肝心の自己診断の部分が動画には無い。
自己診断で不合格を連発し原因を究明するのが大変だった。
5. 自己診断
この3Dプリンターには
自己診断機能が備わっている。XYZの各軸の移動距離を自動的に測定しファームウエアに
設定された距離と異なると不合格(Faile)になる。これは簡単に合格した。
ところが次のZ Calibrationで躓いた。Z軸の上限からノズルがベッドに当たるまでの距離を測るのだがFaileになる。
試行錯誤を繰り返して
Z軸の上端にあるストッパーを3mm上方向へ移動させたところ合格になった。
本来はオレンジ色のZ軸上端部品がアルミの骨格と同じ高さになる筈?なのだが、3mm高く取り付けた。
アルミ骨材の端面を覆うオリジナルのカバーが合わなくなったので、自分で設計し青いPLAで印刷した。
その後のCalibrationは恙なく合格した。
First Layer calibrationで
ノズルの高さを合わせて印刷準備が整った。
6. 試運転
First Layer calibrationで使った白色のPLAフィラメントを使って試験印刷を行った。
印刷したのはキットに同梱されていたSDカードに入っていた
MakerBot
Gnomeだ。大きさはsmallで、高さが60mm。
印刷結果を見て出来の良さに驚いた。表面が滑らかで積層痕など全く見えない。申し分なく素晴らしい性能だ。
PLAフィラメントでの印刷が上々の出来栄えだったので、PETGフィラメントでも試した。
印刷したのは、自分で設計した小箱だ。小型の電子回路を収める箱を想定した。
大きさは縦30mm、横40mm、高さ20mm、壁の厚さ1.2mm。
結果は大成功だった。以前に使っていたJGAURARO A3では、難しかったPETGを簡単に印刷した。
このプリンターはPETGの印刷が上手だ。これならばPLAやABSは必要無さそうだ。
小箱の印刷が上手く出来たので、前出のZ軸上端カバーをPETGフィラメントで印刷してみた。
青はPLAフィラメント、黒と白はPETGフィラメントで印刷した。何れも遜色無い出来栄えだ。
WebにはPETGでの印刷は難しいとの評価が多いが、
我がBear upgrade PRUSAはPETGフィラメントを上手く印刷できる。
PETGはノズル温度230℃、ベッド温度85℃、内部充填15%で印刷した。
撮影に試用したデジカメのラチチュードが狭い為か白いPETG製が上手く写っていないが、綺麗に印刷されている。
黒色PETGフィラメントは
SUNLU製、白色PETGフィラメントは
eSUN製を使った。
7. Z軸最上部の補強
Z軸の最上部には駆動部の保護用部品が付いている。下の写真のオレンジ色の部品だ。
過日、ここに手を付いたらカクカクと緩んだ感じがした。
本来は手を付くような場所では無いので強度を見込んでないようだ。
歳のせいか無意識に高い場所に手を触れて体の安定を保つ癖がついたようだ。
そこで補強した互換部品を設計しPETGフィラメントで印刷した。
下の写真で黒いのが自分で設計製作した補強部品で縦方向は46mmだ。
対してオレンジ色のオリジナルは17.5mmと短い。下方向の耐加重は想定してないのだろう。
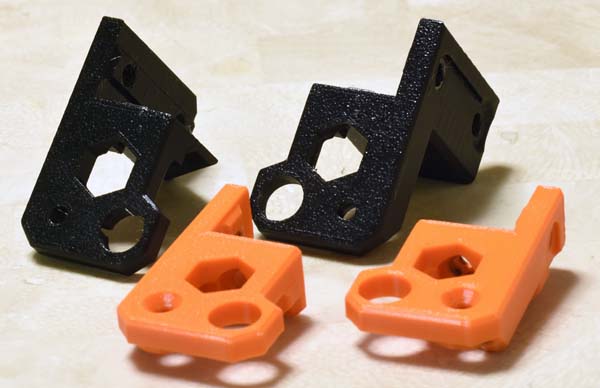
この印刷ではベッドにテクスチャー柄のバネ鋼板を使った。
ベッドのバネ鋼板を平滑からテクスチャー柄に変えたのでLive Zの修正が面倒だったが、上手く模様が転写された。
Clone_PRUSAは平滑2種、テクスチャー2種のLive Zを個別に覚える。面倒でも一度設定すれば後は楽チンだ。
PETGはノズル温度230℃、ベッド温度80℃、内部充填30%で印刷した。
従前はベッド温度を85℃にしていたが、最下層の剥離が多いので下げた。結果は判らない。
PETGで強度が必要な印刷は初めてだったが、取り付けた部品に体重を掛けても割れなかった。
補強は大成功だ。PETGの層間癒着は素晴らしく強い。
PETGによって本格的な工作にも3Dプリンターが使える。画期的なフィラメントだ。
補強部品によってBear upgrade PRUSAの両肩の部分が黒色になり、少しイメージが変わった。
このデーターを
thingiverseへ掲示しました。
8. P.I.N.D.Aの再設定
PETGで印刷の試験をした際に事故が起こった。印刷したのは直径5cm、厚さ0.5mmの円盤だ。
試験の目的はベッドへの定着の具合を評価する為だった。
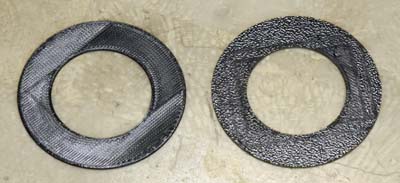
印刷中に円盤の端部が剥がれ、ノズルの力でロールケーキのように巻かれて直径5mm程度の棒が出来てしまった。
ABSやPLAのフィラメントでは、印刷物が剥がれても棒状にはならないのでPETG特有の現象だ。
そのPETGの棒がP.I.N.D.Aの下部に挟まりP.I.N.D.Aを上へ2mmほど押し上げて狂ってしまった。
その後にBear upgrade PRUSAのコンピューターがクラッシュを検出して自動的に印刷を中断した。
P.I.N.D.Aはノズルとベットの距離を測るセンサーだ。
Bear upgrade PRUSAのベッドには高さ調節ノブが無い。
総てP.I.N.D.Aの信号を基にコンピュータが制御する。
これが狂うと印刷がメチャクチャになるので再設定をした。
ノズルをベッドへ当てて高さゼロの状態にしてP.I.N.D.Aを高さ1mmに合わせた。
その後にFirst layer calibration を行い、Live adjust Z
を設定した。その説明はコチラ。
その値は下のようになった。
バネ鋼板 が Texture1 の場合の
Adjusting Z : -2.025
バネ鋼板 が Smooth1 の場合の
Adjusting Z : -1.803
狂う前の値は下記のようだった。
バネ鋼板 が Texture1 の場合の
Adjusting Z : -0.925
バネ鋼板 が Smooth1 の場合の Adjusting Z : -0.700
値が違うのはP.I.N.D.Aを高さを1mmに合わせる際の誤差に起因していると思われる。
Sheetが Texture1 の場合とSmooth1の場合で違うのは、
Smooth1には表面に3M製フィルムが貼って在るからだ。
9. 定着の工夫
PETGを使い、薄い円盤を印刷した試験で良い感じだったので少し大きな物の印刷を試みた。
印刷したのはBear upgrade PRUSAの液晶部を覆うカバーだ。
キットに付属していた物は、製造不良で液晶表示窓の端が小さく割れていたので接着して使っていた。
組み立てた当初からPETGが印刷できるようになったら作り直したいと考えていた。
黒色のPETGで印刷したところPRUSAと書かれた文字の部分が剥離して失敗してしまった。
PLAフィラメントやABSを使った場合には、部分剥離を起こした事は無い。PETG特有の現象だ。
仕方なくバネ鋼板に髪型を整えるケープを薄く吹きかけて印刷したところ上手く定着した。
バネ鋼板はTextureを使ったが、ケープはスプレーなので布目模様を潰す事が無く具合が良かった。
印刷物を外す際もバネ鋼板を軽く捩るだけでパリッと音がして簡単に取れた。
バネ鋼板は素晴らしい発明だ。
印刷が完了した液晶部カバーをプリンター本体へ取り付けたのが下の写真だ。
写真では判り辛いが、購入品よりも精緻に印刷されている。
液晶部カバーにはClone PRUSAと書いてある。
Bear upgrade PRUSAにOriginal Purusaと表記しては、開発したJosef PRUSA氏に対して失礼だと考えた。
このカバーのSTLファイルは
Thingiverseから頂きました。
この印刷では布目模様を潰さない為にスプレーのケープを使った。
上の写真の様にバネ鋼板がSmoothの場合にはスティック糊でも大丈夫だ。
写真のスティック糊はJGAURAR 3Aの為に約3年前にダイソーで買った。
ケープもダイソー糊も水溶性なので使用後は、バネ鋼板を水洗いすれば簡単に落とせる。
スクレーパーのように傷を作る可能性は少なく簡単な掃除方法だ。
10. OctoPrintの組込み
プリンターにラズベリーパイという名称の超小型コンピューターを組み込むとWiFiで操作できる。
3Dプリンターをパソコンから離れた場所に置けるので案外に便利だった。
その説明は
PRUSA
RESEARCH社のホームページに在る。記載の通りに作業して成功した。
引っ掛ったのはIPアドレスだ。
プリンターの本体にIPアドレスが表示される筈なのだが電源を入れても表示されなかった。
暫くしたら表示されたが、今でも表示されるタイミングが判らない。
ブラウザーをWiFiルーターに接続し、
DHCPが割り付けているIPアドレスで数字の一番大きな物がラズベリーパイだと推定し、
ブラウザーにIPアドレスを入力して接続した。
電源投入後にブラウザーに画面が出るまでに5分程度掛かった。兎に角遅い。
当初、応答が遅いのが判らず何度もやり直して時間を浪費してしまった。
接続が確認された後にDHCPの割付を自動から固定へ変更した。
10-1
購入資材は下記の2点だけ。
Raspberry Pi Zero W は
スイッチサイエンス社から購入した。同社が最安値だった。
Rasberry Pi Zero WHは似ているが使えないので要注意だ。
GPIO Headerは指定された寸法の市販品が見つからなかった。
仕方なく
AMAZONから近い物を購入し改造して所定の長さに合わせた。
10-2 遠隔操作以外の機能
印刷に関係する操作以外に下記のような素晴らしい機能がある。
(1)TVカメラを取り付けられる。
これはPRUSA RESEARCH社のホームページには書いて無い。
3Dプリンターをパソコンから離れた場所に置いた場合に、印刷の状態が見られる。
想定外に便利だ。下の写真では液晶のカバーを印刷している動画を映している。
駒撮り撮影も出来るようだが使っていない。
購入した機材はカメラとケーブルだけだ。
Raspberry Pi Camera
AMAZONから購入。たったの780円だった。
Raspberry Pi Zero用カメラケーブル 上記カメラに付属のケーブルはRaspberry Pi 用でZeroには使えない。
Raspberry Pi Zero用30cmのケーブルをAMAZONから購入した。
カメラは下の写真の様にX軸駆動モーターへ取り付けた。青い小箱がカメラだ。
(2)ベッドの凹凸を把握できる。
OctoPrintへ
Githubからプラグインを組み込むとPrusaMeshMapが使える。
これはベッドの傾きを図示してくれる便利な機能だ。
下の図で青い部分が低く、黄色い部分が高い所だ。
このプラグインには癖がある。上にある長い横棒を押すと
メッシュベッドレべリングを始める。測定を終えても画像には結果が反映されず、
30秒程度経過の後に下のReloadボタンを押すと結果が表示される。
上の図は自分のプリンターの凹凸を測定した結果だ。中央が低く周辺が高い。
この状態で印刷しても影響は見られなかったが、できれば改善したい。
しかしOriginal PRUSAには調節機構が無い。当然Bear upgrade PRUSAにも無い。
Youtubeには
Nylock Bed
Levelingなるナイロンナットを使った方法が紹介されている。
それに使う治具を作った人もいる。
自分は、時間経過と共に狂いそうな気がするので乗り気がしない。
11. JGAURARO A3 のBear upgrade PRUSA化計画 2019,11,11 開始
Bear upgrade PRUSAが完成して以降JGAURARO A3を全く使わなくなった。PRUSAは圧倒的に使い易いからだ。
使わなくなったJGAURARO A3を捨てようかと考えたが、勿体無いし若干の罪悪感もある。
そこでJGAURARO A3の部品を使って、もう一台のBear upgrade PRUSAを作ることにした。
使える部品を活用し、足りない部品はAliexpress等から買い足して纏める方針だ。
費用はキットの半額程度で済む筈だ。成功するか失敗するか判らないが計画を実行へ移した。
11-1 フレームの組立て
フレームのキットは
Aliexpressに出店している
Funssor Official Storeから購入した。
現時点(11/28)では81.25$だが、注文した11月11日は特売日で69.12$だった。
輸送費は無料で、注文してから10日間で手元へ届いた。
組み立てようとしたらネジが締まらない。
Tナットを抜けたネジが長過ぎてアルミ棒の壁に衝突してしまう。
M5*10mm 64pcsと書かれた袋に入っていたネジは長さが12mmも在った。
他にM5*12mm 12pcsと書かれた袋に入っていたネジと中身が同じだった。
販売店にメールでネジの寸法が間違っていると指摘したところ、
正しい品を送るから新たに何か買ってくれないかとの返事。送料の出費が嫌なのだろう。
何もいらないと答えたら、その後連絡が無い。
待ってられないので、近所のホームセンターでM5のワッシャーとスプリングワッシャーを買い、
これをM5*12mmのネジに挟み込んで長さを調節してフレームを組み立てた。出費は352円で済んだ。
スプリングワッシャーを組み込んだほうが強度が上がる筈なので怪我の功名か。
組立てには、前回のBear upgrade PRUSAのキットに含まれていた柱の位置を決める治具が活躍した。
組立ての寸法は
Githubの資料に従った。寸法はノギスを使い正確に測った。
下の写真で左側が過日組み立てたBear upgrade PRUSAのキットで右が新作のフレームだ。
フレームのキットには、この部分では使わないタイラップが20本くらい入っていた、
X軸やY軸の組立てでは沢山使うので有難いが ? である。
11-2 プラスチック部品の印刷
組立てに必要な部品をBear upgrade PRUSAで印刷した。主にZ軸とY軸用に使う小さいものを作った。
フィラメントにはPETGを使った。Bear upgrade PRUSAはPETGをPLAのように楽々と印刷する。
PETGの御蔭で強靭な部品が出来上がった。部品のデーターは
Githubからダウンロードした。
上の写真に在るものが使用するプラスチック部品の総てではない。
コンピュータを収納する箱やLCDのカバーなどの大物が無い。これから印刷する予定だ。
11-3 Y軸キャリッジの組込み
JGAURORA A3のY軸用すべり棒を移植したのだが、PRUSA MK3よりも50mmも長い。
ロッドホルダーの設計を貫通形に改造し、本体の後部へ突き出す形にした。
元々後部にはY軸やエクストルーダへ繋がる電線が動くための空間が必要なので、
設置面積の拡大等の実害は全く無い。チョット格好が悪いだけだ。
Z軸の台形ネジ付モーターもJGAURORA A3から移植した物だ。
この後。モーターのコイルを調べたところ2Ω前後だった。
PRUSA i3 MK3用は5Ω前後なので電圧が違うのが判明した。
つまり
JGAURORA A3用モーターはPRUSA i3 MK3用には使えないのだ。
仕方なくモーター3個を
Aliexpressへ追加発注した。想定外の痛い出費だ。
Z軸用すべり棒はPRUSA i3 MK3用と同じ寸法だったので、そのまま移植できた。
Y軸用キャリッジは
Aliexpressに出店している
FYSETC 2th Storeから買った。
付属品は、リニヤベアリングが3個、Uボルトが3個、ナイロンナットが6個だった。
商品に問題は無かったが、
深圳市から埼玉県南部までの輸送に53日間も掛かった。
輸送業者はChina postだった。普通は10日前後で届く筈なのだが。
Y軸アイドラーは以前にAMAZONから買ったGT2用プーリーを使った。
穴径は3mmだったので、軸にはM3*20mmのビスとナイロンナットを使った。
元々の設計が、そのようになっている。
Bear upgrade PRUSAで印刷した部品は、どれも精度が良く問題は起きていない。
11-4 ヒートベッド他の組込み
Y軸のキャリッジにヒートベッドを取り付けた。
前後方向には滑らかに動くが、ガタツキは全く無い。素晴らしい精度だ。
ベッドの上に載っているのは、これから使うプラスチック部品を印刷したものだ。
3色のPETGを使い分けて印刷した。
残りはコンピュータ収納箱の蓋とX軸の右側アイドラーだけになった。
磁石付ヒートベッドは
Aliexpressから買った。
ベッド以外に電線やネジなどの必要な部品が付属していた。付属のスペーサーはアルミ製だった。
前に作ったBear upgrade PRUSA kitではスペーサーがステンレス製で磁力で吸い寄せられ作業しづらかった。
11-5 液晶表示部の組込み
液晶表示基板と制御用コンピュータも
Aliexpressから買った。
この液晶表示基板には二つの問題点があった。
普通のBear upgrade PRUSA用液晶にはコントラスト調節用可変抵抗は無いのだが、
この基板ではそれが在った。
それが基板を支える右側のLCD supportに当たって取り付けられない。
仕方なく下の写真のように設計を手直しして可変抵抗の位置に切欠を設けた。
また前面にあるロータリーエンコーダのシャフトが長く、1cmも在った。
Original PRUSAのシャフトでは5mm位なのでOriginal のノブは不恰好だ。
仕方なく新たにノブを設計製作した。下の写真の赤いのがノブだ。
一見変な形に見えるが、指一本で回せるように工夫した。
Bear upgrade PRUSAに付いているオリジナルのノブよりも扱い易い筈だ。
液晶のカバーは、今回もClone PRUSAだ。白色のPETGを使った。
電線は下の写真の様にケーブルクリップでアルミフレームへ固定した。
固定に使ったケーブルクリップはBear upgrade PRUSAで印刷した。
同じ物を何度も印刷するのは面倒だったので、まとめて一度で済ませた素材はオレンジ色のPETGだ。
当初はキッチリ固定できるのか懐疑的だったが、杞憂だった。
しっかりと電線を固定できた。素晴らしい設計技術だ。
11-6 X軸の製作
モーターが付く左端の印刷データは
Thingiverseから頂いた。
Original PRUSA i3 MK3はリニヤベアリングを嵌め込むだけの構造だが、
これはビスナットで締め付ける構造に改良されている。
先に作ったBear upgrade PRUSAキットでも、これを使っていた。
アイドラーだけの右端はGithubからOriginal PRUSA i3 MK2用を頂いた。
X軸用のすべり棒もY軸と同様にJGAURARO A3の物を移植した。
これがOriginal PRUSA i3 MK3用よりも10mm程度長い。
その差を吸収する為に右端は改造が必要だった。
Original PRUSA用のほうが構造が単純で設計の修正が容易だった。
X軸の両端は、すべり棒やリニヤベアリングを嵌め込む構造なので高い精度が要求される。
上手く印刷できるか心配だったが、我がBear upgrade PRUSAは問題無く印刷した。
もちろんフィラメントはPETGだ。
11-7 コンピュータの組込み
コンピュータ基板を収納する箱の印刷が終わった。フィラメントは黒色のPETGだ。
コンピュータを固定する側のケースは大きく複雑で印刷に5時間半ほど掛かった。
蓋はZ方向が浅いので4時間程度で済んだ。印刷の精度が高く箱と蓋の噛み合わせはピッタリだった。
以前に作ったBear upgrade PRUSA kitよりも精緻な出来栄えだ。
コンピュータは
Aliexpressから購入した。コンピュータの基板以外にUSBケーブルが付属していた。
静電気防止の袋に入り、衝撃防止材入りの箱で丁寧に梱包されていた。注文から13日で届いた。
印刷したコンピュータ収納箱に電源、ヒートベッド、LCDの配線を済ませ試しに通電してみた。
しかしLCDが暗いままで何も表示しない。バックライトも点灯しなかった。
コンピューターの異常でもLCDのバックライトは点灯する筈だ。
それにコンピューターの基板にある電源パイロットLEDは点灯した。
問題の原因はLCDに在りそうだった。
そこで解体して取り出したJGAURARO A3のLCDを接続したところバックライトが点灯し文字が出た。
コンピュータには、最初からOriginal PRUSA用のファームウエアが書き込まれていた。
Arduino IDEを使って書き込まねばならないのかと考えていたが、手間が省けた。
下の写真で左上が動かないLCD,右下がJGAURARO A3のLCDだ。
良く見たところケーブルが出ている方向が変だ。下に出る筈なのだが、上に出ていた。
基板上のヘッダーを逆に半田付けしたのか、ケーブルの製作に間違いが在ったのではと疑った。
何れにしても、そのままではケーブルを反転して刺し込めない。
仕方なく基板のヘッダーにニッパーで逆入防止の突起が入る切り欠きを作って下の写真の様に接続した。
これで通電したところLCDは正常に機能し、自己診断の実行を促すメッセージが表示された。
しかし正しい電圧のモーターを取り付けてないので、まだ自己診断は実行できない。
JGAURARO A3のLCDは、機能的にはBear upgrade PRUSA用と同じだが、
基盤の大きさが縦横共に1mmほど大きくケースに入らなかった。
ヤスリで削れば収まると思われるが作業が面倒なので新規購入品を使った。
11-8 モーターの交換
Aliexpressへ注文していたモーターセットが届いた。
そこで仮に取り付けていたAGAURARO A3用モータを外して新しいモーターを取り付けた。
今度のモーターは
電線が配線ルートに合わせた長さになっていた。
電線をコンピュータまで引き回すルートはモーターの場所により違う。
コンピューターに近い左側Z軸モーターでは電線が短くて済むが、
右側Z軸モーターやX軸モーターでは長くなければ接続できない。
以前に組み立てたBear
upgrade Prusa kitでは電線の長さが同じで、
コンピュータ収納箱の中に電線がとぐろを巻いて始末に困ったが、
今回はスッキリしている。今回買ったモーターは使い易い。
Bear upgrade Prusaを組み立てる過程で半田付け作業は無い。
電線の接続はコネクターをコンピュータ基板へ差し込むだけだ。
モーターの接続もコネクターだ。
上の写真でZ軸モーターにはリードスクリューナットが無い。
リードスクリューナットとは台形ネジと噛合ってZ軸を上下させる特殊なナットだ。
ところが
届いた実物にはリードスクリューナットが付いていた。
下の写真の黒くて平たいナットがそれだ。材質は自己潤滑性プラスチック (デルリン) の様だ。
モーターを注文した際に
Aliexpressの別の店へリードスクリューナットを注文した。
届いた物は、穴が4mmでM4のビスが付属していた。PRUSA i3は3mmだ。
Webの商品説明ではM3のビス・ナットが付属と書いてあるが、良く写真を見るとM4の様だ。
Z軸モーターにリードスクリューナットが付属していたので、
台形ネジへ捻じ込んで遊びの少ない2個を使った。残りの2個は余ってしまった。
AliexpressはWebの商品説明で正確に仕様を把握するのが難しい。
それでも価格の廉さは魅力的だ。
XYZ軸のモーター交換が済んだので
回転方向を確認した。
Y軸とZ軸は正しかったのだがX軸は逆だった。電線を入れ替えれば修正できるが面倒だった。
購入したモーターセットには5個のモータが在りエクストルーダに使う1個が余っていた。
電線の長さも合いそうだったので、これをX軸に取り付けて回転方向を修正した。
エクストルーダはキットを買ったのでモーターが含まれていた。
よってモーターが1個余る。丁度良かった。
11-9 エクストルーダーの組立て
エクストルーダーも
Aliexpressに出店している所から買った。
下の写真は、エクストルーダーを組み立てて本体へ取り付けた様子だ。
外観は完成状態の様に見えるが、残念ながら複数の問題が在った。
問題1:電線の束が太い
コンピュータを収納している箱へ差し込むエクストルーダからの電線の束が太過ぎる。
そのため固定するケーブルクリップが完全に締まらずドアも閉じない。
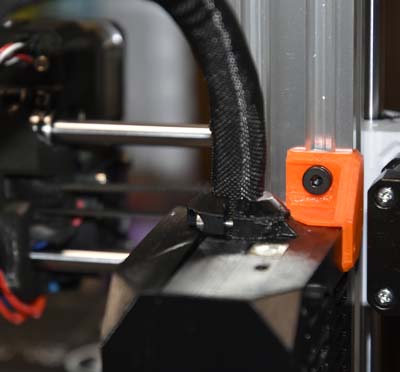
電線束の太さは、前作のKitでは直径13mmだが、これは14.5mmも在る。
原因は使っている電線が不必要に太いからだ。交換が必要だ。
問題2:ホットエンドのサーミスタに邪魔なコネクターが在る
ホットエンドの温度を測るサーミスタの先端から5cmのところに大きなコネクターが在る。
これが邪魔で上手く処置できない。下にするとノズルよりも低くなってしまう。
横にするとX軸ゼロ点の検出を妨害しXYZ CalibrationがErrorになってしまう。
普通は半田付けで接続し細く仕上げてあるのだが、なぜこんなことをしたのだろうか?。
Webの商品を紹介する写真でも半田付けで接続している。半田付けに修正する予定だ。
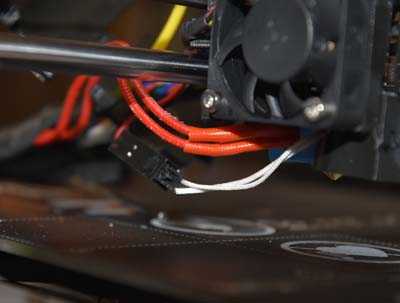
後日、このサーミスタは
amazonから買った物へ交換した。
コネクターが無く電線も細いので具合が良かったのだが、先端の保護管が無い。
そこだけは前のサーミスタから外して使った。
問題3:印刷された部品の精度が低い
このエクストルーダには3Dプリンターで印刷された部品が沢山使われている。
それらの寸法精度が低い。
PINDAと呼ばれる近接センサーを取り付け穴はC形の筈だが、癒着してO形になっていた
仕方なく鋸で巾1mm位の切れ目を入れた。
フィラメントセンサーではPLAで印刷された検出レバーが滑らかに動かず時折引っ掛る。
上端のカバーがカッチリと固定できない。
Bear up PRUSA用エクストルーダの印刷
PETGを使って下の写真のようにBear upgrade Prusa用エクストルーダの部品を印刷した。
今度のはOriginal Prusaのコピーではなく
ThingiverseのGrégoire Saunierの設計を頂いた。
昨年に完成させたBear upgrade Prusa kitのエクストルーダも同じ物だった。
Original PRUSAの物と機能は同じだが部品数が少なく組み立てやすい。
Aliexpressから買ったエクストルーダーキットの部品を再利用して
新しいエクストルーダを組み立てる予定だ。
新エクストルーダ完成
上の写真の部品を使って新エクストルーダを組み立てた。
組立てには
Bear
Labの
エクストルーダ組立てガイドを参照した。
Original PRUSAのコピーに比べて配線の処理が楽だった。
PTFEチューブの交換
Bear
Labの
エクストルーダ組立てガイドを読んだ。
その中の注意書きにBear upgrade Prusaの中に使われているPTFEチューブは
PRUSA i3MK3用と長さが違うと書かれていた。
PRUSA i3MK3用は44.2mm、Bear PRUSA用は50mmだ。5.8mmも長い!!。
新エクストルーダはPRUSA i3MK3用エクストルーダを解体し、
その部品を使ってBear upgrade Prusa用に組み替えたので短い筈だった。
調べる為にフィラメントを送るギヤの横扉を開けて中を覗き込んだ。
送りギヤの直下にPTFEチューブの先端が見える筈だが見えなかった。
やはり
PTFEチューブが短い。
そこでPTFEチューブを新規に製作し組み込んだ。
必要なチューブは内径2mm、外径4mm、長さは50mmだが、そんなに短い商品は見つからなかった。
仕方なく
amazonで1mのPTFEチューブを2個買った。
1mのPTFEチューブから
治具とカッターナイフを使って切り出し両端を加工した。
出側は外側を円錐形に尖らせた。
入り側は内部を30度の角度でラッパ上に広げた。これでフィラメントが差し込みやすくなる。
CNCフライスで回路基板を切削する際に使うVカッターが30度だった。
下の写真は上から旧PTFEパイプ、新PTFEパイプ、Vカッター、チューブ加工用治具だ。
完成したチューブをエクストルーダへ組み込んだところ
長さはフィラメント送り歯車の直下まで届きピッタリだった。
エクストルーダを3Dプリンター本体へ取り付け
フィラメントのAutoloadを実行したところ滑らかに吸い込まれた。
11-10 自己診断の実施
Bear up PRUSAがの組立てが完了した。
従前の写真との差異は、エクストルーダをBear Labが設計した物に変えてある。
また自作したスプールスタンドを取り付け、PLAフィラメントを載せている。
PRUSA i3のファームウエアには
Wizard と呼ばれる自己診断機能が組み込まれている。
これによって組立てが正しく行われたか診断する。
一度はWizardを行わないと3Dプリンターを起動する度に実施を促す表示がLCDに出る。
Wizardを実施したところ
Self tesでX軸、Y軸、Z軸で問題点を指摘された。
(1) X軸駆動系
ベルトが緩いとの指摘。張りを調節するのを忘れていた為だった。
X軸の右端にある張力調節部を適切に調整して合格。
(2) Y軸駆動系
Y軸の動作距離が異常と指摘された。
このPRUSAには位置決めの為のリミットスイッチが一つも無い。
位置決めは可動部を固定部に衝突させ、モーター電流の変化で検出している様だ。
Y軸の場合はリニヤベアリングが滑り棒用ホルダーに当たる位置だ。
そこでリニヤベアリングの位置を変え試行錯誤を繰り返した。
その結果リニヤベアリングの固定位置を下の写真の様に中央へ寄せて合格になった。
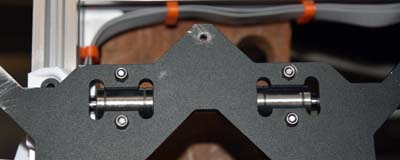
後のなって判ったのだが、これが異常だった。
正常ならばベアリング固定ナットの位置に
リニヤベアリングの中央が揃う様に固定すれば合格する筈だ。
(3) Z軸駆動系
当初Z軸の動作距離は異常と指摘されたが、想定内だった。
前作のKitで経験済みだったので、やっぱりかと思った。
Bear
Labの
エクストルーダ組立てガイドを良く読んで調べたところ
Bear up PRUSAのエクストルーダーはOriginal
PRUSAよりもZ方向が2mm長い。
そのためOriginal
PRUSA用のファームウエアでは合格しないとの記述があった。
GithubにBear up
PRUSA用のファームウエアが在ったので、これを入れて合格になった。
しかしOriginal
PRUSA用のファームウエアが使えないのでは甚だ不便だ。
そこで前作と同様にZ軸駆動モーターを上へ3mmだけ持ち上げて
Original PRUSA用のファームウエアでも合格した。この段階で
Self
testは合格した。
Wizardは続けて
XYZ calibrationを実施した。ここでは下記のような異常の指摘が在った。
"XYZ calibration failed. Please consult
the manual."
PRUSAリサーチ社の解説では、原因は下記のようだ。
= Calibration point was not found at all.
しかし
XYZ calibrationの実行中にPINDAの軌跡を見ていると
ヒートベッドの四隅に在るCalibration pointの丸印の周囲を旋回していた。
総てのCalibration pointが見つからないという状況ではない。
四隅総てのCalibration pointを検出しているように見えた。
原因を探るべくWebで情報を集めたが自分の状況と合致する物が見つからない。
原因が判らず試行錯誤を繰り返して一週間も経過してしまった。
その後、Y軸用リニヤベアリングの位置が変だった事を思い出し、
若しや歯付ベルトに原因があるのではと疑った。
Y軸のベルトはJGAURARO A3からの使い回しだった。
手元に以前買った2GTベルトが在ったので張り替えてみた。
リニヤベアリングの位置も調節代の中央へ戻してから
Wizerdを最初から実行したらXYZ Calibrationに合格した。
続けてFirst layer calibrationを行い、
Live adjust Zの設定を終えたところLCDに下記のような表示が出た。
めでたく総ての検査に合格した。
原因となったベルトを比べてみた。
下の写真で上側がJGAURARO A3から流用した無印のベルト。
下側がXYZ Calibrationに合格した2GTベルトだ。
無印は歯のピッチが僅かに広い。
Wizardはヒートベッドの四隅に在るCalibration pointの間隔を測定し、
ベルトのピッチが許容誤差に収まっていないのを検出したのだ。凄い!!。
この
XYZ calibrationは個人用3Dプリンターの範疇を越える素晴らしいものだ。
それにしても、つまらない所をケチって時間を無駄にしてしまった。
AlliExpressには多くの2GTタイミングベルトが出品されている。
写真で見ると型式の印刷が無いものも沢山ある。
中国内で規格が徹底してないのかも知れず要注意だ。
11-11 X軸不調
Wizardには合格したが、X軸が変だ。電源を切るとX軸の左側が僅かに下がる。
X軸の左側にはX軸駆動モーターが在り重いので下がるのかと考えたが、そうではなかった。
下の写真の様にX軸のモータ固定部を外して滑り棒に曲尺を当てて直角か調べたところ、
右端に比べてモーター側は5mm位下がっていた。つまり印刷した
X-end-motorが歪んでいた。
3Dプリンターは印刷の際の方向によって誤差が異なる。
前作のKitではX軸はー0.25%、Y軸はー0.5%の誤差がある。
この誤差を打ち消すためには印刷方向を揃えれば良い筈だ。
下の図の様にスライサーに部品のSTLファイルを読み込み比べてみたところ揃っていなかった。
X-end-motorと
Z-topの向きが適切ではない。
そこでX軸に関係する部品を何度か印刷してX軸とZ軸の滑り棒が直角になるようにした。
これで電源OFFの際のX軸左端沈下は大幅に改善された。
11-12 Z軸不調
Z軸を上下させると稀に脱調の音が聞こえる。
調べてみるとZ軸を動かす左右の台形ネジが平行ではない。
間隔が下に比べて上で2mmほど広かった。印刷誤差にしては大きすぎる。
情報を求めてwebを探したところ、Githubに
Bear
Upgrade 2.1が在った。
早速ダウンロードして印刷し組み込んだところ問題は解消した。
下の写真で左がBear Upgrade 2.1、右が旧作だ。
11-13 試運転
問題は総て解消したので試運転を行った。
前回のBear upgrade PRUSA kitを作った際には、添付されていたSDカードに入っていたMakerBot Gnomeを印刷した。
そのSDカードを雑な扱いで割ってしまったので新たに
Tingiverseからダウンロードして印刷した。
大きさを前作と合わせる為に60%へと縮小した。
下の写真で左が新作のPLA、中央が新作のPATG、右が前作のPLAだ。どれも遜色のない素晴らしい出来栄えだ。
PETGはオレンジ色の半透明なので陰影の部分が判り辛いが、他と同じように成型されている。
Bear upgrade PRUSAはPETGでも上手に印刷する。
試運転が成功し新Bear upgrade2.1 PRUSAが完成した。
左が
Trianglelab社のKitを組み立てた前作。
右が今回の部品を集めて作ったBear upgrade2.1 PRUSAで機能は同じだ。
完成の御祝いにPRUSA RESERCH社も大好き?なHARIBO GOLDENBEARを買った。
凄く硬いグミだが味も食感も自分好みだ。
妻が、これを噛んで奥歯に被せてあったプラスチックが外れて顰蹙を買った。
11-14 JGAURARO A3 のBear upgrade PRUSA化計画のまとめ
この
計画は失敗だった。Bear upgrade PRUSAは完成したが、
本来の目的である”GAURARO A3 を解体した部品の活用”は出来なかった。
僅かに使えたのはXYZ軸の滑り棒とベルト駆動歯車、ネジ類だけだ。
JGAURARO A3のX軸滑り棒はPRUSA用に比べて10mm長い。
そこでX軸右側スプールを改造設計し滑り棒を収める穴を延伸した。
垂直面に見える火山のような膨らみがそれだ。
JGAURARO A3のY軸滑り棒はPRUSA用に比べて45mmも長いので
Y軸滑り棒受けを改造設計し、Y軸滑り棒を本体後部へ突き出して取り付けた。
Z軸の滑り棒はPRUSA用と同じ長さだったので加工は無しで済んだ。
リニヤベアリングは同じ規格なので使える筈だったが、
手で触れた際のガタツキが大きかったので国産品に替えた。
この計画に掛かった総費用は4万円弱だった。
AliExpressでclone prusa i3 mk3sと検索すると沢山のPRUSA互換機が売られている。
それらは輸送費を含めても4万円から5万円程度で買える。但し品質は判らない。
この計画では少し廉くBear upgrade PRUSAを入手できたが、計画が成功と言える程の差ではない。
しかし計画を始めてから4ヶ月の間は、これに熱中して楽しい時間を過ごせた。
また実用に耐える素晴らしい3Dプリンターが2台に増えた。
その意味では、計画は成功かもしれない。
11-15 部品購入業者の評価
部品は主にAliexpressに出店している業者から買った。それらを評価した。
今後X印が付いた業者からは買わないようにする。
品 名 |
購 入 先 |
金 額 |
評価 |
備 考 |
アルミ骨格 |
Funssor Official Store |
$69.12- |
× |
M5*10mmのビスが12mmだった。指摘したが対応無し。仕方なく自腹で対処した。 |
制御用コンピュータ基板 |
FYSETC 1th Store |
$59.34- |
○ |
問題なし。良質のコンデンサを使った高級品。Aliexpressには機能互換の廉価品も存在する。 |
Y軸用キャリッジ |
FYSETC 2th Store |
$14.32- |
○ |
問題なし。付属のリニヤベアリングは国産ではないが良品だった。 |
オリジナルペイ春鋼板 |
BIQU Global Store |
$12.5- |
○ |
問題なし。春鋼板とはSpring Steel Sheetの意味だ。自動翻訳か?。 |
ステッピングモーター 1式 |
FYSETC 1th Store |
$67.55- |
△ |
無い筈のリードスクリュー用ナットが付属していた。商品管理に問題が在るかも。 |
リードスクリュー用ナット |
3D SJIE TECH Store |
$4.18- |
○ |
ステッピングモータに付属していたので不要だった。 |
磁石付きヒートベッド |
Sealand |
$39.51- |
○ |
加温通電モニター用LED付きの高級品。先に作ったKitには無かった。 |
エクストルーダキット |
cn1514408019szbo |
$63.18- |
× |
印刷部品精度が低い、サーミスタの仕様が違い使えない。 |
ホットエンド用サーミスタ |
amazon (HALJIA ) |
\890- |
○ |
Aliexpressでは遅いのでamazonから購入。必用なのは1個だが5個入りで勿体無い。 |
電源箱 |
ヤフオクで落札 |
\2,873- |
△ |
新品未使用純正との商品説明、消費電流の変化に対応して雑音が出る。 |
ゴム足 |
島忠ホームズ |
\600- |
○ |
別の用途で売られていた。 |
注:購入金額はAliexpress特売期間の価格だ。現時点では、もっと高いかもしれない。
12. 温度制御の評価 2020,02,18 開始
2台目のBear upgrade PRUSA(以降、
白PRUSAと記述)では、
ホットエンドのヒーターやサーミスタを自分で組み込んだ。
組込み作業の後にPIDの設定を済ませた。PRUSAは自動設定なので簡単だ。
素子の固定方法が不適切だと温度制御性能が低下する筈なので評価試験を行うべきだったが、忘れていた。
12-1 白PRUSAの温度制御性能測定
PIDによる温度制御の性能を評価するにはステップ応答を見るのが簡単だ。
OctoPrintには温度変化をグラフ表示する機能がある。これを利用すれば簡単にステップ応答が見られる。
実行したのが下のグラフだ。
緑の線は目標温度設定値で0℃から230℃へステップ状に上げている。
赤の線はホットエンドの温度で直線的な傾斜で上がっている。
概ね2分で目標温度へ到達し以降は安定している。目標温度への収斂も早い。
素晴らしい性能で自分が行った
組込み作業に問題が無かった事を確認できた。
12-2 黒PRUSAの温度制御性能測定
キットを買って組み立てたBear upgrade PRUSA(以降、
黒PRUSAと記述)のホットエンドは組立て済みだった。
PIDの自動設定は行ったがステップ応答を試してなかった。メーカーの組立てを信じていたからだ。
念の為に試したところ温度制御の性能に問題が在った。下のグラフは、その結果だ。
目標温度設定値を0℃から230℃へ上げた直後から概ね4秒後にホットエンドの温度が上がり始めている。
遅れが4秒も在るのは長すぎる。目標温度への収斂も遅い。白PRUSAに比べて性能が低い。
遅れはPID制御(フィードバック制御)の大敵だ。反応速度を低下させ制御誤差(残留偏差)を増やす。
どうやら中国のメーカーが行ったホットエンドの
組立て作業に問題が在るようだ。
12-3 黒PRUSAの温度制御性能改善
金属同士の接触で熱を伝えようとする場合には、その界面に伝熱材を充填するのが一般的だ。
黒PRUSAの場合には、その
伝熱材が不足なのか使われていないのではと疑った。
そこで伝熱材を追加で充填すれば性能は改善されると筈と考えた。
伝熱材を追加したいのは、ヒーターの周りとサーミスタの周りだ。
先ずヒーターをヒートブロックから外そうとしたが、固定しているネジが堅く締められていて緩まなかった。
六角のレンチ用穴が丸くなっても緩まなかったので、ヒーター周りへの伝熱材追加は後回しにした。
下のヒートブロックの写真で上面右端に見えるのが固定用ネジだ。
次にサーミスタへ取り組んだ。下の写真で上面左端に見えるイモネジがサーミスタ固定用だ。
これは緩められた。ところが穴からサーミスタが抜けない。
固定用のイモネジを強く締めすぎてサーミスタの保護管が歪んでしまったのだろう。
サーミスタがヒートブロックから外せないので、外さずに済む方法を工夫した。
固定用のイモネジを外し、そのネジ穴へ伝熱材を注入し、
その後ヒートブロックの温度を200℃まで上げてからイモネジを締め込んだ。
熱で軟らかくなった伝熱材がイモネジに押されてサーミスタとヒートブロックの隙間に浸透した筈だ。
一般的に伝熱材には
伝熱セメント等が使われる。しかし産業設備用で、ゆえに量が多く値段が張る。
そこでコンピュータのCPU冷却用として売られている
放熱グリスを使った。
伝熱セメントと放熱グリスは、呼称と使用目的が違うが、機能は同じだ。
放熱グリスをサーミスタの周囲へ充填した後で効果を調べるためにステップ応答を見た。
従前は4秒程度だった遅れが2秒程度に短縮された。やはり
伝熱材が不足していた。
僅かな量の放熱グリスで大きな効果が在った。しかし自分で組み込んだ白PRUSAには及ばない。
◎ヒーター周りへの伝熱材追加 2020,03,10 実施
ネジザウルスという工具を買って、以前に失敗したヒートブロックのネジを緩めるのに成功した。
そこでヒーターの周囲に伝熱材を注入しステップ応答を見たのが下のグラフだ。
加熱開始直後の遅れ時間が、従前のサーミスタの周りに伝熱材を注入したグラフよりも更に減っている。
かなり改善されたが、白PRUSAには及ばない。問題はサーミスタ保護管の中に在りそうだ。
白PRUSAの様にサーミスタの保護管を自分で組立てれば更に改善できる筈だが、効果の程度が判らない。
カートリッジ ヒーターをヒートブロックから抜いた際に下の写真を撮影した。
驚いた事に伝熱材を使った形跡が見られない。黒いのは印刷に失敗した際のフィラメントだ。
3Dプリンターを開発した人々は伝熱材の重要性を知らないようだ。
12-4 伝熱材注入の効果
黒PRUSAへ伝熱材を注入した効果をFirst Layer Calibrationで評価した。
使ったフィラメントは勿論PETGだ。
下は伝熱材を注入する前のFirst Layer Calibrationの写真だ。
サーミスタの周りに伝熱材を注入した後にFirst Layer Calibrationを行った結果が下の写真だ。
上の写真と比べれば伝熱材を注入した効果は一目瞭然だ。
比較の為に白PRUSAのFirst Layer Calibrationを行った。
サーミスタの周囲に伝熱材を注入した後の黒PRUSAよりも僅かに線の巾が安定しているように見える。
黒PRUSAを作った時点では、First Layer CalibrationはPLAしか使えなかった。
仕方なくPLAでFirst Layer Calibrationを行い、ノズルの高さを合せてからPETGで印刷していた。
2019年の秋に出たファームウエア3.8.1からPETGでもFirst Layer Calibrationが出来るようになった。
素晴らしい進歩だ。
12-5 PID改善の印刷物への影響
伝熱材を注入した黒PRUSAを使いPETGで幾つか印刷した。
結果は印刷物の表面が、従前よりも綺麗に揃っていた。
従前でも、まともに印刷できたが稀に小さなダマができた。それが全く無い。
下の写真で左から
Octprint用TVカメラ腕木、寸法精度確認用立方体、スプールスタンド用ハブだ。
Octprint用TVカメラ腕木は過去にPLAで作った物が罅割れたので代替だ。
またハブは床へ落として割ってしまったPLA製の代替だ。
PLAは繊維は強いのだが画層間の融着が弱い。
その点でPETGは画層間の融着が強く優れている。
上の写真で中央に在る立方体は一片が50mmだ。
そのFirst Layerを印刷したところで中断して取り出したのが下の写真だ。
ノズルの吐き出した糸が綺麗に並び布地の様に揃っている。
厚さは指で持っている部分が0.5mm、他は0.3mmだ。
13. 印刷精度の測定 2020,03,03 実施
黒PRUSAの印刷精度を把握する目的で前出の立方体を印刷した。一辺の長さは50mmで設計した。
立方体の寸法は、
X軸:49.8mm ( 誤差-0.4% )、
Y軸:49.7mm( 誤差-0.6% )、
Z軸:49.9mm ( 誤差-0.2% )だった。X軸とY軸の誤差は僅かだが改善の余地がある。
Z軸の誤差はスライサーが49.9mmと設定した値であり黒PRUSAの実質的な誤差はゼロだ。
立方体を使ってZ軸が直立しているのか調べた。残念ながらY軸とZ軸は直角でないのが判った。
下の写真で立方体に当てた直角定規の隙間から光が漏れている。
その巾は上部で1mmほど在った。つまりZ軸は少し前傾していた。
プリンターを平らなところへ置いて曲尺を当てたところZ軸の上端で5mm程前傾していた。
組立てた際に三角定規で確認した筈なのだが狂っていた。
原因は判らないが、Z軸のV溝棒を固定しているビスを締める際に狂ってしまったのだろう。
修正する為にZ軸のV溝棒を固定している20本のビスを緩めて傾きを修正し締め直した。
修正の結果を確認するために精度試験用ブロックを設計して印刷した。
立方体は印刷に時間が掛かるのでZ軸の直立を調べる目的に不要な部分を削ったブロックだ。
その結果、Z軸の傾斜は解消されていた。
14. PINDA故障 2020,02,26 実施
完成したばかりの白PRUSAが故障した。
症状は、Auto homeでZ軸がゼロ点まで下がらない。
Octprintで操作するとXYZ軸の総てが動き異常動作は見られない。
Wizardで試すとSelftestの段階ではXYZ軸とも正常に動きOKとなるが、
Calibration XYZの段階へ進んだ途端に下の写真のような故障を指摘された。
この指摘の具体的な意味が理解できなかった。
指摘されたXYZ軸を調べたが何も見つからなかった。
原因を究明すべくXYのプーリーやベルトが緩んでないか点検した。
Z軸の上部ストッパーも点検したが、緩んでなかった。
この問題を解明するために試行錯誤を繰り返し数日を費やしてしまった。
その後、おかしな事に気づいた。
PINDA(距離センサー)の頭頂部に在るパイロットランプが点灯していない。
このランプは鉄が近傍にあると消灯するが、無ければ点灯する。
下の写真ではベッドのバネ鋼板から離れているので点灯していなければならない。
消えているのでPINDAの故障が疑われる。
そこでPINDAの配線を外して別電源から給電して動作試験をした。
PINDAは電源を投入した際に一瞬だけ光るが、全く反応しなかった。
PINDAの故障だ。
このPINDAは近傍にバネ鋼板が無いのに在りとの誤信号を出していた。
よって制御コンピューターはZ軸が上限に在ってもZero点に在ると判断し下がらなかったのだ。
この異常を検出したCalibration XYZの表示内容が、もう少し具体的であれば
時間を浪費せずに済んだ筈だ。ファームウエアに改良の余地がある。
この白PRUSAでは2回しか印刷していない。
白のPLAとオレンジのPETGでgunomeを印刷した。
印刷は大成功だった。その際、PINDAは正常に機能した。
印刷中には、ホットエンドを冷却した温風に曝されてPINDA内部の温度が上がる。
運転停止を何度か繰り返し、温度が上がったり下がったりしたので
半田の芋付けが接触不良を起こしたと推定している。初期故障だ。
このPINDAはエクストルーダKitに含まれていたものだ。
このKitの部品は問題が多かった。
プラスチック部品の印刷が雑だったし、付属のサーミスタも使えなかった。
安物を買って散財してしまった。
代替の部品をbanngoodとAliexpressへ発注した。
banngoodには、PINDAは一種類しか無かったが、輸送の速さを期待した。
Aliexpressでは品質の良さそうな
Trianglelabを選んだ。
Aliexpressで売られているPINDAでは一番に値が張るが安物は懲り懲りだ。
14-1 BanggoodのPINDA到着 2023,03,09
実施
2月26日にBanggoodへPINDAを発注した。
商品がBanggoodから輸送を担うはOCSへ渡ったのが3月6日なので9日後だ。
OCSが通関を済ませ日本に着いたのが、3月8日、翌日に佐川急便が届けてくれた。
注文から手元へ届くまで12日間だったが輸送は、たったの3日間だ。速い!!。
早速届いたPINDAの機能を試した。
白PRUSAの制御基板上のコネクターへPINDAを差込み電源を供給しが、
PINDA上端のLEDが点灯しない。
眼を凝らしてみたら点灯していたが、薄い光で見えなかった。
検出の精度を試すために写真のようにDips micrometerとPINDAを向かい合わせて、
Dips micrometerのノブを回して隙間を変え、PINDAが検出する位置を測定した。
動作のチェックはLCDのSupportの中のSensor infoを利用した。
下の写真ではPINDAは
0で鉄を検出していない。故障した際には常時
1だった。
肝心の検出間隔は、
2mmピッタリで驚いた。凄い精度だ。
Banggoodから購入したPINDAは使えるが、
モニター用LEDが暗いのが難点だ。
そのような設計なのか、不良品なのか判らない。
来週にはTriangleLabへ発注したPINDAが届きそうだ。
両方を比べて良い方を組み込もうと考えている。残りは予備にする予定だ。
14-2 PINDA交換 2020,03,13 実施
TriangleLabへ発注したPINDAが、まだ上海あたりに在る。
待ちきれないのでBanggoodから購入したPINDAを組み込んだ。
高さ調整の後にFirst Layer Calibrationを行ったのが下の写真だ。
故障したPINDAを交換して白PURUSAが復活した。
印刷に支障は無いがパイロットLEDが暗い。上の写真は点灯している筈だが見えない。
それにしてもFirst Layer Calibrationで設定するAdjusting Z の値がー1.800だった。
何か変だ。PINDAの検出距離が2mmならばー0.800程度の筈だ。
14-3 TriangleLabのPINDA到着 2020,03,21 実施
TriangleLabへ発注したPINDAが到着した。注文してから16日が過ぎていた。
早速性能を試した。前回はガムテープで固定したのだが、ガッチリと押さえるのは難しかった。
そこでPINDAとDips micrometerを固定する治具を3Dプリンターで印刷して使った。
測定結果は1.5mmで定格の2mmよりも0.5mmも狂っていた。
若しや
Dips micrometerの先端の面積が小さく誤差を増やしているのではと疑った。
そこでDips micrometerの先端にカッターナイフの刃を重ねて測定したところ
1.99mmだった。
従前の測定方法は不適切だった。
TriangleLabのPINDAは正確で頭部のモニター用LEDも適度に明るく良い感じだ。
TriangleLabのPINDAは何の問題も無い良い製品だった。
PINDAを白PRUSAへ取り付け高さを1mmに調整した後にFirst Layer Calibrationを行った。
その結果、
Adjusting Zはー0.600だった。
表面にフィルムを貼ったバネ鋼板に印刷したので納得できる値だ。
測定方法に問題が在ったので、先に試したBanggoodのPINDAを再度測定した。
カッターナイフの刃を重ねて測定したら3.5mmだった。
Adjusting Z の値がー1.800だった事と符合する。
Banggoodから購入したPINDAは誤差が多く、モニター用LEDが暗い。
15. タイミング プーリー交換 2020,03,08 実施
黒PRUSAではX軸とY軸が動く際にブーンと唸る様な音が聞こえるが、大きな音ではないので問題ない。
しかしX軸とY軸が同時に動く斜め移動では、共鳴するらしくブイーンと大きな騒音が出る。これが気になる。
騒音の発生源が何処か判らなかったが、タイミング
ベルトの歯がプーリーの円筒面に当たる際の音だろうと推定した。
その騒音を軽減する為にベルトの歯が当たる場所が凹んでいる歯付プーリーを試した。
プーリーを外したところタイミングベルトとの接触面に黒い痕跡が在った。
高い圧力が掛かっているようだ。強く張り過ぎなのかもしれない。
下の写真で左側が
新しい歯付プーリー、右側が外したプーリーだ。
従前のプーリーは軸穴の直径が3mmだが、新しいプーリーは5mmだ。
3mmの歯付を探したが、amazonにもAlliexpressでも見つからなかった。
仕方なく5mmのプーリーをamazonから買い、軸穴を細くするパイプをPETGで印刷して嵌め込んだ。
交換後に試運転をしたところ、騒音は従前のブーンからシャーへと変わっていた。
騒音源の推定は的中し、黒PRUSAは従前よりも静かなプリンターになった。
歯付プーリーは騒音低減に大きな効果が在った。
シャーという感じの騒音はベアリングから出ている。
白PRUSAも黒と全く同じ構造だが、白はベルトからの騒音が少ない。
白に使ったタイミングベルトは黒よりも少し柔らかい感じなので、
それが騒音発生を抑えているのかもしれない。
プーリーを変えた事により印刷物の表面が、
以前よりも僅かに滑らかになったような気がする。
GitHubに
歯付プーリー用テンショナーが在る。これを印刷して試したが、
自分が買ったプーリーは鍔の部分の直径が18mmで、大きくて入らなかった。
Thingiverseにも
同じ目的のテンショナーが在るが、同じ理由で使えなかった。
16. 電源箱でトラブル発生 2020,03,22 実施
白PRUSAで印刷を始めて30分も過ぎた頃にトラブルが発生した。印刷の途中で止まったのだ。
暫くすると印刷を継続するリカバリー動作に入るが、また停まる。
数回試したが、この現象を再現するので電源箱の過熱保護機能が働いたと推定した。
そこでベッドの温度を60℃から40℃へ下げ、消費電力を減らして印刷したところ最後まで印刷できた。
この結果から過熱保護機能が働いた可能性が濃厚になった。
このところ気温が上がって過熱しやすくなったのだろう。室温は20℃位だった。
この電源箱はヤフオクで廉く落札した。
純正品だそうだが外観からは、純正品かコピー商品か見分けられない。
しかしWebでオリジナルの写真を見るとPRUSA RESEARCH社製の旧型電源に酷似している。
過熱保護機能が働いた原因を解明するために電源箱を分解してみた。
商用電源を高周波へ変えるPower FETが、放熱の為にアルミケースへネジ止めされている。
Power FETはシリコンゴムの袋に入っていた。
Power FETが絶縁破壊を起こした際に高電圧がケースへ漏れ出るのを防ぐ目的だろう。
その
シリコンゴムの外側とアルミケースの間に放熱グリースが塗られていなかった。塗り忘れか?。
シリコンゴムは軟らかいので放熱グリースは不要と考えたのかもしれない。
しかしシリコンゴムの袋を切って中を覗くと、中のPower FETには放熱グリースが使われていた。
アルミケースとシリコンゴムの外側の間にも必要な筈と考えアルミケースへ放熱グリースを塗って元の様に組立てた。
その結果
放熱グリースが機能したらしく状況は改善された。しかし問題が完全に解消されたのか判らない。
下の写真で最上部に灰色の四角い部品が二個並んでいるのがシリコンゴムの袋に覆われたPower FET。
斜めになっている黒い棒が温度センサー付きのPower FET押さえ棒だ。
写真では外されているが、普段は長いビスでPower FETをアルミケースへ締め付けている。
アルミケースに付着している灰色のペーストは自分が塗った放熱グリースだ。
組立てた後に印刷を行ったが過熱保護機能は働かなかった。
印刷したのは円筒形スピーカー用のデフューザーだ。
大きさは縦120mm、横120mm、高さが100mmで円錐に羽が生えた形だ。
印刷には黒色PLAを使い5時間を要した。
ノズル温度210℃、ベッド温度60℃、周囲温度は17℃だった。
もしも問題が再発した場合にはPower FETを発熱の少ない物に交換しようと考えている。
使われていたのはFAIRCHILDが開発したFQA11N90の互換品だった。
定格は900V 11.4Aだが、
ON抵抗が0.96Ωも在る。大き過ぎる。
秋月電子通商のカタログを見るとON抵抗が格段に低い物が廉く売られている。
ON抵抗が0.35Ω程度のPower FETに替えれば発熱は大幅に減らせる筈だ。
16-1 電源箱の能力推定 2020,03,25 実施
先の試験印刷でPLAフィラメントでは問題無いのが判った。
しかし自分はPLAフィラメントは殆ど使わない。
以前は使ったのだが、PRUSAを買ってからはPETGフィラメントばかり使っている。
2年前に買って使わずに眠っていたPLAフィラメンを利用して試験印刷を行ったのだ。
肝心のPETGフィラメントでも印刷できるのか確認しなければならない。
しかしPETGフィラメントを浪費したくなかったので"
エアー印刷”を試みた。
フィラメント検出スイッチに短いフィラメントを差込み誤魔化して運転した。
運転条件は
ノズル温度240℃、
ベッド温度90℃で運転した。
室温は16.5℃だった。
その結果、
運転開始から約30分後に停止し液晶表示も消えて真っ暗になった。
調べたところ電源箱のAC入力部に在る
5Aのガラス管フューズが溶断していた。
自分が実際にPETGフィラメントを使って印刷する際には、
ノズル温度235℃、
ベッド温度60℃に設定している。ベッド温度90℃で30分も耐えたので、
それよりも30℃も低いベッド温度ならば夏場に室温が上がっても耐えられる筈だ。
室温が上がるとベッド加熱電力が減るので
ベッド温度60℃ならば充分に余裕が在ると判断した。
ところがフューズを新品と交換し電源スイッチをONにしたが、電源が入らない。
スイッチング電源が故障してしまった。故障部位を特定するためにスイッチング電源を開けて調べた。
その結果
スイッチング電源の基板上にもフューズが在り、それが切れていた。
下の写真で下部中央に在る黒い直方体がフューズだった。
見た事の無い形だが、基板に
FS1 T5A/250Vと印刷されていたのでフューズと判った。
テスターで動通を測ったところ無限抵抗だった。
更にパワーFETが2個ともD-S間が貫通破壊を起こしていた。
パワーFETの故障でガラス管フューズと基板上のフューズに過電流が流れた。
このスイッチング電源は保護協調が上手く機能していないようだ。
故障したパワーFETの代替品を探している。入手出来次第交換する予定だ。
16-2 代替電源到着 2020,05,10 実施
過日に壊れた白PRUSAの電源を修理して使おうと考えていたが、
調べたところパワーFETだけでなくファーストリカバリーダイオードも壊れていた。
そのダイオードには放熱器が付いていたが、放熱グリースが塗られてなかった。
これではヒューズが切れるような過負荷で何度も運転すると熱でダイオードが劣化して壊れる。
代替パワーFETは良さそうなのが見つかったが代替ファーストリカバリーダイオードが見つからない。
見つかり次第修理しようと考えているが、時間が掛かりそうなので代替電源を発注した。
その電源はAliexpressに出店している
TriangleLabの商品だ。
選んだ理由は、黒PRUSAに使っている電源にはトラブルが無いので同じ物にした。
発注してから30日で手元へ届いた。輸送の種類はe-packetだった。
COVID-19で流通が混乱している折にしては速かった。
驚いた事に製造者の名称と住所が表記されていた。中国製にしては珍しい。
念のために届いた電源を開けて放熱グリスの有無を調べた。下の写真は開けた様子。
パワーFETと2次側整流器には放熱グリースが塗られていたが、一時側整流器には放熱グリースが無かった。
そこだけ放熱グリースを追加して組み立て、白PURUSAへ組み込んだ。
これで白PURUSAは以前のように印刷できるようになった。
この電源箱はオリジナルと違うところが在る。
先ず電源電圧は110Vと220Vをスライドスイッチで切り替える方式だ。
オリジナルのような広い電源電圧にスイッチ無しで対応する物に比べて回路が単純になる筈だ。
信頼性も向上するのではと考えている。
それに電源のスイッチが照光式だ。スイッチONですぐに電源が入ったのが判る。
オリジナルでは前面のLCDが光るまで判らない。
1秒程度の遅れなのだが、使ってみると照光式のほうがオリジナルよりも良い感じだ。
17. 印刷台の断熱とNylock-Spring leveling
17-1-1 印刷台の断熱 2020,03 31 実施
印刷台の裏面からの放熱を減らし消費電力を削減する目的でコルクの板を貼った。
コルクの板はダイソーで買った。ナチュラル コルククラフトという商品名で大きさは220*300*5.9tだった。
大きさを合せて切り、両面テープで印刷台の裏面に貼った。切欠きは固定用ビスを通す部分だ。
印刷台の断熱で消費電力を2割程度は減らせるのでは?と期待している。
17-1-2 コルク断熱の節電効果把握 2020,05 実施
Aliexpressで
電力計が安価に売られていた。
これを買って印刷台の断熱による節電量を測った。
節電効果の測定は、コルク断熱を施した黒PRUSAとコルクの無い白PURUSAを比較した。
その結果、コルク断熱での
節電効果は1割程度だった。
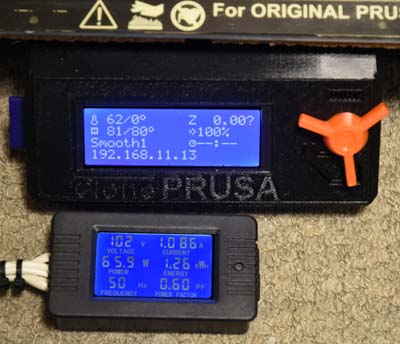
上の写真では、室温26℃でベッドの設定温度が80℃の際に65.5Wを消費している。
コルクが無ければ72W程度に増える筈だ。
実際に印刷している状態ではベッドが前後に動くので
放熱量が増えるはずだが、変動が大きく測定が難しくて失敗した。
しかし大きな影響は無いようだった。
17-2-1 白PRUSA用 Nylock-Spring Leveling 2020,04,01 実施
PRUSA i3MK3にはバネ鋼板を磁力で固定する印刷台が使われ、
PINDAと呼ばれるセンサーでノズルの高さを測り、自動的に制御するので印刷台の高さを調節する機構が無い。
ところが、印刷台がバネ鋼板なので僅かに撓んだり反ったりしていて完全な平面ではない。
Nylock Levelingは、Nylockと呼ばれる緩み止めナットを用いて印刷台の撓みや反りを修正する方法だ。
従来のスペーサーを外してビスにNylockを取り付け高さ調節機能を付与する。
Youtubeに解説した動画が在る。
https://www.youtube.com/watch?v=hDv73AdiBqM
しかし、この方法では固定用ビスにガタツキが在り安定性に難があると考えていた。
そこでコイルスプリングを併用する
Nylock-Spring Levelingを考案した。
下の写真は固定用ビスにコイルスプリングを被せた状態だ。
下の写真は
Nylock-Spring Levelingの部分を拡大した。
コイルスプリングは外径8mm、長さ10mm、太さ0.8mmだ。
Nylock-Spring Levelingを組み込んだ印刷台でOctPrintのPrusaMeshMapを使って高さを調節した。
その結果が下の図だ。一見すると大きな凸凹が在るように見えるが最大高低差は僅か0.036mmだ。
従前は最大高低差が0.25mmも在ったので大幅に縮小された。素晴らしい成果だ。
上の図は印刷台の温度を60℃に暖めてから約1時間後に行った。
加温を切り室温の16℃まで冷めてから測定したら最大高低差は0.08mmになっていた。
印刷台は温度変化により膨張や収縮して寸法が変わる。
どの位の温度でNylock-Spring Levelingを行うのが最良か思案している。
実際の運用上は最大高低差が0.1mm程度ならば問題ないと考えている。
Nylock-Spring Leveling無しでは最大高低差を0.1mm程度に追い込む術は無い。
ゆえに
Nylock-Spring Levelingは有益な技術だ。
Nylock-Spring Levelingの印刷物への影響は、
高さ方向の精度が0.1mm程度向上する程度だろうと考えていた。
ところがFirst Layer Cal.を実施したところ印刷の品質が大幅に良くなっていた。
従前はPLAは簡単だがPETGでのジグザグ印刷は難しく、
途切れず、剥がれず、鈍角にならない事をLive Zの設定基準にしていた。
つまり印刷を失敗しないLive Zを選んでいた。
ところがNylock-Spring Levelingを組み込んだ後は、設定基準を満たすLive Zが大幅に広くなった。
従前はLive Zの最適値がー0.410mmだった。( バネ鋼板はSmooth1を使用 )
それで途切れずにジグザグ印刷は出来るのだが印刷した糸の断面が潰れ気味だった。
Live Zの値を変えて試行錯誤を繰り返した結果、Live Zの最適値はー0.345mmに落ち着いた。
この値だと糸の断面が潰れずに楕円形になる。
Nylock-Spring Levelingを組み込んだ後のLive Zを設定する基準は
糸の断面が楕円形になる事だ。
Nylock-Spring LevelingによってPLAでは当たり前のことがPETGにも適用できるようになった。
それにしてもPINDAによってノズルとバネ鋼板の間隔は自動制御されている筈だ。
何故にバネ鋼板の歪みや撓みを
Nylock-Spring Levelingによって補正すると印刷の品質が向上するのか謎だ。
しかも
バネ鋼板への印刷物の定着も良くなる。
PINDAに依るノズル高さの自動制御が荒いのだろうか?。
( メモ: Smooth1 Live
Z ー0.345mm、 Texture1 Live Z -0.550mm )
17-2-2 白PRUSA用 Nylock-Spring Leveling 2020,05 実施
白PRUSAにもNylock-Spring Levelingを組み込んだ。
黒PRUSAには設定にOctPrintのPrusaMeshMapを使った。
白PRUSAではOctPrintの
Prusa
Leveling Guideを使った。
これによって簡単にベッドの高低差を0.033mmまで追い込む事ができた。
実行結果は以下のようになった。
このプラグインは素晴らしいのだが、変な動きをする事がある。
先ずBegin Adjustingを押して開始するとエクストルーダーが動いてベッドの9箇所を測る。
暫くすると画面に測った距離が反映される。
その後にContinueを押した場合にもエクストルーダーが動いてベッドの9箇所を測るが画面に反映されない。
もう一度Continueを押すと前の測定結果が画面に反映される。
自分の設定に間違いがあるのかプラグインにバグがあるのか判らない。
何とか騙し騙し使って乗り切った。
18. ファームウエアの更新 2020,04,05 実施
PRUSAのファームウエアは、PRUSA RESARCH社のホームページに在るFIRMWARE 3.8.1が最新だと考えていた。
ところがGitHubには更に新しい
FIRMWARE
3.9.0 RC1が在るのを見つけた。
試験版だが早速インストールして使ってみた。
細かな改良が沢山施されているが、自分が良いと感じたのは下記の2点だ。
18-1 温度低警報の設定温度変更 ( 15℃ から 10℃ )
従前は室温が
15℃を下回るとLCDに
Minitemp error と表示され印刷できなくなる。
3月末にも少し寒い日が在り印刷できなかった。仕方なく熱湯を注いだコップを印刷台に載せて誤魔化した。
日頃から
15℃は高過ぎると感じていたのだが、
新しいファームウエアでは10℃に下げられた。
これなら我が家では、Minitemp error は発生しないだろう。
18-2 PINDAを使う際に印刷台の加温を切る
印刷台の加温にはPWM制御が使われている。PWMはパルス幅変調の意味だ。
PWM制御は電力をON-OFFして調節するので高周波の電磁界が発生しPINDAに影響が出る。
それが好ましくないのでPINDAを使って印刷台の高さを測るときだけPWM制御をOFFにする。
実際にOctPrintのPrusaMeshMapを使った場合に、
高低差を0.05mm以下に絞り込んだ際の再現性が良くなったと感じた。
19. 防塵カバーの製作 2020,04,06 実施
Bear upgrade PRUSAの骨格はアルミV溝押出し棒を組み合わせて作られている。
その為に強度が高く体重を掛けても歪んだり撓んだりしない。ところが、そのV溝に塵が溜まる。
特に前方両脇の部分にはフィラメントのカス等が溜まり易く見苦しい。
そこで、その両脇の部分を覆うカバーをPETGで印刷しアルミV溝押出し棒へ嵌め込んだ。
その上部空間を利用しないのは勿体無いので強力な磁石を嵌め込み工具等を保持できるようにした。
工夫したのはカバーをアルミV溝押出し棒へ固定する方法だ。
V溝へ嚙み込む爪を七箇所に設けた。緩いかと危惧したが、ガッチリ固定された。
使用したPETGは強いので爪が折れないが、PLAでは硬く脆いので折れると思う。
中央部に直径23mmの丸穴を設け、ネオジム磁石を嵌め込み周囲の4箇所に接着剤を塗った。
実際に使ってみると磁石を使った工具保持機構が案外に便利だった。
頻繁に使うピンセットや六角レンチなどを吸付けておくと工具が迷子にならない。
使用したネオジム磁石は直径23mm、厚さ2.5mmで百均のセリアで買った。
同じと思われる磁石がダイソーにも並んでいた。
この印刷はNylock-Spring Levelingを組み込みファームウエアをFIRMWARE 3.9.0 RC1へ
更新して以降最初の印刷だった。気のせいか従前よりも更に調子が良いように感じた。
この印刷用データーを
Thingiverseへ掲示した。
20. Longsell PETG フィラメントの試用 2020,04,25 実施
今まで使っていたeSUN製の白色PETGが残り僅かになった。スプールの軸に数巻きなので1m程度か。
補充の為新たにPETGフィラメントを購入した。こんどのは
Longsellの緑色だ。
選定理由は色と値段だ。PETGは色の種類が少ない。その中でLongsellは10色も用意している。
その上に値段が\2,699-/Kgと安価だった。
届いたフィラメントを見ると色は不透明の緑で光沢も適度で良い感じだった。
念のためにSmooth1で初層校正を行いLive Zの最適値を求めた。
この前まで使っていた
TONXYのTran-Orangeでは ー0.345mmだった。
しかし、この
Longsellの緑では-0.385で0.04mmだけ下がっていた。
フィラメントによって最適なLive Zが僅かに違うようだ。
この後に従前のPETGの印刷温度で試験印刷を行ったところ初層が毛羽立ってしまった。ノズルの温度が低いようだ。
今までにメーカーの違う3種類のPETGフィラメントを使ったが、ノズルが235℃、ベットは60℃で上手く印刷できた。
初層校正では印刷温度が230℃/80℃に固定されている。ベッドが80℃だったので毛羽立たなかったようだ。
スプールに張付けてあるシールを見ると印刷温度が230℃-260℃になっている。
今まで使ったフィラメントは230℃-250℃だったので要求温度が高い。
そこでノズル温度を245℃に設定し、ベッドは初層だけ80℃にして以降は70℃にした。
その印刷条件で
MakerBot Gnomeを印刷した。中央の緑色が今回の印刷だ。
印刷の出来栄えは従前と全く同じだが、今度のフィラメントは不透明なので写真写りが良い。
Gnomeは黒PRUSAと白PRUSAを試験する度に印刷したので6体もある。
Gnomeが上手く印刷できたので少し大きいものを印刷してみた。
Josef prusa氏がCOVID-19対策で設計した作品だ。設計が巧みなので何の問題も無く印刷できた。
しかし3個の部品を印刷するのに6時間も掛かってしまった。
以上の試用で
LongsellのPETGは印刷温度が高いが、普通に使えるフィラメントだと判った。
価格が廉いのも魅力だが、それ以上に色の選択肢が増えたのが嬉しい。
21. 長腕操作ノブの製作
2020,04,27 実施
Octprintを組み込んでからLCD表示部についている操作ノブを使う機会は半減した。
しかしOctprintは電源投入から動作するまでに5分程度かかる。
その待っている時間が無駄なのでフィラメントの交換やノズルの掃除を行う。
温度を上げる為に
SettingーTemp.ーNozzleにして温度を合せるのだが
PETGの場合には230℃程なのでクルクルと何度もノブを回さなければならない。
PRUSA i3 MKSの標準ノブは腕の部分が8mm程度と短く指が外れそうだ。
そこで腕の部分を長くすれば扱いやすくなると考えた。
また従前は腕が一本だったが、Prusa MINIのように3本のほうが良さそうに思えた。
そこで下の写真のように15mmの腕を3本備えたノブを設計製作した。
実際に使ってみたところ明らかに扱いやすくなった。
人差し指の先でグルグルと勢い良く回せる。回す速度は従前の何倍にもなったと思う。
腕が長くなった事で不都合な事が起こるのではと懸念したが何も無かった。大成功だ。
設計はGithubで開示されているPrusa i3 MK2のLCD-knob.scadをダウンロードして改造した。
無料のopen-scadでLCD-knob.scadを読み込みExportでLCD-knob.csegに変えた。
それを同様に無料のfreecadで読み込み腕の部分を改造した。
この印刷用データーを
Thingiverseへ掲示した。
22. 固体ポリマーベアリングの試用 2020,05,11 実施
ベアリングといえば鋼の球が回るボールベアリングが一般的だが、
最近は自己潤滑性の在るプラスチックで成型したポリマーベアリングが在る。
鋼球のような動く部分が全く無く滑りを利用している。
好奇心からAliexpressに出店している
FYSETC 1th Storeから購入し試してみた。
左がポリマーベアリング、右が従前のLM8UU だ。大きさは全く同じだった。
耐磨耗性が判らなかったのでXYZ軸の中で最も動きの少ないZ軸へ取り付けた。
Z軸は片側に2個、両側では4個のLM8UUベアリングを使っている。
これらを総てポリマーベアリングへ交換した。
下の写真は、白PRUSAのZ軸モーター側へポリマーベアリングを取り付けた様子だ。
Z軸をポリマーベアリングへ交換後に
MakerBot Gnomeを印刷し評価した。
使用したフィラメントはLongsellのPETGだ。
左がポリマーベアリングを組み込んだ白PRUSAでの印刷、右はボールベアリングの黒PRUSAでの印刷だ。
印刷結果は殆ど同じだが、細部が僅かにシャープになったように見える。
右の髭の部分に横線が見えるが、ポリマーベアリングを組み込んだ白PRUSAで印刷した左には線が無い。
印刷物への影響は僅かだったが、
騒音低減には大きな効果が在った。
PRUSA i3 MKsはステッピングモーターのピロピロピーピーの様な音が出ない。
3Dプリンターとしては低騒音だが、歯付ベルトの音や発生源が判らない騒音が少し出る。
それが大幅に減った。運転中に聞こえるのはエクストルーダを冷やすファンの音だけだ。
費用と騒音低減の効果を考えると1,000円( 4個 )は廉い買い物だったと思う。
Trianglelab社のポリマーベアリングを説明した文に、模造品に注意とある。
どうやら自分が買った物は模造品だったようだ。型式の刻印が無い。
値段も少し高いだけなのでオリジナルを買えば良かったのかもしれない。
黒PRUSAの分はTrianglelab社から買おう。
X軸やY軸へポリマーベアリングを組み込めば一層の低騒音化と印刷精度の向上が期待できる。
しかし耐久性に不安が在る。Web上で情報を探しているが見つからない。
23. フィラメントの詰り除去 2020,06,05 実施
誤操作をしてエクストルーダー内にフィラメントを詰めてしまった。
手でフィラメントを掴み押し込んでも、ノズルの下から細い針金を差し込んでもダメだった。
頑固な詰りだったので仕方なくエクストルーダーを分解し除去に成功した。
運悪く同様のトラブルに遭われた方の参考になれば嬉しい。
下の写真の様に前面から分解した。手順は以下の様だ。
①ファンノズルを外す。 M3ビス1 本
②前面ファンを外す。 M3ビス2 本
③側面ファンを外す。 M3ビス4 本
④PETG製抑え板を外す。 M3ビス2 本
以上の操作で下の写真の様に導入管とホットエンドが露出する。
導入管を手で手前に引くとエクストルーダから外れた。
更に導入管を手で回してネジを緩めホットエンドから外した。
外した導入管へ
直径1.8mmのドリルを差し込んだところ、
ホットエンド側から1cm程度入ったところで詰り物に当たった。
指先でドリルを回すとフィラメントの削りカスが少し出てきて詰り物が外れた感じがした。
開通を確認する為に穴へフィラメントを差し込んだら、詰り物が出てきた。
詰り物が撤去できたので元の様に組立てて作業は完了した。
初めての詰り物除去作業だったが、事前に考えていたよりも簡単だった。
エクストルーダーの設計が優れており詰まった場合の作業性も考えられている。
Bera Upgrade PRUSAには多くの人々の経験と知恵が凝縮されている。
詰まった原因は誤操作だ。
白PRUSAへのNylock-Spring Leveling組み込み作業が終わったので最終的な確認の為にWizardを行った。
Farmware 3.9.0RCでは3.8には無かったフィラメントセンサーの試験が加えられている。
この試験に短い白色のPLAフィラメントを使ったのだが、誤ってエクストルーダーへ吸い込ませてしまった。
短いので引戻せずPETGのフィラメントを入れて押し出そうとした。
大部分はノズルから出たのだが最後の部分が詰まってしまった。
PLAをPETGで押し出すのは問題があるのかもしれない。
23-1 ノズル衝突事故発生 2020,06,07
白PRUSAの寸法精度と直角を確認するために一辺が5cmの立方体を印刷した。
印刷が八割方済んだ所で衝突検出機能が働いて止まってしまった。
原因を探ったところ下の写真の様に印刷物の上に垂れ落ちたフィラメントが固まり、これにノズルが衝突した。
格子は内部充填で20%だ。
ホットエンドの何処から漏れ出たのか探るためにエクストルーダを分解して覗き込んだのが下の写真だ。
明らかに導入管とヒートブロックの間から漏れて蠟涙のようになっている。
ヒートブロックにシリコンカバーを被せてあるが、その中もグチャグチャだった。
原因は組み立てミスだ。
先のフィラメントの詰りを取り除く作業で、分解し組み立て直した際の締め付けが緩かったのだろう。
清掃の後に締め直して再度5cmの立方体を印刷したところ下の写真の様に印刷できた。
使用したフィラメントはLongsellのPETGだ。
印刷物の精度は、X軸方向:50.08mm 誤差:0.16%
Y軸方向:49.88mm 誤差:-0.24%
Z軸方向:49.90mm 誤差:-0.2%
各角の直角と垂直も調べたが、明らかな誤差は見られなかった。
この印刷試験で白PRUSAの機能は確認できた。
TVカメラを取り付ければ完成なのだが中国からの輸送が乱れており届かない。
困ったことだが仕方が無い。
24. RepRrapper PETGフィラメントの試用 2020,06,06 実施
新たに
RepRapper
PETGフィラメント 灰色 を買ったので試した。
先に買ったLongsell PETGは無地のダンボール箱で説明書等は無かった。
ところがamazonから届いたRepRapper PETGフィラメントは
綺麗な箱に入っていて製造した会社名が印刷されていた。
箱を開けるとフィラメント以外にいろいろと付属品が入っていて少々驚いた。
下の写真の右上のスプールは中央の穴がとても大きく直径が75mmも在った。
SUNLUのスプールが73mmなので、それよりも大きい。自分的には過去最大だ。
右下の黒いのは、粘着材付きのプラットフォームシート。
不透明で表面がザラザラしたプラスチック製の様だ。使っていないので評価できない。
左下はノズルが詰まった際に使う0.4mmのノズル洗浄針。
左中は印刷トラブルへ対応する窓口の連絡先を日本語で記したカードでQRコードも在る。
そのフィラメントを昨日にエクストルーダの詰りを取り除いたばかりの白PRUSAへ取り付けた。
いつも印刷の試験に使っているGNOMEを印刷してみた。
当初は適切な印刷条件が判らず試行錯誤したが、
結局ノズル温度を235℃に設定し、ベッドは65℃で普通に印刷できた。
下の写真で左がRepRaperのPETGで右がLongsellのPETGだ。
照明にLEDライトを使ったので色が変だ。本来は上の写真のスプールハブと同じ色だ。
一見すると同じような出来だが、上下に走る光の線が違う。
この線は天井に在る室内灯の光を反射した様だ。
左は線の幅が狭く、右は広い。右の表面には微細な凹凸がある。
左の表面は滑らかで凹凸が無いので光の反射を乱さないようだ。
この違いが何に起因するのか判らない。
25. AstroPrintの試用 2020,07,13 実施
AstroPrintは3Dプリンターを、インターネットを通じて遠隔操作できるソフトだ。
最小規模で機能限定だと無料で使える。早速ダウンロードして試してみた。
25-1 AstroPrintに必要なハード
3Dプリンターとインターネットを繋ぐ為にAstroboxと呼ばれる小箱が必要だ。
Astroboxと
Astrobox touchの2種が有償で用意されている。
しかし
OctprintのユーザーはAstrobox無しにAstroPrintへ接続できる。
Octrint用のAstroPrin Pluginが用意されていて、
これをOctprintへ組み込めばハードの追加無しでAstroprintを使える。
自分の2台のPRUSAにはOctprintが組み込んであるので障害は無い。
25-2 ユーザー登録と初期設定
youtubeに設定などの解説が在ったので、これに従ってユーザー登録を済ませた。
済ませると下図の様な作業のメニューが表示される。
25-3 プリンターの機種登録
メニューの上から3段目の左端にある
Printer Profileのアイコンををクリックして、
+New Printer Profileiのアイコンをクリックしてi3 MK3Sに設定した。
25-4 フィラメントの種類登録
上から3段目の左から2番目にある
Material Profilesをクリックして、PETGを登録した。
自分がPETGを使う場合には、最初の画層だけ温度を高く設定して2層目以降は5℃程度下げている。
この設定が判らなかった。用意されてないのかもしれない。この設定が無いとPETGは使い辛い。
25-5 スライサーの設定
上から3段目の左から3番目にある
My Slicer Settingをクリックして、
+New Slicer Profileiのアイコンをクリック。
既に登録したプリンターとフィラメントに合ったProfileiが表示されたので
Add Slicer settingをクリック。
25-6 試験印刷
メニューの左上に在るDesign Libralyをクリックした。するとDesign Libralyが開いた。
クラウドのサーバーにサンプルのAstro Key.stlが入っていた。これを印刷した。
上の画面で、ファイルサイズの後ろにマウスのポインターを近づけるとPrintのボタンが現れた。
トリッキーなユーザーインターフェースで要注意だ。
上図のPrintボタンを押したら下図のプリンター選択画面が現れた。
自分は2台のPRUSAを持っているが、1台しかAstroprintのPluginを組み込んでない。
プリンターの登録はPRUSA MK3Sと登録しているのだが、プリンター機種不明でoctopiとなっていた。
Printボタンをクリックすると3Dプリンターの印刷が始まった。
印刷開始と共に画面が下図のように切り替わった。
Printボタンの位置にMonitorボタンに変わった。
上図の
Monitorボタンをクリックすると画面が下図の様に切り替わった。
これは3Dプリンターの印刷状態を遠隔監視する画面だ。
25-7 結果と感想
下の写真の様にAstrokeyが印刷できた。上はAstroprintのスライサーを使った物で、
下はPrusa slicerを作ったGコードファイルをDesign LibraryへUploadしてから印刷した物だ。
明らかにPrusa slicerのほうが綺麗な印刷だ。
AstroprintのスライサーはPrusa i3 MK3Sへの最適化が充分ではないようだ。
自分がAstroprintに期待しているのは遠隔操作の機能だ。
運転や停止が遠隔で出来る機能は魅力的だ。
ところがMonitorの機能が今ひとつだ。
TVカメラで撮影した画像が見られるのだが、動画ではない。
画層が切り替わる際に画を更新するか、時計による更新で最短は1秒周期だ。
1秒周期の駒落としで3Dプリンターの稼動状態を把握するのは難しい。
この点が改良されるよう期待している。
Astroprintはスマホで3Dプリンターを操作することを主眼にしているようだ。
自分にはそのような必要性は無いのでスライサーや他の管理機能は必要無い。
自分のニーズとズレているように感じているが、社会にはそのようなニーズがあるのだろうか?。
26. OctoPrint Anywhereの試用 2020,08,01実施
過日、3Dプリンターを遠隔操作するAstroPrintを試したが、似た機能の
Octoprint Anywhereを知り早速試した。
Octoprint AnywhereはOctprintのプラグインだ。
Octoprint Anywhereを組み込んでも基本的な3Dプリンターの操作はOctprintで行う。
Gコードの読み込みや印刷開始の指示はOctoprint Anywhereでは出来ない。
Octoprint Anywhereはインターネットに接続されたブラウザーから3Dプリンターの動きを動画で見られる。
もちろんOctprintにTVカメラを取り付けなければ見えない。主なOctoprint Anywhereの機能は動画だ。
その他に遠隔停止の機能とXYZ軸を動かす機能が在る。しかし遠隔始動はできない。
3Dプリンターで大きな物を印刷すると長い時間が掛かる。
その間、不測の事態に備えて3Dプリンターの近傍で待機しているのは甚だ不便だ。
このOctoprint Anywhereを使えば3Dプリンターを始動した後に外出し遠隔でチェックできる。
万一3Dプリンターが異常な動作をしてスパゲッティーの様な印刷物が出来たら遠隔停止できる。
異常動作の被害を最小限に止められる。
Octoprint Anywhereは3Dプリンターの束縛から解放される素晴らしいソフトだ。
下の写真は自分のPRUSAでスピーカーの部品を印刷している様子だ。
それをOctoprint Anywhereで遠隔監視している画だ。
画がAstroprintのような駒落としではなく動画なので判り易い。
Octoprint Anywhereの解説記事をよく読んだら、改良された
Spaghetti
Detectiveという
プラグインがあるので切り替えろとの指示が在った。近々試す予定だ。
27. 純正ポリマーベアリング到着 2020,09,01実施
AliexpressのTriangleLabへ発注していた純正ポリマーベアリング4個が届いた。
早速従前の無印と寸法精度を比べてみたが、自分が持っているノギスでは差異が判らなかった。
外観上の違いは色が薄いのと型式の刻印が在る事だ。
しかしTriangleLabの説明によれば刻印の在るコピー商品が在るらしい。
そこで下の写真のように滑り棒に取り付けて感触でガタツキの有無を確認した。
比較した結果、無印は小さなガタツキが在った。次にガタツキが小さかったのが左端。
中央は全くガタツキが感じられなかった。
ここで解った結論は、無印よりも純正のほうがガタツキが小さい。
また純正にも僅かなバラツキがある。性能や耐久性の違いは判らない。
純正ポリマーベアリングの価格は1個あたり370円、無印は200円だった。
届いた純正ポリマーベアリングは黒PRUSAのZ軸へ取り付けた。まだ動かしてない。
28. eSUN PETGフィラメントの購入 2020,09,08 実施
このところスピーカーの工作でPETGフィラメントを沢山消費している。
足りなくなったので新たに
eSUN製のPETGフィラメントを購入した。色はグレーだ。
選んだ理由は価格が\2,580-と廉かったからだ。
自分が使っているBera Upgrade PRUSAは何処のフィラメントでも選好みしないようだ。
amazonから届いた商品を見ると箱が昔よりも洗練されていた。
スプールは無色透明だ。これは横から見ると残量が判り使い易く質感も良い。
しかしポリ袋がジップ付ではないのが、ちょっと残念だ。
フィラメントの端をスプールへ取り付けるのに強力なガラス繊維入りテープが使われていた。
これを外すのが面倒だった。フィラメントに巻きついていてカッターナイフで切ろうとしたが上手く行かず、
結局フィラメントを切り捨て、20cmほど無駄にしてしまった。
PETGが軟らかいので他社のように固定用穴を通すだけで済む筈だ。
肝心の印刷し易さは申し分無く良い。
下の写真は直立バックロードホーンに使った
ボイド管の下端を保護する部品を印刷した。
円弧上で長さは約200mm、幅15mm、高さ10mmで断面は三角形だ。
全部で6個印刷したが、全く失敗は無かった。糸引きも見られなかった。
印刷温度は以下の様だ。
ノズル温度: 235℃
ベッド温度: 初層70℃
以降は65℃
印刷速度はPrusa Slicerの初期値で印刷した。
29. ホットエンドの温度制御改善 2020,10,12 実施
以前に
ホットエンドの温度制御を改善する為に放熱グリスを使い効果が見られた。
部品を買い集めて自作した白PRUSAでは性能が向上した。
しかし中国製のKitを組立てた黒PRUSAでは温度センサーが固着していて外せず充分に放熱グリースを塗れなかった。
その為に温度制御性能が今ひとつだった。
抜本的な解決を模索していたところAliexpressに
純銅製のヒートブロックが売られているのを見つけた。
純銅はアルミに比べ小さな比熱と大きな熱伝導率が制御性能向上に寄与する筈だ。
早速それを購入して組み込んだ。同時にノズルや導入管、温度センサー、ヒーターも新品に交換した。
これによって伝熱時間が短くなった筈なので
PID calibrationを実施しPID設定を最適化した。
その結果、著しい改善が見られた。
下の写真は、左側が黒PRUSAから取り外したホットエンド。
右が交換用の部品で純銅製のヒートブロックと導入管、ノズルだ。
すべてTrianglelabから購入した。同社には真鍮製も売っているが純銅に比べて熱伝導率が低い。
純銅製のヒートブロックはニッケルメッキされているので銅色ではない。
下の写真は導入管だ。中にテフロンパイプが無いので260℃を超えて使える。
一部が細く括れているのは熱遮断の為だ。この部分は金属が薄く上の写真では外そうとして折ってしまった。
上の写真で折れてヒートブロックに残った導入管の周囲が黒くなっている。
融けたフィラメントが漏れ出て滲んだようだ。導入管とノズルの接合部は突き合わせているだけだ。
構造的に漏れやすいので鉛のシートからガスケットを作り接合部に挟んだ。下の写真で左側にある小さな円盤がそれだ。
組立てて強く締めると鉛が内側に膨らむので1.8mmのドリルで穴の中を削った。
温度センサーも自作した。検出時間を短縮する為に市販のサーミスタを買い自作した純銅製保護管に入れた。
もちろん管の内部には放熱グリースを充填した。
市販品では真鍮のパイプにメッキが施してあるものが殆どだ。
またサーミスタの周囲にチョコッと放熱グリースが在る程度で充填ではない。
下の写真で上が自作した純銅製保護管入り温度センサー、下は市販品だ。
下の写真は組立てたホットエンドだ。ヒートブロックにシリコンカバーを被せてある。
写真では判らないが、熱が伝わる総ての接触部分には放熱グリースを塗った。
下の図は印刷中の改良ホットエンドの温度変化をOctPrintを使って見た様子だ。
設定温度へ到達した直後に僅かに振動があるが収束後は平坦で正確に温度を制御している。
理想的だ。
左半分のギザギザは初層設定でノズルとベッドの隙間を合わせた際の温度変化だ。
下の図は白PRUSAの温度変化だ。上と同じ物を印刷している。Gコードも同じだ。
設定温度到達後も細かな振動が見られる。たぶん5℃程度の揺れ幅だ。
ヒートブロックへ純銅製を組み込んでも印刷への大きな影響は無いだろうと考えていた。
5cm角で厚さ5mmの枠状のテストピースを設計し印刷して試した。
同じPETGフィラメントで同じGコードだ。肉眼では違いは判らなかった。
ところがカメラで接写したところ差異が在り驚いた。
下の写真で上が黒PRUSAの新ホットエンド、下が白PRUSAの印刷だ。
上のほうが糸の太さが揃っている。下は糸の太さが周期的に変化している。
吐出ノズルの温度変化でPETG樹脂の粘度が変わり
ノズルから押し出される糸が太くなったり細くなったりしているようだ。
純銅製ヒートブロックは想定していたよりも大きな効果が在った。
但し純銅製ヒートブロックだけではなく純銅製保護管入り温度センサーの効果も加わったはずだ。
アルミ製ヒートブロックが付いている白PRUSAも純銅製ヒートブロックへ改造する予定だ。
30. 特殊ケーブル・ブッシュの印刷 2020,11,01 実施
屋外用の
WiFi監視カメラを買った。
その電源ケーブルを壁に穴を開けて通して室内に導く予定だ。
その電源ケーブルには先端に太さが22mmのコネクターが付いている。
ケーブル自体の太さは4.8mm程度なので22mmの穴を開けるとガバガバで不細工になってしまう。
そこで穴とケーブルの隙間を埋める為に二つ割のケーブルブッシュを設計し印刷した。
大きさはM22で長さは45mmだ。
そのケーブルブッシュの印刷にはPETGを使ったのだが、驚くほど綺麗だ。
ネジ山に乱れが全く無い。まるで射出成型機で作ったようだ。
従前は、PETGでこれほど精度の高い印刷は難しかった。これならば工業的な生産にも使えそうだ。
過日にBear upgrade PRUSAへ組み込んだ
純銅製ヒートブロックの効果は素晴らしい。
下の写真はケーブルに取り付ける試験の様子です。上手く行きました。
上の写真で
M22ナットのSTLファイルはThingiverseから頂いた。
自分で設計したのは2分割のボルトの部分だ。
我がBear upgrade PRUSAは、こんな小物を作る際も便利で魔法のような道具です。
でも3D-CADでネジを設計するのは面倒だった。
下の写真は実際に取り付けた様子だ。計画通りに完成した。
玄関のアルミ製扉に直径22mmの穴を開けるのが面倒でした。
31. 純銅製ヒートブロックの取り付け、他 2020,12,01 実施
2ヶ月ほど前に黒いPRUSAへ純銅製ヒートブロックを取付けたところ温度制御特性が大幅に改善された。
それに味を占め二匹目の泥鰌を狙って白いPRUSA用に純銅製ヒートブロックを取り付けようとaliexpressへ発注した。
それが届いたので白PRUSAへ組込んだ。
伝熱時間が短くなった筈なので
PID calibrationを実施しPID設定の最適化を行った。
その後に試運転を行った結果が下図だ。今回も素晴らしい性能になった。
下の図は同じ白PRUSAでアルミ製ヒートブロックを使っていた先日までの特性だ。
温度の飽和部に細かなギザギザが見られる。純銅製ヒートブロックでは、これが消えた。
この測定を行った日に
Octprintの更新が在った。
それ以降はOctprintを起動する度に下図のようなメッセージが表示される。正直のところ鬱陶しい。
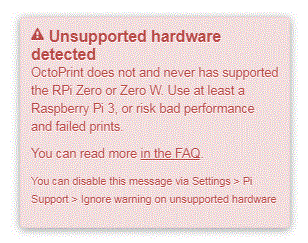
表題は
サポートしないハードウエアが検出されたとの事だが、
中身はRaspberry PIのZeroはダメだと警告している。
Raspberry PIのZeroは
PRUSA RESEARCH社のホームページでも紹介されている。
その記事を参照して我がPRUSAには2台共にRaspberry PIのZeroを組み込んである。
昨日に見たところ
内容の説明が少し変わっていた。
趣旨は 、RaspberryPIのZero処理能力は低いが、大きなプラグインを使わなければ使えると書いてあった。
OctoPrintが使えないと大変に困る。そこで試してみたところ、基本的な機能は動いた。
WiFiを通じて印刷データの送信やノズルとベッドの温度設定も出来るし、
XYZ軸の手動操作やフィラメントの送り出しも問題ないが、
Printボタンの反応が遅れる。
Printボタンを押してから過熱が始まるまでに30秒程度も掛る。従前には無かった事だ。
しかしプラグインには正常に機能しないのが在った。
Prusa Mesh Levelingはエクストルーダを移動させPINDAセンサーを使って測定動作を行うが、
結果が表示されなかった。以前は20秒程度の後に表示されたが、この更新以降は待ってもダメだった。
しかし機能が似ているPrusa Leveling Guideは動いたので支障は無い。
この後、下の写真の印刷を行った。
これは直立バックロードホーン・スピーカー用のSPマウントだ。
今まで使っていたSPユニットが消耗したので新しいSPユニットを入手した。
従前のSPユニットとは少し寸法が違うので設計を修正し印刷した。
我が工作では3Dプリンターは必要不可欠な道具だ。
32. OctPrint非サポート対応 2020,12,04 実施
12月1日にOctPrintの更新が在り、それ以降は起動する度に
下の写真のように
非サポートのハードが検出されたと警告が表示される。
趣旨はRaspberry Pi Zeroをサポートしないという事だ。
そればかりかprintのボタンをクリックしてから加熱が始まる迄に30秒程度も遅れる。使い辛いし
鬱陶しい。
新Version(14)では自分が使わない機能が増えOctPrintが肥大したのだろう。
OctPrintを以前のVersionへ戻してしまえば解決できそうだ。しかしOctPrintには戻す機能が無いようだ。
そこで
対策を考えた。
旧バージョン(13)は、PRUSA RESEARCH社が開示している Raspberry Pi Zero用イメージ(PrusaPrint)に
残っている筈だ。そこで新しいマイクロSDカードを用意し
手順の説明に従ってPrusaPrintを書き込んだ。
これをRaspberry Pi Zeroに差込み白PRUSAへ取り付けて電源投入。
IPアドレスの確認に手間取ったが無事に動いた。狙い通り
非サポートのハードが検出警告は出なくなった。
OctPrint起動の直後に設定窓を開き、Plugin Managerを起動してSoftware UpdateとCuraEngineをOffにした。
これでOctPrintは更新されない筈だ。またCuraは使わないので止めた。
自分のPrusaには
Nylock
Bed Levelingを組み込んである。
Nylock Bedの調節にはPrusa Leveling Guideが必要だ。そこで外部からPlugin を組込んだ。
これはdefaultには無い機能なので外部のWebから読み込まねばならなかった。
https://plugins.octoprint.org/plugins/PrusaLevelingGuide/
https://github.com/scottrini/OctoPrint-PrusaLevelingGuide/archive/master.zip
この状態で試運転を行ったところ、自分に必要な機能は正常に動いた。しかも従前よりも軽快だ。
同じ日にOctPrintへ
ビデオカメラを取付けた。
半年ほど前にAliexprssへカメラとケーブルを発注したが、
疫病の騒動で発送された荷物が行方不明になってしまった。長期間待たされたが届かず代金払い戻しを受けた。
その後に別の店へ発注した商品が届いていた。
ラズベリーパイ用カメラは\400-、
専用ケーブル(30cm)は \240-だった。
驚くほど廉い。
OctPrintの書き換え作業に合せてビデオカメラを取付けた。腕木はX軸駆動モーターに取り付けてある。
腕木とカメラ基板用ケースは自分で設計した。灰色のフィラメントを使ったので少し地味だ。
赤色で印刷すれば良かったかもしれない。問題が無ければThingiverseで開示するつもりだ。
映りは下の写真のようだ。白飛があるが、この用途には充分だ。
それにしても400円のビデオカメラで写した画像がこれだ。技術の進歩は素晴らしい。
33. 温度の齟齬と対策 2021,01,24 実施
Triangle製のキットを組立てた黒色と、自分で部品を買い集めて組立てた白色の2台のBear Upgrade PRUSA i3
MK3を運用している。
整備した後や新しいフィラメントを使う際にはFirst Layer Calibrationを行いノズルとベッドの隙間を最適にして印刷する。
最近First Layer CalibrationをPETGで実行していて問題が発生した。
黒PRUSAでは問題なく印刷できたのだが、白PRUSAでは黒と同じフィラメントを使い同じ温度でも途切れてしまう。
印刷を始めた直後は良い感じなのだが、中頃から掠れだす。
原因を探してノズルを分解したり冷却部の詰まりを調べたが問題はなかった。
フィラメントを送り出すモーターの脱調やギアも点検したが異常はなかった。
試行錯誤の挙句、温度制御に問題が在りそうだった。このところ室温が12℃程度と寒かったので顕著になったのだろう。
そこでノズルの温度を230℃に設定して赤外線温度計でノズルの温度を測ってみた。
その結果、 黒
PRUSA:187℃ 白PRUSA:174℃ で13℃ほど白PRUSAの方が低かった。これが原因だった。
赤外線温度計は測定対象の表面状態によって測定精度が変わるので絶対値との誤差はわからないが、相対的な誤差はわかる。
またヒートブロックの表面温度は設定値よりも低い可能性もある。
温度差の原因はヒートブロックに差し込んでいるサーミスタの検出特性がバラついている為と推定した。
そこで予備のサーミスタが3本あったので取り換えて温度を測ってみた。
の結果、 #1:179℃ #2:
189℃ #3:
186℃ だった。
この結果から#2のサーミスタを組込みFirst Layer Calibrationを実行したところ上手く印刷できた。
問題の原因はサーミスタのバラツキだった。PETGはPLAに比べて印刷に最適な温度範囲が狭いようだ。
PLAでのFirst Layer Calibrationならば問題にならなかったのかもしれない。
34. ヒートベット用電線カバーの製作 2021,02,01 実施
オリジナルのPRUSAでは、ヒートベッドに繋がる電線が本体の真後ろ方向へ突き出している。
Clone PRUSAでも同じだ。我が家では3Dプリンターを机上の壁際に設置してある。
部屋が狭いのでヒートベッドが後ろへ下がった場合に電線が壁に当たる。
当たっても電線が曲がるので直ちに問題は無いが、
カバーとの接続部が急角度で曲がるので長期的には断線を誘発する要因だ。
リスクを解消する方法を探していて良いアイデアを見つけた。
Thingiverseに
Prusa i3 MK3 60 degree heatbed cable coverを見つけた。
早速ダウンロードして印刷し取付けたのが下の写真だ。
取付けた後に動かしてみるとヒートベッドが後ろへ下がった場合に電線が繰り出す長さは、
少し短くなった程度だが、電線が曲がる場所が一か所に集中せず緩やかに曲がる。
断線リスクは軽減されたと思う。
従前のカバーと交換するには新設計のカバーを二個だけ印刷すれば済む。
ビスとナットは、そのまま使える。無駄の無い設計だ。
34-1 ヒートベッド用電線カバーの再製作 2021,04,16 実施
過日に作ったヒートベッド用電線カバーには問題が在った。
重力で電線の束が下へ垂れ下がって滑り棒やY軸駆動モーターに接触しそうだ。
そこで下側のカバーを改造した。
ThingiverseからダウンロードしたSTLファイルを
Freecadへ読み込ませ、
ワイヤーフレーム形式から
ソリッド形式に変換してから改造した。
これをSTL形式でExportしてスライサーソフトへ渡しG-cordeに変換して印刷した。
改造したのは下側カバーの電線引き出し部だ。そこを5mmほど延長し下へ垂れにくくした。
下の図で左が改造前、右が改造後だ。
改造したSTLファイルで印刷しPRUSAへ取り付けたのが下の写真だ。
黒いフィラメントを使うと写真写りが悪いので赤いPETGを使った。
上側のカバーには手を加えてないが色を合せる為に赤色で印刷した。
延長した下側のカバーが、電線の束を支えている。問題は改善されたようだ。
Aliexpressで売られているヒートベッドの電線接続には半田付けと圧着端子接続が在る様だ。
TriangleLabから買ったKitの黒PRUSAは半田付けで、この電線カバーが使えた。
個別の部品を買い集めて作った白PRUSAは
圧着端子接続だった。
圧着端子が大きく、この電線カバーの中で電線を曲げられず
使えなかった。
35. PEIシートの剥離 2021,02,21 実施
印刷台に磁気で吸着させる鋼板にPEIシートを貼って使っていた。
そのPEIシートが長期の使用により劣化した。
貼りかえる為に剥がしたのだが、簡単には剥がせず悪戦苦闘した。
指先でつまんで剥がそうとしたが、粘着剤が強力で剝がれない。
そこで鋼板を冷蔵庫で凍らせて剥がそうとした。
部分的に取れたが、剥がせないのでペンチで引っ張ったらPEIシートが割れてしまった
その上に綺麗に剥がれた部分は粘着剤が鋼板側に残ってしまった。
仕方なく少し剥がして伸びた粘着剤をスクレーパーで切るようにして剥がした。
何とかプラスチックシートは剥がせたが、全面に粘着剤が残った。
その粘着剤をスクレーパーで削り取ろうとしたが、強靭で取れなかった。
粘着剤を軟化させるために鋼板をポリ袋へ入れ無水エタノールを入れた。
鋼板の上にはティッシュペーパーを被せエタノールが鉄板の上に滞留するようにした。
この状態で約1日放置した。
軟化した粘着剤をスクレーパーで掻き取った。粘着剤の白い塊が幾つも出来た。
何とか頑張って実用上問題ない程度に削り取った。
スクレーパーでゴリゴリやったので印刷の白線が掠れてしまった。
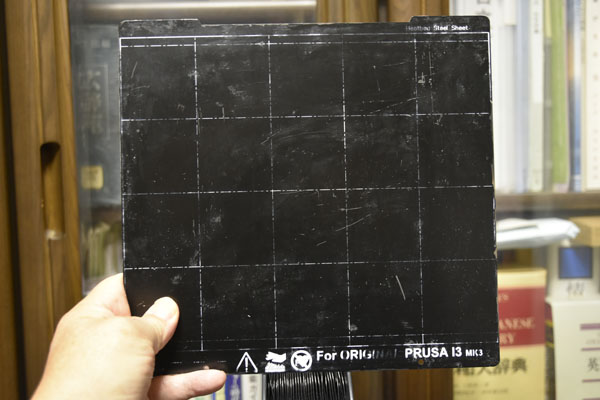
PEIシートは大変に剥がし辛く愛想が尽きた。
36. 代替PEIシートの実験 2021,02,21 実施
ベッドに貼るPEIシートは剥がしにくい上に1枚が千円程度と高コストだ。
代替用に安価なガラス飛散シートを探した結果、2個が見つかった。
実験の結果、2回目に試した
リンテックコマース社のフィルムが特に良かった。
以下に詳しく説明する。なお追試される方は自己責任でお願いします。
実験1.ダイソー ガラス飛散防止安全シート
◎使用の可否
:
使える。但しPETGしか使わないのでPLAやABSでは判らない。
◎コスト
:
安い!!。1個で4枚程取れるので1枚あたり27.5円だ。
◎印刷物定着
:初層校正は定着するが、印刷には
スティック糊が必要。
◎材質
:PET樹脂
◎強度
:弱い。スクレーパーを使うと破れる事がある。厚さが0.05mmと薄いのが原因か。
◎加熱による変形 : 膨張や収縮は見られなかった。
◎粘着力
:
少し弱い。印刷物を剥がす際に少し浮き上がる。押さえれば戻る。
◎剥がしやすさ : 容易に剥がせた。鋼板に粘着剤が残らない。
下の写真はダイソーのフィルムを貼って20回くらい印刷した後だ。
引延し機用レンズを拡大撮影に使う為のアダプターを試作した。
白いのは定着の為に用いた水溶性スティック糊の跡だ。
水で洗えば簡単に流せるのだが、横着で洗わずに使っている。
中央にスクレーパーで破った小さな穴が在る。
実験2.リンテックコマース 防災凸凹ガラス用シート
◎使用の可否
:
使える。但しPETGしか使わないのでPLAやABSでは判らない。
◎コスト
:
1300円。1個で6枚程取れるので1枚あたり216円だ。
◎印刷物定着
:表面が艶消しで
強く定着する。定着力を下げる為に
スティック糊が必要かも。
◎材質
:ポリカボネート樹脂
◎強度
:強い。スクレーパーでは破れそうにない。
◎加熱による変形 : 膨張や収縮は見られなかった。
◎粘着力
:
充分。印刷物を剥がす際にも浮き上がらなかった。
◎剥がしやすさ :
剥がせた。鋼板に粘着剤が残らないが、試験回数不足だ。
下の写真はリンテックスコマースのフィルムを鋼板に貼って
MakerBot GnomeをPETGフィラメントで印刷した様子だ。60%に縮めて時間を短縮した。
スティック糊は使っていない。目的は印刷物の剥がしやすさを試す為だ。
印刷終了後に印刷物を外そうとしたが、強く定着しており鋼板を撓めても取れなかった。
仕方なくGnomeを手で掴んで横に倒したらバキッと音を立てて外れた。
これを2回印刷して試したが2回とも同じ結果だった。
フィルムは剥がれたりせず割れもしなかった。このフィルムは大変に強いようだ。
今後に大きな物を印刷する際には、スティック糊を使って定着力を減らした方が良いのかもしれない。
実験 3.リンテック ガラス用シートとスティック糊の併用
リンテックスコマース社の防災凸凹ガラスシートに糊を併用して印刷してみた。
ガラス用シートだけでは定着力が強すぎると感じたので定着力を弱める魂胆だ。
その結果が下の写真だ。
スティック糊を塗っても定着力は強く端部もガッチリと着いていて剥離は全く無かった。
肝心の造形物の取り外しは、鋼板を撓めるだけで印刷物の端が浮き上がり手で剝がせた。大成功だ。
リンテックスコマース社のガラス用シートとスティック糊の併用は、過去最良だと思う。
印刷したのは
円筒直立型バックロードホーン用の部品だ。
大きさは、直径126mm、厚さ9.5mmでフィラメントはPETGを使った。
使用したスティック糊は百均のセリアで買った物を使ってみた。(下の写真の上)
いつもはダイソー製を使っている。どちらも3Dプリンター用に適している。
どちらも成分はPVP(ポリビニールピロリドン)で中身は色も硬さもそっくりだ。
PVPは水溶性なので後始末が楽だ。水で洗い流せば済む。
事務用品店には水に溶けにくいスティック糊も売られている。
それらの中には乾固した糊を剥がすのが面倒な物も在るので要注意だ。
スティック糊を使えばフィルム無しで鋼板に直接印刷する事も出来る筈だが鋼板を傷付ける事故が心配だ。
我がBear Upgrade PRUSAでPETGを印刷する場合に印刷物が部分的に剥離し、
それが丸められてベッドとPINDAの間に挟まりPINDAを持ち上げてしまう事故が過去に3回も在った。
何れも2層目か3層目を印刷していた時に起こった。
その結果、相対的にノズルが下がり過ぎて鋼板の塗装を削りノズルを痛めてしまった。
その際に鋼板にフィルムが在ると被害が軽減できる。
廉くて丈夫なフィルムが見つかって良かった。
実験 4.リンテック ガラス用シートとスティック糊の併用 2回目
リンテック ガラス用シートとスティック糊の併用で2回目の印刷を行った。
印刷したのは下の写真に写っている
マイク用の防振スタンドだ。
大きさは縦130mm、横100mm、高さ15mmだ。
印刷は全く問題なく終了した。印刷物を剥がす際も鋼板を捩って剥がせた。
剥がした感じは最初の印刷よりも定着力が弱くなっている様だったが丁度良い。
今の所、リンテック ガラス用シートとスティック糊の併用には
何の問題も無い。
実験 5.リンテック ガラス用シートとスティック糊の併用 3回目
リンテック ガラス用シートとスティック糊の併用で3回目の印刷を行った。
印刷したのは下の写真に写っているだ
ヒートベッド用電線カバーだ。。
大きさは下側カバーが縦23mm、横37mm、高さ6mm、
上側カバーは縦39mm、横40mm、高さ9mmだ。
印刷は問題なく綺麗に出来上がったが、鋼板への定着が強く捩っても印刷物を剥がせなかった。
仕方なくスクレーパを使って外した。リンテック ガラス用シートには傷は付かなかった。
カバーを設計した段階で
底面の周囲を45度で幅0.8mmの面取りをしていたので
スクレーパーの刃先が印刷物の下側へ食い込みやすく具合が良かった。
37. PETGの接着 2021,03,17 実施
自分の3Dプリンターによる造形では、サポート、筏(Raft)や鍔(Brim)を使わないように設計する。
成型後、外すのに手間が掛るのとサポートでは寸法精度を確保するのが難しいと考えているからだ。
そこで必要なのが接着だ。PETGの接着にはアクリサンデーを使っている。
アクリサンデーは接着剤だが一般的な接着材とは異なりサラサラの溶剤だ。
通常の接着剤は二つの接着対象の間に入って結びつける糊の様な物だ。
ところがアクリサンデーは接着対象を溶かして溶着させる。
通常の接着剤との大きな違いは、アクリサンデーには隙間を埋める性質が乏しい事だ。
下の写真は
円筒直立型バックロードホーン用の部品を接着している様子だ。
接着したい赤と黒の部品を合わせてバイスで締めて密着させている。
その赤と黒の接合面にアクリサンデーをスポイトで滴らし毛細管現象で接合面の隙間に吸わせる。
下の写真は、黒い色のスピーカーマウントと赤いゲル押さえリングを接着した後だ。
スポイトの操作が下手で沢山のアクリサンデーを滴下したために溢れ出た液の痕が残っている。
しかし接着は大成功でガッチリと着いた。手で力を加えても撓まず剥がれない。
完成したスピーカーマウントを
直立円筒形バックロードホーンへ組み込んだ。
38. PINDA V2 センサー温度補正の校正 2021,04,05 実施
ノズルと鋼板の間隔を検出するPINDAセンサーは周囲温度によって検出距離が変わり誤差を生じる。
温度の影響を排除し誤差を軽減する為にV2では内部に温度を測るサーミスターが組込まれている。
自動温度補正のスイッチをONに設定するとサーミスタが測った温度を基に検出された距離の補正が行われる。
ところがPINDAセンサーの性能にバラツキがあり個々のセンサーに合わせた
補正データを制御コンピュータに覚えこませねばならない。
PRUSAのファームウエアには補正データを自動的に取得する機能が組み込まれている。
我がPRUSAは過去にPINDAが故障し交換した。その後、補正データの取得を行っていなかった。
四月に入りPRUSAを設置している暖房も冷房も無い部屋の温度が21℃になった。
補正データの取得条件が揃ったので
Calibrationを実施した。
補正データ取得の操作は以下の様に行った。
先ずメニューから
Calibrationを選ぶ。
Calibrationの項目から
Temp. Calibrationを選ぶ。
Calibrateを選んで補正データの取得を開始。
初めに実施条件が提示された。
周囲温度が21℃から26℃で丈夫な台が必要だそうだ。揺れを嫌っているようだ。
その後、ヒートベッドに鋼板を載せているかとの質問。
Yesと答えたら鋼板を外せとの指示。
鋼板を外し操作ノブを押したら補正データの取得が始まった。
第1段階はヒートベッドの温度が75℃で補正データの取得。
第2段階はヒートベッドの温度が70℃で補正データの取得。
第3段階はヒートベッドの温度が80℃で補正データの取得。
第4段階はヒートベッドの温度が90℃で補正データの取得。
第5段階はヒートベッドの温度が100℃で補正データの取得。
第6段階はヒートベッドの温度が110℃で補正データの取得。
第6段階が終ると補正データの取得を終え自動温度補正のスイッチを
ONに設定したと告知。
メニューから
Setting->Temp.calを選ぶと自動温度補正のスイッチが在るのでOFFを選べる。
操作ノブを押したら補正データの取得を終え初期画面に戻ったが、
Temp. calの表示は消えなかった。Bugか?
以上の操作でPINDAの自動温度補正が働くようになった筈だ。
開始から終了までに30分近くかかった。
昨年Prusa resarch社から自動温度補正が不要なSuper PINDAが発表された。
最新のPRUSAには採用されているらしい。
PRUSAのPINDA V2はフィラメント導入管を冷却した温風の出口に固定されている。
その為に印刷を開始すると温度が上がってしまう。
印刷終了後、直ちに次の印刷を始めるとPINDAの温度による検出誤差が問題になる。
自分の場合には過去にノズルを鋼板に当てて傷つけてしまった経験がある。
そのような事故を避ける為にPINDAの温度補正は適切に使いたい。
39. X軸傾斜対策 2021,04,15 実施
PRUSAではZ軸を上下させる為に左右に2個のモーターを組込んである。
印刷を終えて電源を切った際に各々のモーターは電気的な制御から解き放たれ
僅かだが機械的もしくは磁気的に安定な位置へ移動する。
X軸駆動モータはX軸の左側に設置されているのでX軸は左側が重い。
その上に普通はエクストルーダが左側で印刷を終えるので更に左側が重くなる。
その為に電源を切った瞬間に
X軸が僅かに左側へ傾く事が多い。
少し傾くと機械的な摩擦が増えるので傾きは進行しないし、
PINDAによる自動補正が働き
実害は無い筈だ。
自分のPRUSAにはNylock-Spring Levelingを組み込んである。
印刷台の凸凹を0.03mm程度まで絞り込める優れた方法だが、
X軸が傾くと相対的に印刷台の傾きが変わってしまう。
これもPINDAによる自動補正が働き印刷への
害は無いが、
次にNylock-Spring Levelingを調節する際に操作量が増えて面倒になる。
この問題を解消するため下記のようにスライサーの
special G cordeに手を加えた。
実施したのは
PrusaSlicerだが他でも適用できると思う。
◎
印刷開始
印刷を始める前にZ軸を上部のストッパーへ当ててX軸を水平に揃える機能を追加した。
M862.3 P "[printer_model]" ; printer model check
M862.1 P[nozzle_diameter] ; nozzle diameter check
M115 U3.9.1 ; tell printer latest fw version
G90 ; use absolute coordinates
M83 ; extruder relative mode
M104 S[first_layer_temperature] ; set extruder temp
M140 S[first_layer_bed_temperature] ; set bed temp
M190 S[first_layer_bed_temperature] ; wait for bed temp
M109 S[first_layer_temperature] ; wait for extruder temp
;
;******* Correct the tilt of the x-axis by Syumijin *******
G28 W ; home all without mesh bed level
G1 Z210 F4000 ; Move the Z axis to the upper limit
G92 Z190 ;
G1 Z210 F1000 ; Apply the Z axis to the stopper
;
G28 W ; home all without mesh bed level
G80 ; mesh bed leveling
G1 Y-3.0 F1000.0 ; go outside print area
G92 E0.0
G1 X60.0 E9.0 F1000.0 ; intro line
G1 X100.0 E12.5 F1000.0 ; intro line
G92 E0.0
M221 S{if layer_height<0.075}100{else}95{endif}
; Don't change E values below. Excessive value can damage the printer.
{if print_settings_id=~/.*(DETAIL @MK3|QUALITY @MK3).*/}M907 E430 ; set
extruder motor current{endif}
{if print_settings_id=~/.*(SPEED @MK3|DRAFT @MK3).*/}M907 E538 ; set
extruder motor current{endif}
◎印刷終了
印刷を終えたらエクストルーダを右へ移動し、
X軸の重量バランスを図る。
なお
Ultimaker Cura4.8を調べたところ初期設定から自分の考えたのと同じ対策が在った。RepRap共通の問題点を知っているようだ。
G4 ; wait
M221 S100 ; reset flow
M900 K0 ; reset LA
{if print_settings_id=~/.*(DETAIL @MK3|QUALITY @MK3|@0.25 nozzle
MK3).*/}M907 E538 ; reset extruder motor current{endif}
M104 S0 ; turn off temperature
M140 S0 ; turn off heatbed
M107 ; turn off fan
{if layer_z < max_print_height}G1 Z{z_offset+min(layer_z+30,
max_print_height)}{endif} ; Move print head up
;
;******* Move X axis to the right end by Syumijin *******
G1 X200 Y210 F3000 ; home X axis
;
M84 ; disable motors
40. 減速ギヤ付きE軸モーターへ交換 2021,05,30 開始
昨年発売されたPrusa Miniのエクストルーダでは減速ギヤ付きのモーターでフィラメントが送られている。
prusa i3 MK3s には減速ギヤは無いのだが、フィラメントの送りが荒く要改良と判断したのだろう。
自分の使用目的では不便を感じてないが、減速ギヤをつけたらどう変わるのか興味が湧いた。
そこで我がbear upgrade prusaに取り付けられる減速機構を
Thingiverseで探したところ幾つかが見つかった。
どれも良さそうなのだが、シャフトの製作が難しそうだった。
そこでAliexpressの品揃えから探したところ
Trianglelabの商品に良さそうな物が在った。
Prusa Miniと同じく3:1の減速比だ。これを組み込むことにした。
(1) 購入と点検
発注から2週間程で到着した。30日は掛ると考えていたので早くて驚いた。
支払った金額は\3,400-だった。送料無しで税金も無かった。
Aliexpressから届いた小箱を開けると中身は下の写真の様だった。
減速ギヤー付モーターの質感は良く高級感がある。
モーターから出ている電線の端には左端に写っているコネクターと同じ物が付いていた。
コネクターには緩み防止の爪が無く180度回しても入ってしまうタイプだ。
いろいろと入っていたが自分のBear Upgrade Prusaで使ったのはモータだけだ。
付属品は異種のプリンターへ広く対応するための配慮と思われる。
ここで問題に気づいた。Bear upgrade prusaに使うには電線の出ている向きが使いにくい。
上の写真でモーターを時計方向に90度回転させた位置が具合が良い。
モーターの四隅に在るビスを外せそうだが、モーターがバラバラになりそうだった。
ウジウジしていても埒が明かないので思い切って四隅のビスを外したところ、
ギヤ部からモーターが外れた。何故かモーターは原型を保っていた。
モーターを90度回転させ具合の良い位置でビスを締めた。
次にモーターの回転試験を行った。
制御基板のE軸モーター用コネクターを抜き、そこへ新しいモーターのケーブルを差し込んだ。
手動操作でノズルの温度を230℃まで上げてから、同じく手動操作でフィラメントを10mm出す操作をした。
prusaには故障を防ぐ保護機能が在り、ノズルの温度が低いとE軸が回らない仕組みになっている。
自分の場合には便利なのでOctPrintを使いパソコンのブラウザーで操作した。
モーターは無事に回った。回転方向も正しかった。
コネクターの金属が見える小窓が並んでいる面をprusaの正面方向にした。
若しも回転方向が逆だったらコネクターを抜いて180度回して差し込めば修正できる。
(2) 組込み
下の写真のようにエクストルーダーを本体に取り付けたままで分解しモーターを外した。
自分のエクストルーダーはBear upgrade prusa用なのでオリジナル用とは違うかもしれない。
適切な分解の方法を忘れてしまい不必要な部分まで外してしまった。
しかしX軸駆動用のベルトは外さずに済んだ。
取り付ける作業は面倒だったが、想定したとおりに収まり何も問題は無かった。
組立てに使うM3のビスは、外した物が総てそのまま使えた。
モーターが従前の位置より左へ12mm移動したが、前への出っ張りは無かった。今度のモーターは薄い。
また重量の増加を危惧したが、従前と同じか少し軽いと感じた。
調べた所オリジナルは270gで減速ギヤ付は220gだったので概ね50g軽い。
商品には放熱器が付属していたが、取付けていない。
印刷中にモーターの温度を赤外線温度計で測ったところ46.5℃だった。
気温が約33℃だったので発熱は13.5℃だ。この程度なら放熱器は不要と判断した。
(3) ファームウエアの設定値変更
モーターを減速ギヤ付きに変えたので組込み制御ソフト内の設定値を変更しなくてはならない。
prusaにパソコンを繋ぎターミナルモードで命令を入力すれば減速比を書き換えられる。
しかも一度書き換えれば電源を切っても保持される。prusaは素晴らしい。
prusaのファームウエア(組込み制御ソフト)は、当初から修正を想定していたようだ。
スライサーの設定には手を加えない。従前のモーターを使っているpurusaでも
スライサーが出力した同じGコードのファイルで印刷できる。
自分は2台のprusaを使っているが不便は無い筈だ。
変更手順の詳しい説明はココにあります。
自分はOctPrintのターミナルを使ってWiFiで以下のコマンドを順に書込んだ。
もちろんUSBでパソコンと繋いでも出来る筈だ。
M350 E16
M92 E420 (TriangleLab社の指定値)
M500
何かの不都合が生じて元へ戻す場合には下記です。
M350 E32
M92 E280
M500
設定値の変更を終えた後に、上の写真の赤いテストピースを印刷した。
無事に印刷が済んで改造の完了を確認できた。今の所、この
改造による性能低下や不都合は全く無い。
減速ギヤからの騒音を危惧したが杞憂だった。
(4) 印刷試験と結果
テストピースを設計しPETGで印刷して評価した。
下の写真で左側にあるAがモーター交換前で右側に在るBが減速ギヤ付きモーターへ交換後だ。
どちらもキッチリと印刷されており差異は殆ど無い。僅かに交換後の方が文字の周囲が平坦に見える。
また枠の上部もBの方が高さが揃っているように見える。Aは高さ方向に僅かに畝っているようだ。
枠の高さを測ったところA:10.02mm、B:9.98mmだった。Aは畝った分だけ高い。その差は0.04mmだ。
五角形の底辺と頂点までの長さを測ったところA:35.97mm、B:35.87mmだった。
使っているノズル径が0.4mmなので0.1mm程度は仕方の無い誤差だが、やはりBの方が小さい。
(5)
考察
Webに見られる情報では、減速ギヤ付きモーターによって印刷の質が向上すると書かれている。
では何故に我がbear upgrade prusaでは効果が少なかったのか考えた。
フィラメントは冷えた状態で間歇的にヒートブロックへ送り込まれ加熱溶解される。
その際にアルミ製ヒートブロックだと検出遅れが生じ僅かだが温度が乱れる。
フィラメントの間歇的な供給は温度制御を乱す要因(外乱)だ。
温度が乱れればフィラメントの粘度等の物性が変化しノズルが吐出したフィラメントの
太さが微妙に変わる。これが印刷の乱れになる。
間歇的なフィラメントの供給が、減速ギヤ付きモーターによって連続に近くなれば
温度制御を乱す要因(外乱)が小さくなり印刷の乱れが減る。
自分のbear upgrade
prusaは温度の制御性能を改善する目的でヒートブロックを
純銅製に替えて在る。その為に温度変化への追従がアルミ製に比べ格段に速い。
フィラメントの供給が、間歇的でも温度は乱れないので印刷も乱れないのだろう。
しかし小さな歯車を印刷した場合には印刷精度が上がるのでは?、と期待している。
(6) 小さな物の印刷試験
小さな物を印刷したら印刷精度が上がるのでは?、との疑問から試した。
印刷したのはPrusaの分解や組立てで頻繁に使うM3六角レンチ用グリップだ。
M3六角レンチは全体が細く回し辛かったので、この機会に作ってみた。
外径は約8mm、中心に六角の穴があり向かい合う平行辺の距離は2.8mmで設計した。
六角レンチの棒の部分の向かい合う平行辺の距離は2.48mmなので隙間は0.32mmだ。
隙間が広いが、ノズルの径が0.4mmなので丁度良さそうな2.6mmは選べないので仕方ない。
握りの部分には幅0.8mmで滑り止めのローレット加工風ギザギザを施した。
印刷は良い感じに仕上がった。穴に六角レンチを通した感じも少し緩く設計と符合した。
六角穴の向かい合う平行辺の距離をノギスで測ったところ2.76mm位だった。
ノギスで小さな穴の寸法を正確に測るのは難しいが、概ね設計通りに出来ていた。
従前のエクストルーダーでは小さな穴を正確に印刷するのは難しかったが、
減速ギヤ付きのモーターの採用により、印刷の細部の精度が向上した。
上の写真は印刷したグリップの端部を拡大した。その六角穴の左下方向に糸引きが見える。
これは印刷が終わったらノズルを引き上げるのだが、その際の糸引だ。
従来はもっと太く長かったのだが、細く短くなった。何故だか判らない。
(7) まとめ
減速ギヤ付きモーターは印刷物の細部の造形が良くなるようだ。
3Dプリンターの使用目的が小さな造形の場合には効果が在りそうだ。
これからprusaを組立てるのならば最初から減速ギヤ付きモーターを組み込んだほうが
良いかもしれない。少なくとも悪くなった所は見られない。
既に完成したprusaの場合にはエクストルーダと電線の束の分解と組立てが面倒だが、
造形の目的によっては減速ギヤ付きモーターの効力が発揮されるかもしれない。
41. 換気口通線計画 2021,08,14 開始
3Dプリンターは有害な微粒子を大気へ出すという説があるが、真偽の程は判らない。
しかし妻が心配して部屋の中で印刷するなと言い出した。
仕方なく3Dプリンターをベランダへ持ち出して印刷している。
外では風が影響するので段ボール製の囲いで覆っている。
また冬場には温まりやすいようにアルミの断熱フィルムを段ボールに貼っている。
段ボール上には段プラの板を被せて冷えないように工夫している。
問題は電源だ。ベランダにコンセントは無いのでガラス戸を少しだけ開けて電線を通し
室内から給電している。当然隙間から夏は熱気が、冬は冷気が入る。
我が家は鉄筋コンクリートで作られた集合住宅だ。
ベランダとの間を遮る室内の壁には下の写真のような換気口が設置されている。
これを通線路として利用できれば隙間風の問題が解消される。
下の左側の写真は換気口の拡大で右は外した穴だ。内径100mmのメネジが在った。
この換気口に捻じ込める通線穴付の蓋を印刷できれば電源線を通せる筈だ。
(1) ネジ部の試作
この試作で難しいのはネジの設計と印刷だ。そこでネジ部の評価モデルを設計し印刷した。
外した部品(レジスターと呼ぶらしい)のネジ山をノギスで測り設計した。寸法は下記の様になった。
ネジの底の直径:97.4mm ネジのピッチ:2.6mm ネジ山底辺の長さ:1.8mm
ネジ山の立上がり角度:60度 ネジ山の形:正三角形
印刷した試作品を換気口に捻じ込んだところ、問題無くスムースに入った。
これで
ネジ部の設計が正しかった事を確認できた。計画を次の段階へ進められる。
この印刷はエクストルーダのモーターを
減速ギヤ付きに換えてから初めての本格的印刷だった。
その出来栄えに驚いた。表面に乱れが無く射出成型で作ったようだ。これなら工業生産にも使えそうだ。
また従前のエクストルーダでは印刷終了時の糸引きが防げなかった。
従前から引き込み長さを変える等の解決策を模索したのだが成功しなかった。
その難題が減速ギヤ付エクストルーダに換えた事で嘘の様に消えた。減速ギヤ付エクストルーダは素晴らしい。
(2) 電線保持部の試作 2021.08.18 実施
電源コードの先端にあるプラグはメーカーによってバラツキがあるが、27mm程度の穴が開いていれば通せる。
そこで余裕を見て直径30mmの丸穴を中央部に設け、通線後に二つ割のブッシングで電線を挟み固定する構造にした。
扇状の穴には、裏から目の細かい網を接着し蚊やハエなどの侵入を防ぐ予定だ。
試作した電線保持部を壁に取付けてみたところ想定通りだった。
取りけや取外しの際に放射状の穴へ指を差し込んで回せて便利だったのは想定外だ。
中央の環状の部分と放射状の部分では厚さを2.4mmで設計した。
手で力を加えても撓んだりしないので充分な強度が在るようだ。
次に似たような物を設計する際は1.6mm程度にするつもりだ。
(3) 白色フィラメントで造形
室内に取り付けるには白が良いと妻が言うので新たに白色のPETGフィラメントを買って印刷した。
前回の印刷とほぼ同じだが、電線保持部の丸穴を電線に合せて楕円穴に変更した。
下の写真では小虫の侵入を防ぐために目の細かい網を接着してある。
網は台所の水切り籠に被せる使い捨ての網袋を切り開いて接着した。
調べた所、換気孔の外側にも内側と同じメネジが在った。
そこで先に作った赤色を捻じ込んで見た所スンナリ収まった。
この後、網を接着して換気口通線計画は無事に完成した。
(4) TINMORRY製PETG
換気口通線計画で白のPETGが必要になった。
Amazonで調べた所、TINMORRYという聞いた事の無いフィラメントが\2,399-で売られていた。
しかもAmazon's Choiceになっていたので、これを買った。
印刷条件はeSunの赤色と同じで初層235℃ ー 70℃、以降230℃ - 60℃で問題無く印刷できた。
箱を開け真空包装の袋を鋏で切って使おうとしたらスプールに巻かれた状態のフィラメントに
更に食品用に似たラップが巻かれていた。ラップは何の目的か判らない。
刃物を使うとフィラメントに傷が付きそうだったので端部を見つけ剥がしたが手間取った。
今までに沢山のPETGを使ったが、ラップが巻かれていたのは初めてだ。
その数日後にAmazonでPETGフィラメントを調べたら同じ値段でeSun製が売られていた。
しかもAmazon's Choiceだ。今ならeSun製を買うだろう。
42. P.I.N.D.A プロテクターの取付け 2021,09,07 実施
PRUSAではノズルとベットの隙間を測定するためにP.I.N.D.Aと呼ばれる磁気センサーが使われている。
( 面倒なので以降はPINDAと記述する。) 不注意からPINDAが上に移動する事故が発生した。
事故の再発を防ぐ為にPINDAにプロテクターを取り付けた。下の写真で赤いのが、それだ。
(1) 事故の状況
prusaスライサーでSTLをGコードへ変換すると、
印刷の最初にベットの左最下部へintro lineと呼ばれる太く厚い線を描く。
印刷が終わった後には取去るべきなのだが、それを忘れ3度も印刷した。
その結果、intro lineの山ができて高さが1mm以上になった。
PINDAがその山に乗り上げ持ち上げられてしまった。
過去にはベットから剥がれた印刷物にPINDAが乗り上げ同様のトラブルを起こしている。
(2) 事故の被害
PINDAが上に持ち上げられても、その印刷は無事に終わった。
ところが次の印刷でノズルがベットを引っ掻いて傷を付けてしまった。
次の印刷ではPINDAが上に在るので相対的にノズルが下へ下がりベットに当たる位置に至ってしまう。
その結果、ベットの上に貼ってあった
代替PEIシートに深い凹み傷が着き使えなくなってしまった。
不幸中の幸いだが、
代替PEIシートはポリカーボネート製で強度が高かったのでベットの鋼板に傷は見られなかった。
代替PEIシートは剥がすのが簡単なので貼り換えは楽に済み、出費も僅かだった。
(3) 再発の防止-1 ( プロテクターの取り付け )
PINDAが上に移動しないようにすれば事故は防げる筈だ。
そこでthngiverseの中を探したところ良さそうなプロテクターを見つけた。
Prusa i3 MK3
PINDA sensor protector との名称で公開されている。
このプロテクターは高さが10mmで設計されていた。
自分のPINDAは下部の長さが11mmだったので取付けると1mmの隙間ができてしまう。
これでは具合が悪いのでSTLファイルを改造して11mmにした。
これを取付けた所、PINDAの先端とプロテクターの先端が揃って良い感じだった。
この後に初層校正を実施して機能的に問題ない事を確認した。
(4) 再発の防止-2 ( intro lineの改造 )
intro lineが太く高く盛り上がるので問題が生じた。何故このように盛り上げるのか理解できない。
同じ長さのフィラメントを消費すれば良い筈と考えprusaスライサーの
special G cordeの印刷開始部に手を加えた。
以下の様にntro lineのX軸移動距離を100から200へと倍増させ細く長い線にした。
G28 W ; home all without mesh bed level
G80 ; mesh bed leveling
G1 Y-3.0 F1000.0 ; go outside print area
G92 E0.0
G1 X60.0 E9.0 F1000.0 ; intro line
G1 X200.0 E12.5 F1000.0 ; intro line
G92 E0.0
M221 S{if layer_height<0.075}100{else}95{endif}
; Don't change E values below. Excessive value can damage the printer.
{if print_settings_id=~/.*(DETAIL @MK3|QUALITY @MK3).*/}M907 E430 ; set
extruder motor current{endif}
{if print_settings_id=~/.*(SPEED @MK3|DRAFT @MK3).*/}M907 E538 ; set
extruder motor current{endif}
このGコードで印刷したところ想定通り細く長い線が引けた。印刷後に剥がすのも従前よりも簡単になった。
43. 歯付タイミングプーリーを再交換 2021,09,30
実施
先にX軸とY軸のタイミングプーリーを歯付に換えて騒音低減に大きな効果が在った。
その際は歯付タイミングプーリーの軸穴が5mmの物しか入手できず穴を3mmへ縮めるスリーブを印刷して誤魔化した。
最近、
aliexpressの商品を眺めていたら穴径が3mmの歯付タイミングプーリーを見つけた。
早速注文し3週間後に手元へ届いた。商品の寸法を調べたところ従前に比べ若干問題が在った。
ベルト幅は6mm用だが、使っている5mmのベルトでも使えそうだった。
大きな問題は、両端の鍔の厚さが0.5mm位厚かった。両側合せて1mmになる。
従前品の厚みが9mmなのに対して10mmも在る。これでは枠に収まらない。
下の写真は左から歯無し、歯付5mm穴、歯付3mm穴だ。赤いのは今日まで使っていた枠とスリーブだ。
厚みが10mmで既存の9mm用枠には収まらないので、Thingiverseで探したところ
Bear Extruder X End Idler Mount using E3D Gates Powergrip® 2GT Toothed Idler 6mm Belt
を見つけた。
STLファイルをダウンロードしてFreeCADに読み込み寸法を調べたら厚みが10mm用に設計されていた。
これを印刷して組み込んだ。下の写真で白いのが10mm用だ。
Y軸用のプーリーマウントも同様にThingiverseを探したのだが、幅10mmのプリーで使える物が見つからなかった。
そこで最も近いと思われる
E3D 20T Idler compatible mount for Y-Axisのy_idler_23.stlをダウンロードし
STLファイルをFreeCADで修正して幅10mmのプリーに対応させた。印刷したのが下の写真だ。
再交換の作業は恙無く終えた。印刷したところ騒音は従前と変わりなかった。
印刷精度への影響は判らない。悪くなった所は無さそうだ。
44. PID Calibrationのすすめ 2021,10,14
時折読者から相談のメールを頂く。多いのは印刷物のベットへの定着不良だ。
その殆どはPID制御の最適化を行っておらずノズルの温度が不安定だと思われる。
また屋内設置でも防風箱が必要な場合などはPIDの設定が不適切なのだろう。
日本語のWeb上にはPrusa i3 MK3を組立てた記事が沢山在るが、
PIDのCalibrationに触れているのは1件だけだった。
殆どはセルフテストをパスしたらFirst layer Calを行い試験印刷へと進んでいる。
PID Calibrationには触れていないのが殆どだ。
しかし
PIDは初層の定着や印刷の美しさに大きく影響する重要な設定値だ。
PIDというのは自動制御の手法の一つだ。自動制御を勉強したことが在れば常識なのだが、
一般の人には馴染みの無い単語だろう。Prusa i3 MK3ではノズルの温度制御に使われている。
ヒーターで発生した熱がサーミスタへ伝わる時間に対応してP値(比例)、I値(積分)、D値(微分)を
設定しなければならない。理屈は難しいが、Prusa i3 MK3には自動校正の機能が在るので簡単だ。
ホットエンドの組立て方や工作精度によって伝熱時間が変わるので
3Dプリンタ1台ごとにPIDの自動校正を行わなければならない。
勿論、ホットエンドを分解したり純銅ヒートブロックへ換えた際にもPIDの自動校正が必要だ。
PID自動校正の方法は
PRUSA
KNOWLE BASEに説明があるので参照して下さい。
英語だがGoogle Chromeの自動翻訳で意味が通じる程度に翻訳してくれる。
PRUSA Resarch社が販売している完成品については、
PID Calibrationを実施してから出荷しているそうだが、
KitやClone prusaでは自分で行わなければならない。
下の図はPID Calibrationを230℃で実施した際の温度変化をOctPrintで記録した。
ステップ応答からPIDの最適値を算出しているようだ。
理科工業のホームページに
PID制御の優しい説明が在る。
PID制御について詳しく知りたい方は一読されると良いでしょう。
45. 大型部品の造形 2021,10,23 実施
新たに円筒形スピーカーの製作に着手した。
円筒の部分の総てをClone Prusaで造形する予定だ。
寸法は最も太い部分の外径が203mm、高さが205mmでPrusaで印刷できる最大寸法に近い。
過去に経験の無い大きさだったので心配だったが問題なく印刷できた。
当初は積層厚を0.2mmでスライスしたところ印刷時間が32時間と算出された。
時間が掛り過ぎるので積層厚を0.3mmにした結果、21時間に短縮された。
0.3mmでは造形物の表面が粗くなるかと心配したが、大型の部品なので積層の荒さは感じてない。
使ったフィラメントは、TINMORRYのPETGだ。選定理由は廉かったからだ。
スライスにはPrusaSlicerを使った。各種の設定は初期値のままだが、
温度の設定は初層が235℃/70℃で以降は230℃/60℃にした。
消費したしたフィラメントの重量は382gだった。
値段が1kgで\2,399-のPETGフィラメントを使ったので材料費は916円の支出だ。
◎他の部品の造形と仮組 2021.11.01 実施
円筒形スピーカーの残りの部分を造形した。
各パイプの高さは我がPrusaで印刷できる限界に近い205mmだが、
重なる部分が5mm在るので5本を継ぎ足すと高さは丁度1mになる。
これは従前の擬似ホーンスピーカーと同じだ。
右下の写真は設計の検証のために5本のパイプを重ねた様子だ。
小さな設計ミスが散見されたが大きな問題は無かった。
全体の形はエクスポーネンシャルホーンなのだが、
拡がりが小さいためストレートホーンの様に見える。
Aliexpressへ発注したインサートナットが届き次第、組立てに着手する予定だ。
頂上に在るオレンジ色の部分はスピーカーマウントで以前に造形した物だ。
従前のスピーカーマウントが、そのまま使えるように設計したのを確認した。
完成したら鳴らして擬似ホーンとエクスポーネンシャルホーンとの差異を検証する予定だ。
印刷に要した時間とフィラメントは下表のようになった。
延べ印刷時間は4日近くで
1kgのスプールを2個近く使った。
1本が\2,399円なので\4,798円の出費だ。
総計4日近くの印刷の間、我がBear Upgrade Prusaはトラブルも無く快調に働いてくれた。
その間に調整等は全く行ってない。行ったのはフィラメント交換とベットの掃除だけだ。
中国製の主要部品買い集めて組立てたCloneのPrusaだが優れたオリジナルの性能を継承している。
◎
組立て開始 2021.11.03
Aliexpressへ発注したインサートナットが届いたので組立てを始めた。
そこで間違いに気づいた。
インサートナットを入れる為の下穴が大きすぎて溶かし代が無かった。
インサートナットは外径が5mmだが、下穴も5mmで設計してしまった。
溶かして挿入できないので2液混合エポキシ接着剤でインサートナットを穴の中に接着した。
上手く接着できたので下の写真の様に組立ててみた。他には設計ミスは無かった。
46. インサート・ナットの組込み 2021,11,13 実施
先日に作った
円筒形スピーカーを試聴したところ非常に良い結果が得られた。
1台の円筒形スピーカーでは、的確な評価は難しいので更に1台を作ってステレオ化する事にした。
前回は分割した円筒を繋ぐのにインサート・ナットを入れる穴の直径を間違えて設計したために
溶かして入れることが出来ずエポキシ接着在でインサート・ナットを固定した。
今回は、その部分の設計を修正して溶かして組み込むのに成功した。
使ったインサート・ナットは
Aliexpressから購入した。50個で435円だった。
下の図でネジ径3mm、太さ5mm、先端部4.25mm、全長5mmのを使った。
下穴は直径4.2mmで設計したが、造形した円筒を測ったら4.0mmだった。
我がPrusaは0.4mmのノズルを使っているので0.2mmの誤差は避けられないのかもしれない。
4.4mmで設計したら良かったのかもしれない。次はそれで試そう。
インサート・ナットの組込みは先端が穴に入らないので先の細いラジオペンチで抑えながら
先の細い
60Wの半田鏝をネジ穴に差込み、溶けたところで押し込んだ。
半田鏝は温度調整機能の無い安価な物だが、先端が細くM3のナットに差し込みやすかった。
ちょっと難しかったのはインサート・ナットを押し込む深さだ、
少し沈み過ぎたのも在ったが、組み立てに支障の無い範囲だ。
下の写真は、5箇所のインサート・ナットを組込みが済んだ処だ。
ところが雄ネジを捻じ込んでみたら傾いているのが在る事が判った。
そこで再加熱しインサート・ナットが熱く周囲のPETG樹脂が柔らかいうちに
雄ネジを捻じ込んで傾きを修正した。
以降は最初にインサート・ナットを押し込んだ際に、インサート・ナットが熱いうちに
雄ネジを捻じ込んで傾きを点検し修正したので二度手間にならずに済んだ。
下の写真はインサート・ナットを使って組立てた円筒形スピーカーだ。
高さは1mで円筒上部は内径100mm、円筒下部は内径200mmだ。
インサート・ナットは3Dプリンターで作った部品を簡単に纏める便利な手段だと判った。
なおインサート・ナットの使い方などは
YouTubeから学んだ。
47. フィラメントの継ぎ接ぎ 2021,12,12 実施
短く残ったフィラメントを繋いで使えれば節約できると考えた。
そこで溶かして繋ぐ治具を買って試したが上手く繋げなかった。詳細は下記です。
円筒形スピーカーの造形では沢山のフィラメントを消費した。
残ったフィラメントの山が下の写真だ。
もうちょっと遣り繰りを上手にすれば良かったと反省している。
スプールに残ったフィラメントの量を推定するには、重さを測るのが簡単だった。
TINMORRYのスプールは空の状態が192gだ。
中途半端に消費したスプールの重量を測り192gを差引いたのがフィラメントの重さだ。
PrusaSlicerでSTLをGコードへ変換すると消費するフィラメントの重量が表示されるので
中途半端に消費したスプールで賄えるか否かが判る。
Aliexpressで
3dプリンター用フィラメント溶接機
という治具を見つけた。
Aliexpressへ注文したところ15日後に到着したので早速試してみた。
原理は右と左の穴からフィラメントを差込み穴の中央部で突き合わせる。
そこにライターの日をかざしてフィラメントを過熱する。
溶けた頃を見計らって左から右へとフィラメントを押し出す。
するとテフロンの穴で絞られて直線のフィラメントが出来る筈だ。
実際にやってみると接合部でダマができて右側のテフロンの穴の引っ掛って通らない。
何度試しても上手く行かなかった。
失敗の原因は、スプールに少し残ったフィラメントは巻き癖が付いており
フィラメント同士の突合せが一線状にならずずれる。
自分が使ったPETGは溶解に適した温度範囲が狭い。
すぐに固まってしまうのでテフロンの穴で成形できない。
PLAならば上手く行くのかもしれない。
最大の原因は作業が下手なことだろう。練習すれば上手く出来るのかもしれない。
48. 白Prusaの点検と整備 2021,12,27 実施
円筒形SP(3Dプリントバックロードホーン)の成型が完了した。
鳴らしたところ過去最良の音が出た。試作は大成功だった。
大きな物の成型が済んだので使用した白Prusa(3Dプリンター)の点検と整備を行っている。
48-1 X軸の異常
症状は無通電の状態でX軸のキャリッジを手で左右に動かすと重くなったり軽くなったりする。
まるでマグネットモーターの軸を手で回した際のCoggingのようだ。
故障部位を探してベルト、プーリ、モーターを目視で調べたが異常は見つからなかった。
そこで部品を一つずつ交換して試した。先ず右側の歯付プーリー、次にX軸駆動モーターを交換したが
症状は消えなかった。最後にGT2タイミングプーリーを黒Prusaから外して交換したら症状は解消した。
原因はモーターの力をベルトへ伝える
GT2タイミングプーリーだった。
上の写真で左が正常品、右が故障品だ。
正常品は一時的に黒Prusa(TriangleLab製のキットに含まれていた)から借用した。
故障品は解体し廃棄した
JGAURARO A3から流用したものだ。
故障品の写真を見ると歯車の山が低いように見える。
3Dプリントバックロードホーンの180時間近い運転で磨り減ったのだろうか。
それとも偏心しやすい構造だったのだろうか?。謎だ。
故障品の要所をノギスで測ったが異常は発見できなかった。
原因が判明したので代替部品をAliExpressへ発注した。
Y軸用も同時に交換するので2個だ。送料を含めて372円だった。
Amazonでも買えるが値段が若干高めだ。
Prusaは、どの部品が故障しても代替部品をAliExpressから入手できる。
しかしSuper PINDAセンサーだけはAliExpressには無いようだ。
48-1-1 GT2タイミングプーリー 交換後も問題解決せず
AliExpressへ注文したGT2タイミングプーリが届いた。
白Prusaへ組み込んで試したが
問題は解消されなかった。
新しいタイミングプーリでも無通電の状態でX軸のキャリッジを
手で左右に動かすと重くなったり軽くなったりする。
従来はタイミングプーリの消耗が原因と考えていたが間違いだった。
新規購入品は従前のタイミングプーリと全く同じだった。
問題はタイミングプーリの設計に在るようだ。
目で見た感じではタイミングプーリの歯の断面が矩形のようだ。
しかしTriangleLab製のキットに使われていたタイミングプーリーの歯は
矩形ではなくインボリュート曲線のように見える。
TriangleLabのKitに使われている部品は良い物を使っているようだ。
Aliexpressで3Dプリンター用と銘打った物を買ったのだがダメだった。
Aliexpressでは商品の詳細が判り難い。
売られているタイミングプーリは皆同じに見える。
TriangleLab製のタイミングプーリーが入手できれば問題は解消する筈だ。
それを求めてAliexpressの中を探した。
しかし20歯は売られていたが16歯は見つからなかった。ちょっと困っている。
したの写真は今回に購入したGT2タイミングプーリーだ。
48-1-2 GT2タイミングプーリー交換二度目で問題解消 2022,03,06実施
前回は商品の詳細寸法を確認せずに注文して失敗した。
Clone Prusaで使え造形もできたが、Coggingの問題は解消しなかった。
そこで再度Aliexpressの商品から良さそうな
GT2タイミングプーリーを探した。
今度は失敗しないように寸法図画が表示されていた品質の良さそうな品を選んだ。
同じ所で16歯と20歯を売っている。
Prusa用は16歯だ。
値段は876円で前回のGT2タイミングプーリーの概ね2.4倍だった。
下の写真は届いた商品の様子だ。X軸とY軸用に2個入り1個を注文したのだが、
一個ずつ小さなZIP袋に収められ更にプラスチック箱に入っていた。
厳重な梱包だ。これにメーカーの広告紙が添付されていた。
それらがポリエチレンのプチプチが内張りされた袋に入って送られてきた。
これをClone PrusaのX軸へ取り付けたところ
Coggingの問題は解消した。
Triangle Labから購入したKitに使われていたGT2タイミングプーリーと較べたところ
全く同じだった。
添付されていた広告紙はAliExpress内の
Mellow
Storeの物だった。
知らなかったので調べたところ3Dプリンター用の高級な部品を扱っているようだ。
TriangleLabのようなClone PrusaのKitは商ってないようだが部品の品揃えは豊富だ。
48-2 Y軸の異常 2021,12,30 実施
X軸のGT2タイミングプーリーを交換後、確認の為にWizardを実施した。
その結果、下の写真のようなY軸の異常を示すメッセージが表示された。
メッセージはY軸のベルトを駆動するGT2タイミングプーリーが緩んでいると指摘している。
そこでプーリーを締めているイモネジを増し締めして再度Wizardを行ったが、状態は変わらなかった。
ベルトが磨り減っても同じ状況になる筈と考え、Yベルトを外して点検した。
その結果が下の写真だ。中央付近の山が変形している。
ベルトは手持ちが在ったので交換しWizardを行ったところ正常にPassした。
Y軸異常の原因はベルトの磨耗だった。
部品を買い集めて白いClone Prusaを組立ててから300時間程度は運転したと推定している。
このベルトはAmazonで購入したものだ。2GT-6との表記が在る。
ゴムの中にナイロンのような繊維が織り込まれている。
TriangleLabから買ったキットに使われているベルトはガラス繊維のようだ。
ガラス繊維よりもナイロンの方が軟らかいので動作音が静かで気に入っている。
白Prusaの運転音はファンの音が主で無音に近い。
部屋のドアを閉めれば外部からは聞こえない程に静かだ。
48-3 X軸ベルトのトラブル
GT2タイミングプーリーを交換した後のWizardではX軸に異常は検出されなかった。
しかしY軸のベルトに消耗が見られたので念のためにX軸のベルトを目視で調べた。
驚いた事にベルトが伸びてピッチが狂っている所が見つかった。
伸びた原因には心当たりが在った。先のGT2タイミングプーリーと歯付プーリーを
交換してCoggingの原因を探った後に、元へ戻す作業で電動ドライバーを使った。
これは買ったばかりで操作に不慣れだった為にベルトの張力を調節するビスを強く
締めすぎたと思われる。伸びたベルトは手持ちと交換し修理は完了した。
上の写真は使用したVESSEL製の電動ドライバーだ。
ベルトを交換する際にエクストルーダーを分解したが、ビスを回す作業がL型レンチとは
比較にならないほど能率的だった。使い方を誤らなければ大変に便利な道具だ。
49. 黒Prusaの点検と整備 2022,01,13 実施
黒のPrusaはTriangleLabのキットを組立てた物だ。
白のPrusaを整備したので、この機会に黒のPrusaも整備することにした。
49-1 ベルトの交換
白のPrusaに使っているベルトは柔らかく騒音が小さい。
それに比べて黒のPrusaに使われているTriangleLab純正?の
ベルトは硬く手でベッドを動かすとウヲーンと重く唸るような音が出る。
硬いので耐久性に優れると思われるが、自分には騒音が少ない方が嬉しい。
そこでTriangleLab純正?のベルトを白Prusaと同じ軟らかい物へ交換した。
その結果、軽い感じの音に変わった。
黒Prusaから外したベルトを目視で点検したが磨耗や変形は微塵も無かった。
下の写真で上がTriangleLab純正?、下がAmazonから買った2GT-6だ。
ベルトが軟らかいと造形の精度低下が懸念されるが、
円筒形SP(3Dプリントバックロードホーン)の成型は軟らかいベルトを使った白Prusaで行った。
造形精度の低下は感じられなかった。但しベルトの消耗は早いようなので定期的な点検は必須だ。
ベルトの交換によって黒Prusaはベルトの駆動音が殆ど聞こえなくなり静かな機械になった。
ところが従前は感じなかった減速ギヤ付きE軸モーターのギヤが嚙みあう音が煩く気になるようになった。
ベルトの駆動音が下がったので相対的に目立つようになったのだろう。
特に初層の印刷で塗り潰す際が煩い。我慢できる範囲だが不快だ。
軟らかいベルトの騒音低減は歯付タイミングプーリーと併用する事で効果的になったと思われる。
この記事を見てベルトの交換を試す方はタイミングプーリーを歯付へ換えると良いと思う。
49-2 代替PEIシートの貼替え 2022,01,17 実施
造形鋼板に貼っている
代替PEIシートが痛んだので貼替えた。
造形鋼板は白Prusaと黒Prusaで同じ物を使い回している。
円筒形SP(3Dプリントバックロードホーン)や他の小さな物の成型に使った。
代替PEIシート(防災凸凹ガラス用シート)にはスティック糊を併用している。
低コストなので重宝しているが若干の問題がある。
造形物を剥がす際にシートが造形鋼板から少し浮き上がる。
何度も同じ場所で造形すると浮き上がった部分に気泡ができてしまう。
そのため気泡の部分で造形すると造形物の底が平らにならずに凹む。
下の写真の中央部が、それだ。
3Dプリントバックロードホーンの造形で大きな物を22回以上印刷できた。
丸い同心円のような白い円はホーンを造形した痕跡だ。
同心円上の部分は細かな気泡が在るだけなので造形に支障は無い。
中央部が、ガサガサに荒れてしまったので使えなくなった。
下の写真はシートを貼り替え初層校正を実施した際の写真だ。
上の写真ではスティック糊を使ってないが良く定着している。
造形の際にはダイソー製かセリア製のスティック糊を使っている。
ダイソー製のほうが浮き上がりが少ないような気がするが確証は無い。
49-3 Firmwareの更新 2022,01,19 実施
久々に
PRUSA
RESEARCH社のダウンロードサイトを覗いたら
自分が使っているFirmwareよりも新しいものがUpされていた。
従前は3.9.1で最新版は3.10.1-4697だ。早速インストールした。
パソコンとプリンターの間をUSBケーブルで繋ぎ、PrusaSlicerを使って書き込んだ。
何故PrusaSlicerにFirmware書き換え機能が在るのか一寸不思議だ。
たぶん発展過程の名残なのだろう。
PrusaSlicerを起動し、画面上段メニューの”構成”をマウスポインターで指すと
プルダウンメニューが現れるので、その最下部の”Firmwareをプリンタに書き込む(f)を
クリックするとファームウエア更新窓が現れる。
ファームウエア更新窓のファームウエアイメージ枠が空白になっているので
そこにダウンロードしたファームウエアの所在を書込み、
書込みボタンをクリックすれば書込みが始まり、下の図の様に更新完了になる。
無事に書き換えが済んだ。動かしてみたが変わった部位は判らなかった。
たぶん細かな改良が行われたのだろう。
このような継続的な改良がPrusaの使いやすさに繋がっているのだと思う。
49-4 Z軸上部支持部の更新 2022,01,19 実施
久々に
gregsaun /prusa_i3_bear_upgrade
を覗いたらZ軸上部支持部が改良されていた。
Original PrusaのFirmwareを組み込むとWizardをPassできない問題が解決されたのかと期待した。
自分が使っているBear upgrade PrusaはZ軸が約3mmほど短いために自己診断が不合格になる。
自分がTriangleLabからKitを買ったのは3年近く前なので現在販売されている
モデルは改良されているのだろうか?。判らない。
早速Z軸上部支持部をダウンロードして成型し組み込んでみたが、問題は解決されなかった。
たぶん従前の支持部は強度が充分ではなさそうだったので改良したのだろう。
下の写真は成型したZ軸上部支持部だ。申し分ない出来栄えだが、残念。
仕方なくダウンロードしたZ軸上部支持部のSTLファイルを改造した。
滑り棒を収める部分を3mmだけ底上げし、丸い枠の部分を3mmだけ高くした。
黒いメネジに当たりそうな部分を丸く削った。
また改造したZ軸上部支持部と調和させるべく頂上のカバーも改造した。
このファイルをThingverseへ掲示した。
https://www.thingiverse.com/thing:5233051
造形し取り付けたのが下の写真だ。オリジナルとの違いは僅かで3mmだけ高い。
従前の物よりもガッチリしていて良い感じだ。
新しく組み込んだZ軸上部支持部を付けてWizardを実行した結果、無事に合格した。
これでOriginal Prusaとの互換性が完全になったので最新Firmwareが使える。
50. PrusaSlicer 2.4.0 導入失敗 2022,02,11 実施
PRUSA RESEARCH社のホームページに
PrusaSlicerの最新版2.4.0が挙げられていた。
早速ダウンロードしインストールした。
Doenload ホルダーに出来た
PrusaSlicer_Win_ standalone_2.4.0をクリックし問題なくインストールできた。
ところが起動したらエラー表示の窓が現れ
問題が発生したので停止との表示が出た。
そのエラー表示窓を右上のXで消したらPrusaSlicer 2.4.0は起動せず終了した。
設定などを変えて何度も試したが、結果は同じだった。
仕方なくPrusaSlicer 2.4.0をアンインストールした。
Doenload ホルダーに在る前出の
PrusaSlicer_Win_ standalone_2.4.0を起動するとメニューの窓が表示される。
そこにアンインストールも在るので、それをクリックしたら綺麗に消えた。
PrusaSlicer_Win_ standalone_2.4.0は消えなかったので何度も試せた。
自分が主力で使っているパソコンは今もWindows7だ。過去にWindows10に移行させたが
動かない古いソフトが複数あり、Windows7へ戻した物だ。
その際にディレクトリーが完全に戻らず騙し騙し使っている。何か問題が在りそうだ。
PrusaSlicer2.4.0をインストールした際に従前のPrusaSlicerは消されてしまった。
PrusaSlicerが無ければ甚だ不便なので旧版を探したところ
Prusa
Knowledge Baseに
Older wersionsの赤い文字があった。下図中央の最下部だ。
これをクリックすると
Drivers Apps 2.3.3が表示される。
その行の右端に赤い文字でDownload for Windows(442MB)が表示されている。
これが
PrusaSlicer 2.3.3のダウンロードスイッチだ。
これでダウンロードを試みたが何故か何回も失敗した。混んでいるようだ。
粘り強く頑張ったところ5回目でダウンロードに成功した。
これをインストールしたところ問題なく使えた。
しかも従前の版と見掛けは同じだが小さなバグが改善されていた。
しかも従前の設定も消されず継承されていた。
試しにWindows10で動いているパソコンへPrusaSlicer 2.4.0をインストールしてみたが問題無く動いた。
またWindows11で動いているCore i5 SSD1Tのラップトップパソコンでも大丈夫だった。
やはり自分が設計に使っているWindows7のシステムに問題がありそうだ。
この記事を書いている間にPrusaSlicerの最新版PrusaSlicer2.4.1が発表されたようだ。
問題は解消されたのかも知れないが。試す気にはならない。
51. OctPrint用カメラにLED照明を取付け 2022,02,24 実施
Bear Upgrade PrusaにOctPrintを組み込み重宝している、
女房が室内での造形は微粒子を飛散させると懸念して嫌がるのでベランダで運転している。
ベランダで運転しても火燵からOctPrintに取り付けたTVカメラを経由して造形の様子が見えるので安心だ。
ところが大きな物を造形すると長時間を要するために運転が夜間まで及ぶ事も屡々だった。
その場合には真っ暗な為にTVカメラで運転の様子をチェックできず甚だ不便だった。
そこで
LED照明を追加することにした。
問題はLEDの電源を何処から取るかだった。
TVカメラの基板を顕微鏡とテスターで調べた所、+5VとGNDの配線パターンを特定できた。
下の写真で
左端の黒矢印がGND,右
端の赤矢印が+5Vだった。
そこへ電線を半田付けして引っ張り出し、100Ωの抵抗を通じて白色LEDに繋げた。
電流は18mA程度なのでPrusaの電源への負担は少ない筈だ。
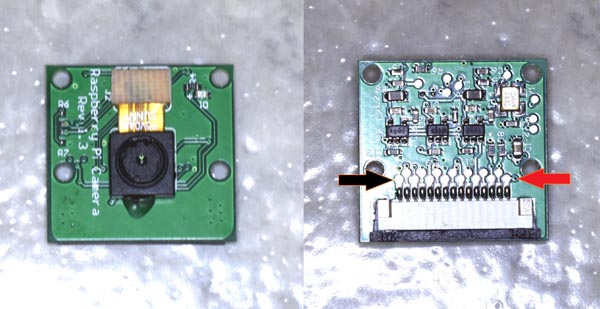
注:このカメラはRaspberry Pi純正ではなく、Aliexpressから400円程度で買った互換品だ。
カメラの基板用に小さな箱を設計し造形して収めた。
小箱の上には照明用LEDを収納する円筒を取り付けた。
下の写真で黒く小さな箱がカメラで、その上の白く光っている小さな丸がLEDだ。。
カメラを支えるカメラマウントも作った。
タイムラプスの様な動画を撮影するのが目的では無いので必要最小限の単純な形に纏めた。
下の写真でモーターに取り付けた赤い横棒がそれだ。
カメラの小箱を挟んで支持しているのでカメラを上下方向に回せる。
可動部は、そこだけだ。
カメラから出ている細長いリボンは電線だ。
左奥に写っているラズベリーパイ・ゼロWとカメラを結んでいる。
長さは30cmでギリギリの長さだが、Z軸が上限まで上がっても引きつる事は無かった。
もう10cm程度長いリボン電線を探したが見つからなかった。
下の写真は夜間に運転中のOctPrintのTV画像だ。充分に明るいとは言い難いが、
成型物の剥がれや倒れが無いのを確認できる。製作目的は達せられた。
下の図は造形物をPrusaSlicerでGコードへ変換した際の表示だ。
これを造形する際の様子をTVカメラで撮影すると上の写真のようになった。
52. GT2ベルト用張力計の製作 2022,03,10 実施
タイミングベルトの張り具合を客観的に把握する方法をWebで探したところ、
PRUSAMENTの中に
GT2ベルト用張力計が在るのを見つけた。
驚いた事に3Dプリンターで張力計を造形しているのだ。
半信半疑だったが面白そうだったので早速ダウンロードした。
ダウンロードしたのだが何故かSTLファイルではなくGCODEファイルだった。
これを印刷しようとしたらヘッドの温度が250℃、印刷台が90℃にセットされたので
慌てて止めた。フィラメントがPETGなので250℃は高すぎる。
しかし自分でスライスしたファイルではないので簡単に温度を変えられない。
仕方なくGCODEファイルをテキストエディターで開き、
250℃を235℃に、90℃を70℃へ編集して下の写真の様に造形に成功した。
若干糸引きが多かったがニッパーで綺麗に切り取って完成した。
造形は済んだが、性能は半信半疑だった。
そこで
テンションスプリングで張力を保っているY軸のベルトを測って試した。
驚いた事に指針が適正張力範囲の中央付近を示した。信用できそうな結果だ。
下の写真でタイミングベルトに巻きついている針金がテンションスプリングだ。
次にX軸を計って見たところ下の写真の様に適正張力範囲の上限だった。
そこで張力調整ネジを緩めて適正張力範囲の中央に合せた。
精度は不明だが、相対的な張力が把握できるのは便利だ。
徒手空拳よりは遥かに役立つ道具だ。それにしても素晴らしい設計技術だ。
STLファイルを供給しないのは、印刷条件の違いによる誤差の増大を回避する為だろう。
検出部は積層厚0.1mmで高さ3mm以上は厚さを増し高速で印刷している。
充填率も変えているのかもしれない。
通常のスライサーでは、そのような設定は出来ないからだろう。
従来からタイミングベルトの張力を把握する方法としては、
ベルトを指先で弾いた際に出る音の周波数をスマホのアプリで測る方法が知られている。
自分も古いiPhoneに
Sonic Tools
SVMというアプリをインストールして測ってみた。
その結果、X軸もY軸も96Hzだった。Prusaの場合には83Hzと言われているので
若干高かった。しかしベルトの振動周波数はベルトの強度や重さによって変わる筈だ。
我がClone Prusaのように軟らかいベルトを使った場合には少し軽いので違う周波数に
なるのは当然だろう。
53. 運転騒音の低減 2022,04,01 実施
我が家ではTriangleLab製のKitを組立てた黒いBear upgrade Prusaと、
部品を買い集めて組立てた白いBear upgrade Prusaの2台を使っている。
騒音問題は黒Prusaで発生した。いつもの様にベランダへ持ち出し運転したのだが、
運転が深夜に及ぶと周囲が静かになり唸るような重低音が聞こえる。
煩いというような音量では無く、小さな音だが気になる音だった。
妻から近所迷惑との指摘があり、直ちに成形を中断した。
2時間も運転した後だったのでフィラメントが無駄になった。
白Prusaは何度も深夜に運転したが騒音の問題は起こらなかった。
白Prusaはとても静かだ。無音ではないが脇で寝られるくらいだ。
黒Prusaと白Prusの違いを調べれば黒Prusaの騒音問題を解消できる筈と考えた。
Aliexpressから購入した部品は殆ど同じだったので、
違いは黒Prusaで成形した白Prusの部品に在る筈だ。
成形データはGithubからダウンロードした最新のSTLファイルを用いた。
53-1 Y軸駆動モーター用マウントの更新 22,04,01 実施
大きな騒音は常時発生しているのではなくY軸駆動モーターとX軸駆動モーターが
同時に動く斜め方向への移動の場合が顕著だった。
時計の文字盤に例えると2時、5時、7時、10時の辺りを描く場合だ。
X軸駆動モーターとY軸駆動モーターが作る振動がアルミ製のフレームを伝わり
協合して重低音を生み出すようだ。
そこでY軸駆動モーターのマウント部を黒Prusaと
Githubからダウンロードした
ファイルを見比べてみたところ新型は頑丈そうに改良されていた。
下の写真で左の白色が改良されたマウントで赤色が旧型だ。
赤色は全体的に薄く華奢に見える。
早速成形して取り付けたところ騒音は大幅に低下していた。
唸るような重低音は消えたが、他の騒音が残っており静かさは白Prusaには及ばない。
下の写真は騒音性能評価の為に成形したM3ナット用ドライバー(M3ボックス)だ。
印刷の品質は従前と変わらず精緻だ。
53-2 Z軸駆動モーター用マウントの更新 22,04,08 実施
Y軸駆動モーターのマウントを最新の設計の物に作り変えたら騒音低減効果が在った。
運転の騒音はX軸駆動モーターとY軸駆動モーターが作る振動がアルミ製のフレームを伝わり
協合して重低音を生み出すようだ。X軸駆動モーターは直接にアルミフレームには接触していない。
故にX軸駆動モーターの振動はZ軸駆動モーターを経由してアルミフレームへ伝わっていると思われる。
そこでZ軸駆動モーター用のマウントも設計が更新されているのではと考えた。
黒PrusaのZ軸駆動モーター用のマウントと
Githubからダウンロードしたファイルを較べたところ
此方も強度を高めるように改良されていて全体に厚くなっていた。
また
Original Prusa i3とのFirmwareの互換性を図ったらしく下の部分が3mm延長されていた。
早速ダウンロードして造形したのが下の写真だ。
造形したZ軸駆動モーター用のマウントを組み込んだ黒Prusaをベランダへ持ち出し
ダンボール製防風囲いの中で騒音性能を評価した。造形したのは妻から頼まれた箸立だ。
その結果、騒音は更に低下していた。造形は5時間に及んだが、妻は全く聞こえないと言っていた。
自分は僅かに聞こえたような気がしたが、近隣に迷惑を掛ける心配は無さそうな水準だ。
騒音問題は解消したが、静かさは白Prusaに及ばない。
時折ベアリングのボールが転がるようなゴロゴロという感じの音がする。
ポリマーベアリングに替えたら消えるかもしれない。
53-3 Z軸駆動モーター用軸キャップの更新 22,04,12 実施
先に行ったZ軸駆動モーター用マウントの更新作業で軸への埃の進入を防ぐ為に
取り付けられていたキャップを持ち上げたままで下げるのを忘れていた。
気づいた時点で下げようとしたがマウントの丸い開口部が狭く入らなかった。
調べた所これも更新されており小さくなっていた。
つまり
Z軸駆動モーターのマウントを更新する際にはキャップも更新しなくてはダメだった。
早速
Githubからダウンロードして造形したキャップをBear
upgrade Prusaに組み込んだ。
軸キャップを交換してから下の写真のような物を造形した。
左の四つは単3乾電池を単2用の機器に使う為のアダプターだ。
Thingiverseの
AA
to C Battery Adapter Remixを使わせて頂いた。
素晴らしい設計技術で感服した。自分の3D-CADを扱う技術では不可能だろう。
右の三つはPrusaのY軸を支えるスライドベアリングを固定する
Y軸ベアリングホルダーだ。
近々ベアリングを固体ポリマーベアリングへ替えようとしている。
その為に必要な部品を集めている。買わなければならないのはM3の25mmビスだ。
53-4 Y軸用リニヤベアリングを固体ポリマーに変更 22,04,16 実施
Aliexpressへ発注した固体ポリマーベアリングが郵便受けに届いた。
下の写真のような簡単な梱包だった。
黄色い袋の内側にはポリエチレンのプチプチが裏打ちしてあった。
金額は5個で送料を含めて\455-だった。色の暗いのは以前に買った無印だ。
以前に買ったdrylinと同じ物だと思って注文した。 色と型番は従前と同じだがdrylinの刻印が無い。
それに内面の溝が多い。モデルチェンジしたのか海賊版なのか判らない。
今まで使っていた金属製のベアリングはステンレスのUボルトを使って固定していた。
Githubには
Y軸用ベアリングホルダーが在ったのでダウンロードして造形した。
設計が素晴らしくパチと音を立てて嵌り固定された。
下の写真のようにポリマーベアリングが嵌ったベアリングホルダーを組み込んだ。
ビスはM3の25mmでナイロンナットはUボルトに使っていた物を再利用した。
組込み後に造形台を前後に手で滑らせてみたら従前に比べて抵抗が大きいかった。
滑り棒にスプレーグリースを塗布したら少し軽くなったが金属ベアリングに比べれば重い感じだ。
それでも電源を入れてY軸を動かしてみたら問題無く動いた。
その後Wizardを実行したところ、Y軸から時折出るベアリングのボールが転がるような
ゴロゴロという感じの音は完全に消えた。凄く静かな機械になった。
騒音の原因はベアリングだった。
試運転はThingverseに在る3dbenchyで行った。
5年前に買い備蓄していたPLAフィラメントを使った為に?糸引きが多かった。
このところPETGしか使わないので、PLAの最適印刷条件を忘れてしまったのも原因だ。
しかし寸法精度は正確で船尾に在る冷却水の出口穴も綺麗に造形されていた。
しかし船尾に在る船名の文字は不鮮明だった。
原因は造形台の滑りが重く、テンションスプリングが伸びて位置決めが甘くなるようだ。
暫く運転すればポリマーベアリングが磨耗して動きが軽くなると考えている。
自分が使っているデジカメは諧調が狭く白い物を撮ると潰れてしまう。
そこで影が出来るように光を一方向から当てて撮影した。
その為に凹凸が強調され印刷が荒いように見えるが、肉眼では綺麗に印刷されている。
写真は難しい。
Y軸からの騒音が消えたらX軸のベアリングとフィラメント送り出しモーターの
減速ギヤの音が気になるようになった。
54 片持ちスプールスタンドの製作 2022,04,26 実施
Bear upgrade prusaにはスプールスタンドが無いので片持ちのスプールスタンドを製作した。
従来はスプールを通すシャフトを両端で支える
物干し竿のようなスプールスタンドを自作し使っていた。
その両持ちのスプールスタンドで問題なく造形出来たのだが、
フィラメントを交換する際に両手を使わねばならず作業性が良くなかった。
片持ちのスプールスタンドは片手で操作できて具合が良い。下の写真は使用中の様子だ。
当初は脚部を下の写真のようにトラス構造で作った。
ところが新品に近いフィラメントのスプールを掛けて置くと重みの為に徐々に横方向へ歪んでしまう。
トラス構造が強度を発揮する後ろ方向は問題ないのだが、横方向に傾いていて格好が悪い。
三次元トラス構造に出来れば横方向も強くなり問題は解決できると思われたが、
3D-CADで三次元トラス構造を設計する技術力が無い。
そこで手っ取り早く脚部を幅25mm、奥行き38mmと太くし、更に鉄の板で補強した。
鉄板は長さ150mm、幅20mm、厚さ2mmの穴が沢山開いた市販品だ。
従前の両持ちスタンドで支柱に使っていたものを再利用した。
Prusaで造形した部分はPETGで表皮が3層、内部充填率は30%にした。
スプールの軸はM8の全ネジ棒を使った。長さは120mmだ。
全ネジ棒の軸にパイプを被せた。パイプの外径は30mmにした。
パイプはクルクルと回るので造形の際にフィラメント送りギヤに掛る負担が減る筈だ。
パイプの両端にはスプールの脱線を防ぐ目的で高さ5mmの鍔を設けた。
パイプを固定するのはM8のナイロンナットだ。これで造形中に緩む可能性は少ない筈だ。
完成したスプールスタンドに八割程フィラメントが残ったスプールを掛けたまま
一ヶ月ほど放置したが、脚が歪む気配は全く無い。製作は成功したと思われる。
55 USB充電ケーブル用標識の製作 2022,05,06 製作
下の写真のようなUSB充電ケーブル用標識を設計し3Dプリンターで造形した。
このところ身の回りにUSBで充電する機器が増えたきた。USB充電なので充電器が付属しない機器が多い。
従前のように夫々に専用充電器が付属していると何用の充電器か判らなくなったり迷子になったりする。
USB充電では充電器が共通だしパソコンでも賄えるので専用充電器を保管する必要が無い。当然迷子にもならない。
しかしUSB充電の機器でも専用のUSB用充電ケーブルが付属してくる。
充電器のコネクターに刺す側はUSB Type-A形で共通だが、
機器側は多彩でUSB 2.0 Micro-B、USB 2.0 Mini-B、USB 2.0 Type-C、USB 3.0 Type-C等が在る。
現時点では統一されていない。何れはUSB 2.0 Type-Cに統一されるものと期待している。
つまりUSB用充電ケーブルの使い回しはできないのだ。しかも各充電ケーブルの外観は似ていて識別しずらい。
その上に我が家ではArduinoやRaspberry Piに使うUSBケーブルが沢山在るので埋没しやすい。
そこで簡単に識別できるようにUSB充電ケーブル用標識を作った。
設計は下図の様にした。長方形の平坦な部分は幅30mm、高さ8mm、厚さ1.2mmだ。
直径3.0mmのケーブルに嵌る部分の穴の内径は3.4mmで設計した。
切り欠きの部分は円の中心から90度で設計した。ケーブルに嵌る部分の肉厚は3.4mmだ。
試用したフィラメントはPETGだ。表皮3層、内部充填は20%で造形した。
電線に嵌めてみるとカッチリと止まり外れる事は無かった。
取付けてから一週間程経過したが緩まなかった。
殆どのUSB充電ケーブルは外径3mmだが、電動ドライバーは4.5mmだったので4.5mm用も作った。
中心の穴を5mmに拡げただけで他の寸法は3mm用と一緒だ。
文字の部分はラベルプリンターで印字し貼り付けた。
この記事を
Thingiverseへ掲示しました。
56 ヒートブロック用シリコンカバーの交換 2022,05,27 実施
自分のBear upgrade prusaのヒートブロックにはシリコンゴムで成形されたカバーを取付けてある。
英語ではSilicon socksと呼ぶらしいが靴下では解り難いのでシリコンカバーと書いた。
目的はノズルに冷却風が当たる面積を小さくして温度制御を安定化させる為と
フィラメントの糸引きでヒートブロックが汚れるのを防ぐ事、そして若干の節電だ。
過日、ヒートブロックの掃除をする際に雑に扱ってシリコンゴムカバーを裂いてしまった。
シリコンゴムは200℃迄は連続使用に耐えるそうだが、
自分はPETGしか使わずヒートブロックは235℃に設定している。
裂け方を見ると235℃での使用で劣化したのかもしれない。
これは2年前に
TriangleLabから買ったのだが、その当時は類似品が僅かで選択肢が少なかった。
そこで代替品をAliexpressへ発注した。それが届いたので取付けたのが下の写真だ。
取付けの為に冷却風のノズルは外してある。
LED照明の下でストロボを使わずに撮影したのだが、何故か実物よりも青く写っている。写真は難しい。
実物は上の写真の色と同じだ。
現在では沢山の種類が販売されており代替品を選ぶのに迷うほどだ。
試しに
以前とは違うものを買ってみた。価格は3個で\823-円だった。
従前のはヒーターを締め付けるビスの頭の部分が丸穴になっていたが、
今度のは半円形に膨らんで覆われていた。僅かだが断熱効果が高い筈だ。
届いた製品を見ると成形が雑でバリが沢山あった。
TriangLab製の精緻な成形とは違ったが廉いのは魅力だ。
それらのバリをニッパーで切り取りヒートブロックへ取り付けたところ、
従前よりもヒートブロックへしっかりと着いた。
嚙み込む爪が長いのか厚いのか判らないが良い感じだ。
正面の厚みを測ったところ従前が1.47mmで今度のは1.59mmで僅かに厚かった。
シリコンゴムカバーを取付けた後にPID tuningを実施し、その後にテストピースを造形してみた。
危惧していた半円形の膨らみが造形物に擦れることも無く正常に造形できた。
Aliexpressには他にも同じ商品を売っている店がある。宣伝の写真では差異が解らない。
若しかすると少し高い商品を買ってしまったのかもしれない。
57. PrusaSlicer 2.4.2 導入成功 2022,06,05 実施
自分が工作の設計やプログラム開発には、現在もWindows-7を使っている。
理由は10では動かない値の張るソフトがあったからだ。
今年の2月に
Win-7のパソコンへPrusaSlicer
2.4.0を導入しようとして失敗した。
当時もWin-10では問題なく動いたので、Bugが在ったのだろう。
直後にPrusaSlicer 2.4.1が出されたが導入せずに落ち着くまで待った。
昨日、
PrusaSlicerのサイトを除いたらPrusaSlicer
2.4.2が出ていた。
2.4.0発表から4ヶ月も過ぎBug解消されただろうと推測し早速ダウンロードし導入した。
導入は自動的に旧版を消し新版を書き込んでくれた。
起動直後に構成ウィザードが表示されたので下にあった
終了ボタンを押したところ
自分が工夫した設定や特別Gコードも特に操作せずに継承された。
自分は試さなかったが、左下にある
すべての標準プリンターを選択を選べばデフォルト値が設定されるのだろう。
PrusaSlicer 2.4.2で追加された機能に底面位置の変更が在る。
STLファイルを読み込んでからFキーを押すと下図左のように要所に白い場所が現れる。
その白い部分をクリックすると、その部分が底面になるように回してくれる。
下図右は煙突の上端の白い部分をクリックした結果だ。
自分の設計では必要ないが、Thingiverseから戴いたSTLでは底面が印刷しにくい場合がある。
そのような場合には便利だと思う。
早速PrusaSlicer 2.4.2で付属してきた3dbenchyをPLAで造形してみた。
下図右は220℃で造形した。温度が高過ぎた為に糸引きが多い。
下図左は180℃での造形だ。糸引きは激減している。
しかし問題が在る。船の手擦りが荒れてガサガサだ。
温度が不適切なのかPrusaSlicer 2.4.2のBugか判らない。
57-1 PrusaSlicer 2.4.2で3dbenchyの手擦りが荒れる原因の追究 2022,06,10
実施
PrusaSlicer 2.4.2で3dbenchyを造形すると手擦りが荒れてガサガサになる。
問題を探るために条件を変えて何度も造形してみた。
自分が3D-CADを動かしているWin-7ではなく、Win-11で動いているラップトップに
PrusaSlicer 2.4.2を導入し、Gコードを作って造形したところ手擦りは荒れなかった。
よってWin-7側の設定に問題が在りそうだった。
詳細に調べた所、PrusaSlicer 2.4.2のプリンターの機種を設定する窓の内容が違っていた。
Win-7ではプリンターの機種が
Original Prusa i3 MK3となっていた。これはPrusaSlicer
2.3から継承した設定だ。
ところがWin-11では
Original Prusa i3 MK3S & MKS3+と登録してあった。自分が登録したのだが。
そこでWin-7のPrusaSlicer 2.4.2も
Original Prusa i3 MK3S & MKS3+に変更して造形したところ
手擦りのガサガサは解消した。糸引きも無く綺麗な申し分の無い3dbenchyが造形された。
自分は
Prusa i3 MK3と
Prusa i3 MK3Sは同じ設定で良いだろうと考えていたのだが、
細かい処で違いがあるようだ。
問題を追及する過程で、古いPLAフィラメントを使ったのだが造形中に3度も折れた。
4年前に買った物だが湿気を吸って脆くなったのか経年劣化なのか判らない。
フィラメントが折れる度にClone Prusaがブザーで知らせてくれた。
折れたフィラメントを抜き、残りのフィラメントを差し込むと造形を再開してくれたので実害はなかった。
フィラメント折れのリカバー機能を備えているPrusaは凄い。
下の写真で一番前にあるのが、手擦りガサガサ問題を解決した造形物だ。
57-2 ファジースキンの試用
2022,06,11 実施
PrusaSlicer 2.4.2では新たにファジースキンという機能が追加された。
造形物の表面を修飾する機能のようだが、良く判らなかった。
そこでPrusaSlicer 2.4.2に読み込まれていた3dbenchyを使って試してみた。
その結果が下の写真だ。
ファジースキンは造形物の表面に布目様の凹凸をつける機能だった。
凹凸の高さやピッチは指定しなかったのでデフォルトだ。
外壁に施すか全体を施すかの設定ができるが、内壁の設定はできない。
自分はスピーカーの工作に3Dプリンターを使っている。
壁面に凹凸を付けると壁面での反射が減り音が良くなる可能性が在る。
内壁にファジースキンを施してみたいのだが出来ず残念だ。
58. 造形台用バネ鋼板の更新 2022,06,15 実施
自分のPrusaでは、PEIシートとテクスチャーの2種のバネ鋼板を使い分けている。
2年に及ぶ運用で何れのバネ鋼板にも表面に傷を付けてしまった。
傷を付けた主な原因は操作の間違いや誤動作だ。Prusaの導入時に理解不足だったのが主因だ。
仕方なくスライサーでGコードへ変換する際に、傷が在る位置を避けて造形しているのだが、
時々忘れて傷の上に造形してしまう。そこでバネ鋼板を刷新した。
新しいバネ鋼板はAliexpressの
ENERGTIC 3D Storeから
購入した。
片面がPEIシートで反対側がテクスチャーになっている。
価格は送料を含めて\2,647円だった。今日調べたら為替の変動で値上がりしていた。
発注から2週間程で届いた。ダンボールに挟まれたバネ鋼板がプチプチの袋に入っていた。
プチプチの袋の大きさはPrusa用バネ鋼板に合わせたピッタリの寸法だった。
大量に製造販売しているのが窺がえる。
ダンボールを開くとバネ鋼板の角を保護するプラスチックが嵌められていた。丁寧な梱包だ。
下左はPEIのシートが貼ってある面で微小の気泡が見られるが実害は無い程度だ。
下右はテクスチャーの面で初層校正を実施した後だ。
Live Zの値は従前よりも0.025mm深いー0.8mmだった。PETGで綺麗に線が引かれている。
従前のバネ鋼板は黒だったが、今度のは琥珀色だ。豪華な雰囲気で気に入っている。
実物を手に取ると従前のバネ鋼板よりも重い感じがしたので厚さを計って見た。
従前は塗膜も含めて0.7mmだったが、今度のは0.99mmだった。
その違いの機能的な影響は判らないが、撓めるのに腕力が必要だ。
試しに
Printablesに在るwhistleをダウンロードし造形してみた。
造形物が剥がしやすいように予めテクスチャーの面にスティック糊を塗布してから造形した。
結果は下の写真の様に綺麗に仕上がった。新しいバネ鋼板は問題の無い良い商品だった。
バネ鋼板の問題ではないのだが、印刷完了時の糸引きは解決できてない。
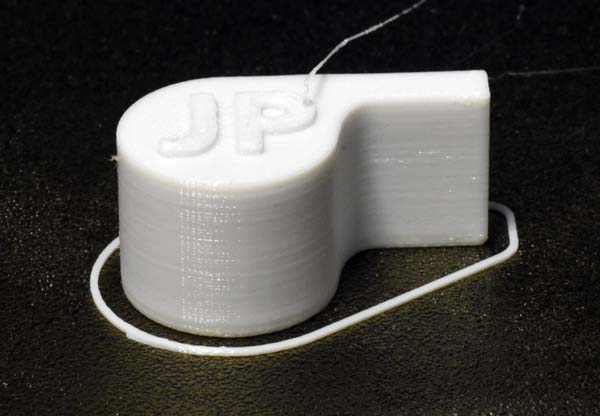
フィラメントはPETGで積層厚0.15mm、内部充填は15%で実施した。
59. ノズル温度の精度測定 2022,06,18 実施
Prusaを始め多くの3Dプリンターでは、ノズルの温度を測るセンサーにサーミスタが使われている。
サーミスタは低コストなので民生機器では多用されるが、特性にバラツキが在るセンサーだ。
以前から測定精度の高いセンサーでClone Prusaのノズルの温度を測りたいと思っていたが、
ノズルの中まで差し込める細く精度の良いセンサーが入手できず測定できなかった。
数日前にオークションを眺めていたら直径1.6mmの細い熱電対が捨値で出品されていた。
他に入札者も居なかったので廉く落札できた。何と\1,200円だった。
その熱電対をフィラメントの入口からノズルの内部まで差込み温度を測ったところ、
235℃の設定に於いて10℃ほど高い温度に制御していた。
誤差が大きいようだが+5%程度なので不良品ではない。下の写真は測定の様子だ。
59-1 使用機器
購入した
熱電対は
J型 Class2 だった。JISの許容誤差は333℃以上 750℃未満の範囲に於いて0.75%だ。
235℃では規定されていないが、仮に1%でも2.35℃の誤差だ。
熱電対の起電力を受けるのに
ディジタルテスターを使った。このテスターにはK型熱電対を接続し
直接的に温度を表示する機能があるが、J型熱電対では、その機能が使えないので電圧で読み取り
計算して温度に換算した。
59-2 電圧から温度への換算
ディジタルテスターで測った熱電対の起電力(電圧)を温度へ変換するのに八光電気のホームページを
使わせて頂いた。電圧を入力すると温度へ換算してくれる便利なホームページだ。
https://www.hakko.co.jp/qa/qakit/html/s04010.htm
59-3 零接点温度補償
熱電対は測温点と基準点の温度差により起電力を発生する。
通常の計器では零度を基準とした表示を行わせる為に零接点温度
補償回路を備えている。
ディジタルテスターの零接点温度補償回路はK型用なので使えない。
そこで八光電気のホームページが算出した換算値に室温を加算した。
59-4 測定方法の検証
上述の機器のよる温度測定方法に間違いが無いか検証する為に沸騰した熱湯の温度を測ってみた。
熱電対の起電力は3.8mVで温度に換算すると72.8℃だった。
その時の室温は26.5℃だったので、72.8+26.5=99.3℃になる。概ね100℃だ。
当日の気圧は1005hPaだった。この結果から、この測定方法は使えると判断した。
59-4 測定結果
OctPrintを使ってノズルの設定温度を170℃から240℃まで変えて熱電対の温度を測定した。
結果は下表のようになった。
誤差は下図のように
概ね10℃程高かった。10℃という数字を見ると大きいように感じるが、
割合にすれば+5%程度の誤差でサーミスタでは普通だと思っている。
しかし何故誤差のカーブがう
畝るのか判らない。若しかするとPID制御に伴う温度の揺らぎを拾ってしまったのかもしれない。
59-5 温度補正後の試験造形
測定の結果、誤差が明白になったので温度を補正して造形してみた。
従前はPETGを235℃にしていたが、
10℃下げて225℃で造形してみた。
その結果が下の写真だ。左が従前の235℃、右がー10℃補正した225℃だ。
左の矩形の窓の部分にPETG特有の枝のような突起が成長している。
それが補正後には全く見られない。補正後の温度のほうが適切と思われる。
補正後の造形には右隅に汚れが見られる。熱電対をノズルの先まで差し込んだので
ノズルの内部がかき回されて以前の造形で使った有色のフィラメントが出てきたのではと推理している。
自分の使っているサーミスターは10本纏めてamazon売られていた安価なものだ。
しかしanazonでもAliexpressでも高精度を謳ったサーミスタを見た事が無い。
Original Prusaでは誤差の少ない物が使われているのかもしれない。
60. eSUN製PETGフィラメントを購入 2022,06,30 実施
eSUN製のPETGフィラメントを買った。色は無色(ナチュラル)で¥2,699円だった。
eSUN製を選んだ理由は、過去にeSUN製を使い品質に問題が無かったので信用しているからだ。その上に廉価だった。
無色(ナチュラル)を買ったのは、電子回路基板用のケースを成形したら内部のLEDが透けて光が見えると考えたからだ。
ガラスのように透けて見えるとは思わないが、回路基板の上に設けた通電表示のLEDが光るのが分かる程だろう。
ちょっと残念なのは、開封後に密閉し辛いのだ。最近のフィラメントはジッパー付が多いのだが、これには無い。
評価用に18650電池(Li 二次電池)用のホルダーを成形してみた。
STLファイルはThingiverseからダウンロードさせて頂いた。
タイトルは
Flexing battery
holders with integrated springだ。
成形は完璧だった。ノズルの温度は225℃に設定した。検出誤差があるので実際は235℃になる筈だ。
糸引きも無く、手で力を掛けた感じでは強度も充分の様だ。電池ホルダーとしては充分に実用になりそうだ。
下の写真で造形物の周囲が白っぽく見えるのは、定着補助用に用いたスティック糊の痕だ。
成形物をバネ鋼板から外して18650電池を入れようとしたら、隙間に余裕が無くキチキチだった。
強く押し込んだら入ったが、今度は指先では外れなくなった。
仕方なく電池ホルダーの底部から細い棒を入れて押出し、取り出しに成功した。
18650電池の寸法誤差が大きいのではと疑い、寸法を測ったら直径が18.7mmも在った。
18650の規格では直径は18.0mmなので0.7mmも太い。キチキチなのは当然だ。
流通している
18650電池には同一型番でも長さの違う二種が存在するので要注意だ。
理由は保護回路無しと在りの違いだ。保護回路無しは長さが65mm、保護回路付は69mmだ。
紛らわしいので型番を変えるとか、型番の最後尾にPをつけるとかの工夫が出来ないのだろうか。
自分は安全第一で保護回路付を買った。ネットでバッテリーホルダーを買おうと探したが、
何故か殆どは65mm用だった。僅かに69mm用も在ったが仕様が合わなかった。
仕方なく我がBear Upgrade Prusaで造形することにした。
61. Aystkniet TPU のフィラメントを試用 2022,07,14 実施
具体的な用途は定まっていないが、TPUフィラメントに興味が在った。
amazonが安売りをしたので廉価なAystknietのTPUを購入した。\2,399円だった。
使ってみたら
特に難しいところは無かった。
届いた商品には、フィラメントと別に未使用のジッパー付きポリ袋が入っていた。
真空包装のポリ袋を開けスプールを取り出したら、フィラメントの巻き方がガサガサだった。
ゴムの様な滑りにくい素材なのでPLAやPETGのように綺麗に巻けないのかもしれない。
引出したフィラメントも弛むとヨレヨレだった。まるで癖の付いたゴム紐のようだ。
太さをノギスで測ったら約1.74mmだった。太さの誤差は計測出来ない程に小さい。
エクストルーダーへの差込みはフィラメントが軟らかいので心配したが問題無かった。
ノズルの温度を予め235℃に上げて、エクストルーダーへフィラメントを差し込んだら
AutoLoad filamentが起動されフィラメントが吸い込まれた。
ノズルから出てくるのがPETGよりも少し遅い気がしたが、それ以外はPETGと同じだ。
造形の試験をする為に”D"のような単純な形を設計しPrusa Slicerで処理しようとした。
ところがPrusa Slicerのフィラメント設定枠にTPUが無い。
良く見たらフィラメント設定枠の最下部に
フィラメントの追加/削除が在った。
それを選ぶと下の様な設定表が現れた。AystknietのTPUは無かったのでSainSmartのTPUを選んだ。
当初はノズル温度を235℃で印刷した。その結果、下の写真の右側のように造形物の表面がガサガサだった。
そこでノズル温度を230℃に下げて造形したところガサガサは消えた。
TPUは綺麗に造形する為の許容温度範囲が狭いようだ。
メーカー指定の温度は230℃~240℃と印刷してあった。
バネ鋼板への定着は良好だった。剥がす際はバネ鋼板を捩っても強く定着していてダメだった。
ところが造形物をラジオペンチで摘まみ上へ引っ張ると簡単に剥がれた。
造形物はフィラメントのゴム紐のような軟らかさではなく、スニーカーの底の様な固さだった。
次に3Dbanchyを230℃で造形してみたところ下の写真の右側のようにガサガサだった。
そこで225℃へ下げて造形したところガサガサは消え良い感じになった。
上の造形で船腹部に印刷の乱れがある。
そこでノズルの移動速度を45mmから35mmへと遅くして試した。
その結果、若干良くなったような気もするが乱れは残っている。何が原因か判らない。
61-1 TPU最適温度への絞込み(2回目) 2020,08,29
スピーカーのセンターキャップを凹ませてしまったが、自覚は無い。
そこで掃除機で吸引して修復しようと考えた。
掃除機のホースの先端にセンターキャップの大きさに合わせたノズルを作り
吸い出そうと言う魂胆だ。ノズルの材料はTPU(ゴム)を使って造形した。
造形の際にノズルの温度設定を変えて様子を見た。
下の写真で左から225℃、220℃、230℃、235℃だ。
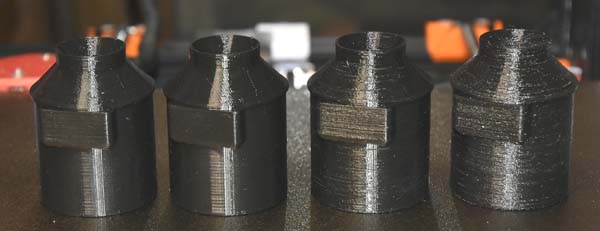
220℃が表面も綺麗で糸引きも少なかった。
ノズルを作った後に掃除機の吸引力は強すぎるかも知れないと心配になった。
そこで下の写真の様に50mlのシリンジで吸引する方法を考え付いた。
先に付いている黒いのがTPUで造形したノズルだ。TPUは便利だ。
62. DSO138のケースを製作 2022,07,23 実施
好奇心から
ディジタルオシロスコープのKitを組立てた。Kitと言っても部品集だ。
買った時点では\2,258円だったが、為替が動き今は¥2,566円だ。プローブは別売りで\808円になっていた。
ケースは付属していないが、透明アクリル板を組み合わせたケースが別売りされている。
自分は帯域が500MHzのデジタルストレージオシロを持っている。
古い製品なのでディスプレイはカラーだが、ブラウン管だ。
性能は抜群に良いが、大きく、重く、電気を食い、ファンの音が煩い。
そこで取り回しの良さそうなDSO138を買ってみた。
基板のままで動かして見たところ低い周波数ならば使えそうだった。
裸の基板では問題を起しそうなのでDSO138基板を納めるケースをClone
Prusaで造形した。
自分で設計したのではなく
Thingiverseから戴いた。
このケースは前側と後ろ蓋で構成されているのだが、固定用のビスが無い。
前後を合わせて強く押すとパチンと音がして嚙み合った。素晴らしい設計技術だ。
ところが基板を入れるとスイッチやLCDの高さが合わず、ケースが閉まらなかった。
仕方なくFreeCADを使ってSTLファイルからソリッドモデルを作り要所を修正した後に
STLファイルに戻した。これによって問題点が解消しケースが閉まるようになった。
造形には
テクスチャーのバネ鋼板を使った。その為に造形物の前面にテクスチャーの凹凸が転写された。
テクスチャー模様なので艶が無くに3Dプリンターで造形したとは思えない質感に仕上がった。良い感じだ。
以前使っていたTriangleLab製のテクスチャーは凹凸が大きかったが、今度のは細かい。
テクスチャーのバネ鋼板もメーカーによって凹凸の大きさが違うようだ。
印刷に使ったフィラメントはPETG、Infillは15%で造形した。
動かして見たところ起動時に表示される筈の製造元の社名が出ず真っ白な画面だった。
それに回路基板に製造元のロゴが無い。自分が買ったのは海賊版だった。
それでスイッチやLCDの高さが合わなかったらしい。
性能は周波数帯域幅が200KHz迄しかないし、トリガーも60KHz程度までしか掛らなかった。
しかしディジタルリードアウトの機能によって周波数やDuty、電圧等が読み取れる。
この性能が三千円程度で買えるのは驚きだ。凄い時代になったと思う。
63. Li電池 18650用ホルダーの製作 2022,08,06 実施
18650と言う型式のLi二次電池がamazon等で売られている。
この電池は容量が大きく電子工作の可能性を広げてくれる素晴らしい物だ。
ところが同じ型番で保護回路の有無や、単一乾電池のような陽極の突起の有無で大きさが違う物が在る。
自分は陽極と陰極の形が異なり陽極に突起があり保護回路が内蔵された18650を購入した。
長さは69mm程だ。選択の理由は最も安全性が高いと考えたからだ。
ところが、これに使えるバッテリーホルダーが見つからない。
殆どのホルダーは長さ65mm用だ。当然69mmの18650は入らない。
そこで自作する事にした。
当初はThingiverseからダウンロードしたファイルを使って製作した。
一応使えたが充分な性能ではなく騙し騙し使っている感じだった。特に電極の部分が半田付けで溶けて頼りなかった。
電極さえ在れば満足できる電池ホルダーが作れる筈と考えて
Aliexpressを探したところ具合の良さそうな電極板を見つけた。
それが下の写真だ。左が陰極用、右が陽極用だ。大きさは縦横12mm、電極部は7mmで厚さ0.3mmだった。
電極版を差し込んで保持する溝を設計し造形した。溝は幅12.4mm。厚さ0.4mmにした。
設計した時点では、我がBear upgrade Prusaの精度に不安が在ったのだが杞憂だった。
下の写真では電極部を拡大した。溝の形は陽極も陰極も同じだ。
強度保持に必要なケースの厚さを探るために3種類を造形した。
一番左は
Thingiverseから戴いた設計で周囲の壁は2.4mmだった。
一番右は最終的に充分な強度が在ると思われる薄くしたモデルだ。
長い部分の横壁が1.2mm、電極を支える部分が4.2mm、底部が2.8mmだ。
フィラメントハ総てPETGだ。黒と赤に塗り分けられたのは造形の途中でオレンジ色の
フィラメントが尽きたので黒を継ぎ足したからだ。
下の写真のように当面必要な3台を製作した。
これでLi 電池駆動デサルフェータやオーディオアンプのLi電池駆動実験が出来る。
63-1. 電池3個 18650用ホルダーの製作 2022.11,14 製作
18650電池を直列に3個使うと12V近くの電圧が得られ電子工作で使い易い電圧になる。
過日に作った1個用を並べれば作れるのだが、纏まりに乏しく不細工になりそうだ。
そこで3個用ホルダーを新たに設計し造形した。
前回は周囲の壁を厚く作ったが、必要以上の強度が在る感じだったので厚さ1.2mmにした。
また電極端子を刺し込む部分の裏側は0.8mmにして強度を試した。
幅の狭い部分だったので大丈夫だったが、広ければ頼りなさそうだった。
厚さ0.8mmだと中空にならないので光が透けている。
実際に電極を取り付け16580電池を入れてみたところ納まったが、
大変に外しにくかった。それでは実用性が無いと判断した。
そこでスライサーで造形の割合を103にしたところ良い感じで出し入れができるようになった。
逆さにして振っても落ちないので実用上の問題は無さそうだ。
使えそうな電池ホルダーが出来たが、要改良点は多々ありそうだ。
この3個用ホルダーを
Printablesに掲示しました。 (2022,12,05)
64. 洗面所混合水栓用工具の製作 2022,08,11 実施
我が家の洗面所にある混合水洗がぐらぐらになった。締めているナットが緩んだようだが締めても直らなかった。
前回取り付けてから随分と時間が経っているので混合水洗を交換することにした。
下の写真はamazonから買った新しい混合水洗だ。TOTOの製品でガッチリ作られている。
固定はチューブの上にあるナットで締め付ける。
ところが締めるべきナットはシンクの奥の狭いところに在る。
洗面台の扉を開けても見えない位置だ。
洗面台の下へ潜り込んで仰向けになると締めるべきナットが見える。
空間の幅が12cm程度しかない。スパナやプライヤーを嚙ませても回せないので使えない。
調べた所、専用の特殊工具が売られているが廉くないし使うのは一度だけだ。
下の写真はナットを既に締めた後です。
そこで3Dプリンターでナットを廻す為の工具を造形した。フィラメントはPETGを使った。
大きさは円筒部の直径が50mm、高さも50mm、六角穴の平行辺の間隔は37mmだ。
使って割れるのではないかと心配したが、杞憂だった。
全力で締めたが歪まず割れなかった。PETGの強さは素晴らしい。
反省点としては滑り止めの溝が浅く少なかった。
印刷時間を短縮するために単純な形にしたのが失敗だった。
もっと大きな溝を沢山設ければ締めるのが楽だったかもしれない。
しかし力一杯に締め付けて目的を達成できた。
3Dプリンターは魔法の様に便利で素晴らしい道具だと感じている。
65. 墓所用造花保持具の製作 2022,08,14 実施
我が家の墓は遠い。墓参には関越道を走るのだが時間も掛るので毎年2回程度しか行けない。
墓参の際に生花を供えると数日後には枯れ、やがて干乾びてしまう。
次の墓参までの半年間、干乾びた花を放置するのは見苦しい。仕方なく造花を供えている。
その造花をステンレス製の花立に飾るのだが、造花は根元が一本に纏めて成形されているので細い。
その為に花立に差し込んでも直立せずフラフラで安定しない。
そこで造花を固定し直立させるための保持具を3Dプリンターで造形した。
材質は過日
試したTPU(ゴム)だ。下の写真で造花の茎に刺してある黒いのが保持具だ。
保持具は造花の茎が差し込めるように穴を開けた。同時に4本の造花を刺せる。
大きさは環状部の直径が30mm、高さが26mmで造形した。
65-1 造花保持具の設置 2022,11,18 実施
今年は雑用がとても多く、墓参へ出かける時間が作れなかった。
やっと時間が出来たので季節外れだが昨日に出かけて造花を入れ替えてきた。
3ヶ月前に
TPUで造形した造花保持具の出番だ。
実際に使ってみると良い感じだった。
花立へ刺し込む際の抵抗感も適度で造花が花立の中央に直立した。
自画自賛だが満点の出来栄えだ。しかし耐久性は未知数だ。
次回の墓参には交換用に造花保持具を造形して持参しようと考えている。
66. TPUで小さな物の造形 2022,09,12 実施
趣味でオーディオの工作を楽しんでいる。今は
直立円筒形バックロードホーンに取り組んでいる。
一般的にSPユニットの鍔には、固定用のビスを通す穴が数箇所に開いている。
我が立円筒形バックロードホーンでは、SPユニットは円筒の上に載っていてビス穴は使っていない。
ビス穴が開いたままでは格好が悪いのでゴム栓を3Dプリンターで造形して埋めた。素材はTPUだ。
下図のように設計した。直径は下段が6.6mmで高さ0.2mmの突起付き、上段が4.6mmで全体の高さは3.5mmだ。
過去の作品では最も小さな造形物だ。
Bear upgrade prusaで造形したところ下の写真の様に出来上がった。
要所の寸法を確かめようとしたが、軟らかい素材なのでノギスでは正確に測れない。
概ね設計どおりに出来ているようだ。ノズルが0.4mmなので限界と思われる。
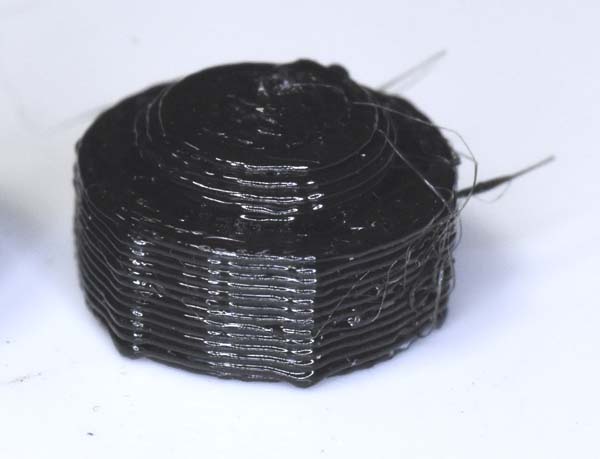
スピーカーユニットのネジ穴へ押し込んだところピッタリと収まった。大成功だ。
67. 聴診棒の製作 2022,10,17 実施
機械や配管の内部を音で探る聴診棒と呼ばれる道具が在る。これを手持ちのパイプと3Dプリンターで作った。
黒い耳当ての部分をTPUで造形した。これを外径4mm、長さ290mmのアルミパイプに嵌めた。
耳当ての部分は、自分の耳の穴の寸法に合せ直径12mm、全長12mmで設計した。
耳の穴を完全に塞がないと感度が低くなるので適切な寸法を選んだ。
耳当ての中央の穴は、アルミパイプに合せて直径4mm、深さ9mmにした。
使ったアルミパイプは以前に作った
WiFi用八木・宇田アンテナ・アダプターの廃材だ。
穴もパイプも直径4mmなので、PETGで成形した場合には入らない筈だが、
TPUには弾力性が在る。その御蔭で良い具合に嵌った。接着剤などは使っていない。
アルミパイプに耳当てを嵌めて聴診棒が完成した。
試すために手元にあった掛け時計のモーター音を聴いてみたところ、ゴロゴロと聞こえた。
その時計は1秒運針ではなく、滑らかに秒針が動いていたのでモーターと歯車の音だ。
設計の間違いや造形の失敗も無く完成した。想定以上に良く聞こえる。
設計開始から完成までに1時間程度で済んだ。3Dプリンターは凄く便利な道具だ。
68.PrusaSlicerとOctoPrintのリンクを設定 2022,10,21 実施
自分はPrusaSlice
2.5を用いてGコードを作り、OctoPrintを
Raspberry Pi Zero 2 Wで動かし造形している。
YouTubeを見ていてPrusaSlicerにGコードのファイルを直接OctoPrintへ伝達できる機能が在るのを知った。
早速試してみた。所在は下記だ。
https://www.youtube.com/watch?v=V2PdG-Wx5Z0
その動画ではPrusaSlicer 2.2を使っていた。自分が使っている2.5と少し違っていた。
リンクを設定する画面が引っ越していたので、その部分だけ以下に記録した。
プレート画面の右に
プリンター選定の窓がある。その右に在る
歯車をクリックすると作業選択の窓が表示される。
下図のように作業選択の窓が表示されたら
物理プリンターを追加するをクリックする。
物理プリンターの設定窓が下図のように開く。
物理プリンターの設定窓を下図のように埋めた。APIキーはOctPrintが支給する暗証番号のような鍵だ。
下図の様に要所を埋めた状態でOctPrintが動いていればテストをクリックして試せる。
OctPrintとの通信が成功すると下図のような表示がでる。これで設定は完了だ。
OctPrintとの設定が完了したPrusaSlicerでSTLファイルをスライスすると下図のように窓の右下隅に
Gボタンが現れる。
これがOctPrintへGコードを伝送するスイッチだ。
Gボタンをクリックすると下図のような窓が現れる。対応動作を選ぶ。
アップロードを選ぶとOctPrintにGコードのファイルが伝送される。
アップロードとプリントを選ぶとファイルが伝送され
造形が始まる。
その場合にはブラウザーでOctPrintを開かなくて済む。
従前はPrusaSlicerでSTLファイルをスライスして作ったGコード ファイルを
HDDに書き込んでからOctPrintに読ませていた。
その過程を経なくても造形出来るようになった。便利になった。
◎
68-1 PrusaSicerとOctoPrintのリンクで初の造形 2022,10,31 実施
5年前に作った
メジロ用の餌台が壊れた。鉄線で作られた籠を支えるキャッチャーの部分が割れたのだ。
下側のキャッチャーが割れたので陽光に含まれる紫外線の影響だろう。
そこで昔のホルダーを開き必要な部品のSTLファイルをPrusaSlicerへ読み込み並べた。
Gボタンをクリックして造形を始めたした。
アップロードとプリントを選んだのでGコード ファイルは作られなかった。
アップロードとプリントは
案外に便利だった。下の写真は完成したキャッチャーだ。
69.PrusaLinkのインストール 失敗 2022,10,27 実施
先日行った
PrusaSicerとOctoPrintのリンクを設定で
PrusaLinkの存在を知った。
先日までOctprintに使っていたRaspberry Pi Zero WをRaspberry Pi Zero 2Wへと更新したのでZero
Wが遊んでいた。
この遊んでいたRaspberry Pi Zero W使って
PrusaLinkを試そうとしたが
拒絶された。以下に説明する。
PrusaLinkのインストール方法は
PRUSA
RESEARCH社のホームページに在るガイドに詳しく書かれている。
それに従って作業を進めた。ハードの部分は既にOctprintをインストールする際に施工済みなので、
マイクロSDカードへPrusaLinkを書き込めば準備完了だ。
ガイドのようにRaspberry Pi Imagerを設定しマイクロSDカードへ書き込もうとしたが、
ここで問題が発生した。使ったマイクロSDカードは以前の実験でOctPrintを書き込んだ。
これを自分が主力で使っているWin7のパソコンが認識せず書き込めなかった。
仕方なくWin11のパソコンでやり直した。
驚いたのはRaspberry Pi ImagerがSSIDとパスワードをパソコン本体から抽出し自動登録した。
パスワードは長いので間違いやすい。それが簡単になったのは助かる。
その後無事にマイクロSDカードへの書込みを終えた。
書込みが済んだマイクロSDカードをRaspberry Pi Zero Wへ差込みClone Prusaへ組み込んだ。
電源を入れて待ったのだが、ガイドに在るLCDに
"Starting Prusa Link "が表示されない。
それに続いて表示される筈の
"GO: 10.10.10.10"も出ない。
Raspberry Pi Imagerへの設定を間違えたのかと思ったが、SSIDとパスワードは自動抽出だ。
念のため
Advanced
IP Scannerを使ってルーターに繋がっている機器の一覧を見た。
その結果、下図の様に正常に繋がっていた。
blackが黒色のClone Prusaだ。
何故
"Starting Prusa Link "が表示されなかったのかは謎だ。
自分のClone Prusaのファームウエアは3.110で問題無い筈だ。
ブラウザーにblackのIPアドレスを入れたところ下図のようにPRUSA LINKの画面が出た。
Raspberry Pi Imagerへの設定は正しかったようだ。
PRUSA LINKの画面ではSerial Numberの入力を求められたが、
Clone PrusaにはSerial Numberが無いのでこれ以上は進めなかった。
Clone PrusaではPRUSA LINKを使えないのが判った。
自分は従前からOctPrintを使っているので問題は無い筈だ。
PrusaLinkをインストールしてみた感想だが、OctPrintに比べてインストールが優しい。
OctPrintではRaspberry Pi Imagerで書き込むだけでは済まず、テキストエディターで
SSIDとパスワードを書き込んだりGPIBの設定を書き換えたりしなければならず敷居が高い。
それらをRaspberry Pi Imageだけで済ませるように作ってある。その点でPrusaLinkは優れている。
70.PrusaSlicerの異常動作 2022,12,26 実施
いつもの様にPrusaSlicer2.5.0を使い3D-CADで設計したSTLファイルをスライスした。
そこで異常が発生した。スライス後の造形物が造形台から浮いていた。明らかに異常だ。
これでは造形物が造形台に密着してないので定着しないかもしれない。
そこで単純なドーナッツ状のSTLデータを用いて造形まで試してみた。
下図の上はPrusaSlicerへドーナッツを読み込んだところだ。
下図の下はスライスが済んだ際の画だ。造形物が宙に浮いている。
造形したところ普通に正しく出来上がった。外径32mm、内径16mm、厚さ5mmだ。
結局、使って問題ない事が分かったので大きな障害ではない。
しかし原因が判らない。自分が誤操作をしたのか?
OSがWindows-7のせいなのか、Bugなのか?解らない。
問題を解決する為にPrusaSlicer2.5.0を消去し再インストールしてみたがダメだった。
PrusaSlicer2.5.0にはプリンターの種類を追加/削除する項目が在る。
これを利用しBear Upgrade Prusa #1 Original Prusa i3 MK3S & MKS3+と設定していた。
若しやと思いこれをOriginal Prusa i3 MK3S & MKS3+に設定した。
その結果、問題は解消した。
PrusaSlicer2.5.0のプリンターの種類を追加/削除する機能は何か変だ。
71.磁石付部品トレーの製作 2023,01,08 実施
Prusaの整備を行う際にビスを外す。その際に小皿にビスを納めて散逸しないようにしていた。
そこで専用のトレーを作った。特徴は要所にネオジム磁石を接着した事だ。
これによって小さな部品を吸着すると共に造形バネ鋼板にも吸着し安定した。
皿のように滑り落ちる危険性は解消した。
下の写真は完成した磁石付部品トレーだ。大きさは縦横共に100mm、厚さは15mmだ。
造形にはPETGを用い、サポート、筏、鍔は使わず内部充填は20%だ。
ネオジム磁石は直径13mmで厚さ2.5mmだ。百円ショップのSeriaで買った。
それをゴム系接着剤で固定した。
ネオジム磁石を収納する窪みは直径13.2mm、深さ2.5mmで設計した。
寸法を確認する為に要所を切り取り造形時間を短縮する確認用モデルを作った。
ネオジム磁石を嵌め込んだところ、良い感じにピッタリで接着剤無しでも固定できそうだった。
この製作データを
Printablesに挙げた。
https://www.printables.com/model/363895-magnetic-parts-tray
72. 六角レンチ用グリッパーの製作 2023,01,22 実施P六角レンチ
キャップネジに用いる六角レンチの操作性を改善するジグを作った。
これはPRUSAに多用されているM3専用だ。
ネジを緩める際に強く廻すのは最初だけで後は軽く廻せば済む。
しかし六角レンチは軽く廻す際には操作性が良くない。
そこで胴の部分を少し太くして親指と人差し指の先で挟んで捩るように廻せるようにした。
造形にはスティック糊を使って定着させたのでサポート、筏、鍔は使わなかった。
この製作データを
Printablesに挙げた。
https://www.printables.com/model/376786-hex-wrench-gripper
73. PINDAをSuper PINDAへ交換 2023,02,10 実施
従前のPINDAは検出距離が周囲温度の影響を受けるので、
サーミスタを内蔵して温度を測り制御コンピュータで補償の計算をしていた。
本家のオリジナルPRUSAでは数年前からSuper PINDAが使われている。
Super PINDAは温度補償が不要になった便利なセンサーだ。
過日、AliexpressのPRUSA用Partsを眺めていたら
CloneのSuper
PINDAが売られていた。
面白そうだったので早速注文したところ約2週間で届いた。
下の写真が届いたCloneのSuper PINDAだ。出費は\2,454-だった。
早速通電して機能を確認した。
Super PINDAは従前とコネクターが同じで刺しかえるだけで簡単だった。
しかし、このCloneのSuper PINDAは動作表示LEDが暗く見辛かったが、動作はしていた。
ポストイットの束を透過させ動作した紙の厚みをノギスで測り検出距離を求めたところ
2.5mm以下で検出した。従前のPINDAが2.0mmだったので0.5mmだけ広い。
下の写真では動作表示LEDが暗く見えないのでPRUSAのモニター機能を使って確認した。
CloneのSuper PINDAが動いたのでPRUSA本体に仮止めしてLive Zの調整を行った。
その際の設定値がー1.700mmだった。従前が-0.850mmだったので大幅に移動した。
しかし、これが間違いだった。交換作業の当初から電源を投入したまま作業したので
ファームウエアは従前のPINDAが使われているものと判別して温度補償を行い誤差を生じていた。
その後に電源を切り従前のPINDAを取り外してSuper PINDAへ置き換えた。
電線の束も解いて被服を巻き直した。電源を再投入してLive Zの調整を行ったところ
ノズルが下がりすぎて造形鋼板を削りそうな位置まで下がってしまった。
その後に最適なLive Zを求めたところ-1.000mmだった。
ファームウエアは電源投入直後に使われている位置センサーがPINDAかSuper PINDAを
識別し、専用の制御プログラムを実行するようだ。
Live Zの調整で描いたジグザグが、下の写真の様に従前よりも綺麗に見えた。
線の幅も厚みも安定している、大きく違うのは、左手前の書き出しの線だ。
従来は幅が広く厚い線が盛り上がってポッテリしていた。それが薄くなった。
制御ソフトが改善されたのは間違いない。
若しかするとZ軸の位置決め制御の性能が向上しているのかもしれない。
その後、以前に作った六角レンチ用グリッパーを造形してみた。
左がSuper PINDAで右がPINDAだ。 結果に差は無いが好奇心が満たされた。
74. テフロン加工ノズルへ交換 2023,02,16 実施
Triangle Lab製のKitを組立てて使い始めてから4年目に入った。
その間に酷使したのでノズルが消耗したようで、最近ではフィラメントの導入時に写真の様に癒着が頻発する。
原因はノズルの穴の周囲に付着したPETGによる汚れと損耗だと推定した。
穴の周囲が汚れにくいノズルが在るのではと考えAliExpPressで探したところ
テフロンコーティングされたノズルが売られていた。しかも5個で487円と安価だった。
下の写真で右がテフロン加工されたノズルだ。
熱伝導を妨げないようにネジの部分にはコーティングが無い。良く考えられている。
下の写真で左は取り外したノズルだ。
六角の部分が変形しているのは取り外す際にプライヤーで強く挟み変形した。
ネジの部分が灰色なのは、伝熱グリースだ。乾いて固まり外しにくくしていた。
穴の周囲に黒く炭化したようなフィラメントが付着している。
下の写真はノズルの下にLEDライトを置き、下から光を当てて撮影した。
取り外したノズルは酷い汚れだ。中にフィラメントが入っているので光は通らない。
右のテフロン加工されたノズルは、あなが綺麗に丸く開いている。安価だが問題無いようだ。
テフロン加工されたノズルのネジに伝熱グリースを塗り、ヒートブロックへ取り付けてから
PIDのチューニングを行い、その後にLive Zの調節を行った。
試運転に以前に作った六角レンチ用グリッパーを造形してみた。
下の写真で左端がテフロン加工ノズルで右の2個は損耗したノズルでの造形だ。
テフロン加工ノズルのほうが稜線が鋭く鮮明だった。
テフロン加工ノズルは普通に使えた。
テフロン加工の効果は判らないが、悪化したところは無い。
暫く使えば効果が判るかもしれない。
テフロンのフライパンでも長い間使うとテフロンが剥離する。
テフロン加工ノズルのテフロンも何れは剥離するのだろう。
75. テフロン加工ノズルの評価 2023,03,27 実施
テフロン加工ノズルへ換えて10個以上の造形を行った。延べ稼働時間は30時間程度だ。
そこでノズルを評価するために写真を撮影し点検した。
下の写真で左が30時間の造形後、右はノズルを230℃迄過熱した後に綿棒で拭取った後だ。
左ではテフロン加工されたノズルの周りに付着物がありテフロンが見えない。
右ではテフロンが見えているが、ノズルの先端と根元の部分の色が違う。
たぶんノズルの先端のテフロンが剥げたのだろう。
以上の結果からテフロン加工ノズルには、特別な価値は無さそうだ。
但し、このテフロン加工ノズルで不都合は微塵も無い。よって継続して造形に使い続ける。
76. ノズル・クリーナーの製作 2023,04,08 実施
造形の際にフィラメントが細い糸を曳く。これがノズルの円錐部へ付着しノズルが汚れる。
汚れが目立ってきたらティッシュを四つ折にしてノズルを挟んで拭取るのだが、綺麗に拭取れないし熱い。
綿棒でふき取る際には、熱くないが小さなノズルの周囲に沿って綿棒を動かすのが、なかなか難しい。
そこで下の写真のようなノズル・クリーナーを作った。
軸を半分の長さにに切った綿棒を本体へ差込み、3本を組み合わせた。
綿棒はジョンソン・エンド・ジョンソン製で軸の長さは52mm、太さは2.4mmだった。
綿棒を組み合わせた様子は、下の写真のようだ。3本の中心にノズルを当て廻しながら拭取る。
下の写真は使っている様子だ。シリコン・ソックスが在ると上手く拭けないので外した。
この造形ファイルをPrintablesに掲示した。
https://www.printables.com/model/446362-nozzle-cleaner
77. ノズル用レンチの取っ手を製作 2023,07,20 実施
ノズルを交換する際に使うソケットレンチが大袈裟に感じていた。
ラチェット式の取っ手に交換式のソケットを刺し込む方式だった。
もっと簡便な専用工具は無いものかと
Aliexpressの中を探していて具合の良さそうな十字レンチを見つけた。
何故か大変に廉く、送料を含めてたったの226円だった。
注文から2週間程で商品が届いた。届いた実物を見て廉かった事に納得した。
全体が小さく手でガッチリと掴むことが出来ない。手で掴む部分の長さは24mmしかない。
親指と人差し指で挟んで廻せるが、力が入らず強く締められない。
このままでは使い物にならない。
使えないままで暫く放置していたのだが、詐欺に騙されたようで甚だ面白くない。
そこで取っ手を作ってみた。下の写真の様に横棒の部分まで取っ手に埋没するように設計した。
造形は1時間ほどで完了した。完成した取っ手に十字レンチを差し込んだところガタツキも無く納まった。
一度の造形で成功したので大成功だ。下の写真では大きく見えるが、取っ手の直径は40mmと小さい。
ノズルを緩めたり締めたりする際には、ノズルを過熱して行う。
その際の熱が十字レンチを伝ってPETGで成形した取っ手に伝わってきてPETGを
軟化させるのではと心配したが、長時間の作業を行わなければ問題ないのが判った。
実際に試用してみると従前のラチェット式ソケットレンチよりも使い易いところが在った。
ラチェット式ソケットレンチではソケットの部分が大きく、ヒートブロックを固定するための
スパナーと干渉した。今度の十字レンチでレンチの部分が薄く小さいので干渉が少なくなった。
それに全体が小さいので掌に乗る。ネジ回しのように片手での操作が楽に出来る。
この取っ手によって使い物にならなかった十字レンチが、使えるようになって嬉しい。
日本のamazonでも、下の絵の様に十字レンチが売られていたが価格はかなり高目だ。
米国の
amazonでは十字レンチ単体で売られていたが、6$で若干値が張る。
この設計データーを
Printablesに掲示した。
https://www.printables.com/model/531585-nozzle-wrench-gripper
78. Super P.I.N.D.A 誤差増大 2023,07,20 実施
先に行ったノズルレンチ用の取っ手の造形でトラブルが在った。
下の写真の左側の様に初層がガサガサになってしまった。
自分のClone PRUSAは、とても安定なので造形の度には調整しない。
今回もいつもの様にOctPrintのWiFiで造形データを送り込み、遠隔で造形を始めた。
造形を終えたので造形鋼板から剥がしてみて初層がガサガサだったのでビックリした。
原因を探るためにLive Zを実施したところ0.5mmほど高い方向に狂っていた。
前回の造形は4月で今回は7月だ。そのときの室温は約30℃だったので誤差を生じたのだろう。
その後、OctPrintのPrusa Leveling Guideを使って造形鋼板の傾きを調べた。
驚いた事に左側が1mm程度も高く傾いていた。つまりX軸が造形鋼板と平行ではないのだ。
Prusa i3 MK3のZ軸は電源を切った時点でステッピングモータが制御磁界に拠る拘束から開放され
物理的に安定な位置へ移動する。これが蓄積されてX軸が傾く。
Prusa i3 MK3には、この問題を解決すべくCalibrate Zの機能が在るが造形の度に実施するのは甚だ面倒だ。
この問題を回避すべくPrusa Slicerの
カスタムGコードにZ軸を上限のストッパーに衝突させて誤差を打ち消す文を追記した。
しかし、その機能が働いていなかった。その原因を追究したらPrusa Slicerを2.6.0へ更新した際にカスタムGコードが
継承されていなかった為と判った。カスタムGコードへ衝突文を追記して解決した。
Live Zを修正しPrusa SlicerのカスタムGコードへ衝突文を追記して造形したのが冒頭の写真で右側の赤だ。
注:カスタムGコードはPrusa Slicerの難易度設定を高度にしないと表示されない。
79. Super P.I.N.D.A の滑り防止 2023,09,16 実施
先日の造形でノズル付近からカリカリという感じの小さな異音が出た。
一層目が僅かに剥離して捲れ上がりPINDAに当たった音だったようだ。
次の造形では、ノズルが下がり過ぎて造形鋼板を擦ってしまい痕が付いた。
原因は
PINDAが上方向へ滑って移動したため相対的にノズルが下がり過ぎた為だ。
下の写真は、その様子だ。白く見えるのは初層の定着を強くするスティック糊だ。
そこでPINDAが上へ滑るのを防ぐ為に、PINDA購入時に付属してきたナットを組み込んだ。
ところがナットを締めるとPINDAが下へ動いてしまうので調節が難しい。
試行錯誤の結果、PINDAと造形鋼板の隙間をPRUSA社指定の1mmに合せることができた。
これで正常に造形出来るようになったが、ナットによる固定は調節が難しいのが欠点だ。
もっと簡便な方法を探していて
ゴム系接着剤を塗る方法を思いついた。
下の写真の様にPINDAのネジ部中央付近にゴム系接着剤(ボンド G17) を塗った。
充分に乾いて接着力が無くなってから組み込んで見た所、
従前の様に簡単に滑る感じではなく抵抗感があり良い感じになった。
これなら剥離の捲れ上がりにPINDAが当たっても簡単には滑らないだろう。
もちろんPINDAを取り付けてから初層校正を行い、Live-Zを調整した。
80. 大きな物の造形 2023,10,31 実施
2台目の直立円筒バックロードホーンの製作に着手した。
3Dプリンターでの造形開始から10日ほど経過し、総てのプラスチック製部品の造形を終えた。
昼夜に亘って造形を続けたがノズル詰りなどのトラブルも無く快調に働いてくれた。
また糸引きは皆無だったので造形後の手間が掛っていない。
円筒部の高さは各段とも20cmで5段を重ねると高さは100cmになる。
円筒部の直径は左端の最下部が20cmで右端の最上部が10cmだ。
前回と同じ寸法でClone PRUSAで造形できる最大寸法だ。
使用したフィラメントはTINMORRY社のPETG Cool whiteだ。これを4本購入した。
3本で済む計算だったが、造形の失敗が在り4本目の半分程度まで消費した。
このフィラメントは乾燥剤が入ったポリ袋に真空包装されていた。
別にジッパー付きのポリ袋が添付されていた。開封後の湿気防止対策だろう。
スプールに空の重量が180gと明記されていたが、自分が測ったところ
196gだった。
◎気温低下によるトラブル
造形は最上部の細い部分より始め下へと進めた。
上から4段目の2個目(ステレオなので)の造形を終えたところで異変に気が付いた。
下の写真の様に造形物の表面が小さくガタガタになってしまった。
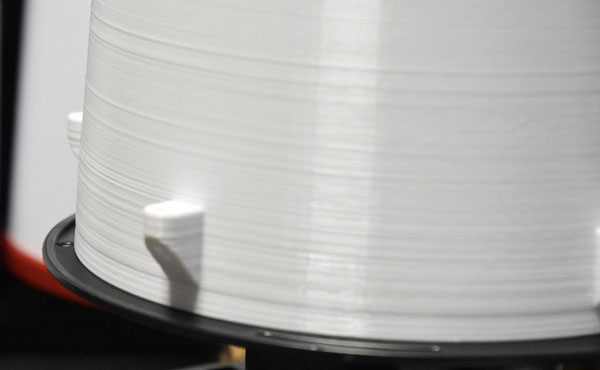
X軸とY軸の駆動部に緩みが発生したかと考え点検したが、問題は無かった。
若しやと思いノズル温度を225℃から230℃へと5℃だけ上げて造形したところ問題は解消していた。
我が家では3Dプリンターで造形する際はベランダにて、ダンボールの風除けで囲っている。つまり風の在る屋外だ。
4段目の1個目の印刷では気温が高く夏の終わりと言う感じだった。
それが4段目の2個目では気温が下がり冬の始まりのようになった。
その為にノズルの先端の温度が下がり溶けたフィラメントの粘度が上がり吐き出した糸の太さが変動したようだ。
PETGフィラメントは温度に敏感なようだ。
◎
フィラメント継足しでのトラブル
大きな物を造形するとスプールにフィラメントが中途半端に残ってしまう。
その対策として
PRUSA i3にはフィラメント継足し機能が備わっている。
フィラメントセンサーがフィラメントの終わりを検知するとブザーで教えてくれる。
そしてフィラメントセンサーからノズルに至る残存フィラメントの排出を促す。
ボタンを操作し排出操作を終えてから補充フィラメントを装填すると造形を継続してくれる。
フィラメント継足し機能の活用によって新品スプールの大部分を捨てることなく消費した。
無駄になったフィラメントは10cm程度だった。
下の写真はホーンを支える足を造形した。高さ方向の半分ほどの位置でフィラメントが終わった。
その上は新しいフィラメントに継ぎ足して造形した。
フィラメント継足自体は成功したのだが、下の方が色が僅かに暗いのが判る。
フィラメントの色にバラツキが在ったようだ。
フィラメント継足には、このようなトラブルも起きる可能性がある。
81. 炭素繊維入りPETGの試用 2023,11,22 実施
以前から炭素繊維入りのフィラメントに興味が在った。
しかし売られていたのが炭素繊維入りPLAばかりだった。
最近になって炭素繊維入りPETGが出回ってきた。
アマゾンの安売りでTINMORRY製が安く売られていたので買ってみた。
通常は¥3,700-程の価格だが、概ね千円引きだった。
下の写真は購入したTINMORRYカーボンファイバーPETGフィラメントだ。
スプールは厚紙製で、炭素繊維の含有率についての記載は無かった。
乾燥剤入りのポリ袋に真空包装され、別に保存用のジッパー付きのポリ袋が添付されていた。
フィラメントに触れると針金の様に硬く、エクストルーダーが吸い込んでくれるか心配になった。
◎
耐磨耗ノズルへの交換
Webでカーボンフ フィラメントを使った記事を漁ると、通常の真鍮製ノズルでは造形中にノズルの穴が削られ
大きくなってしまうそうだ。そこで硬いノズルを探した。
ルビーノズルやタングステンノズルが理想的なのだが高価だ。
硬化鋼製は比較的安価だが、熱の伝導性が低いので温度制御性能の低下が懸念された。
時間を掛けてAliexpress内を調べた所面白そうなノズルを見つけた。
本体がジルコンー銅製でノズルの先端に硬化鋼を嵌め込んである複合金属構造だそうだ。
価格も¥833-と手頃だった。ジルコンー銅は真鍮よりも熱伝導性能が良いらしい。
下の写真で左が
複合金属ノズルで、右は先日まで使っていたのと同じ真鍮テフロン被覆製だ。
複合金属ノズルの本体にはニッケルメッキが施されている。たぶん防錆だろう。
複合金属ノズルをprusaへ取り付けてからPIDチューニングを行った。
その後にPETGフィラメントで3dbencyを造形し温度の制御性能をチェックした。
性能が向上するかと期待したが、温度の振動は従前と同じ程度だった。悪くはなっていない。
◎
フィラメント送出ギヤを硬化鋼へ交換
標準的なフィラメント送出ギヤはステンレス製だ。
Webには、これをカーボンフ フィラメントで使うと磨耗すると書いてあった。
Aliexpressでは
硬化鋼製のフィラメント送出ギヤが売られていたので入手した。
ギヤだけではなくベアリングやシャフトも同梱されていた。
価格は\1,301-だった。
イモネジが2個含まれていたが、使い道が無かった。
◎
試運転
複合金属ノズルと硬化鋼製送り出しギヤを組み込んだprusaで試運転を行った。
ノズルを交換したので初層校正を行った後に3dbencyを造形した。
先ず従前の機能がPETG-Carbon対応改造で失われていないか確認する為に通常のPETGで造形してみた。
その結果、普通に造形できた。写真の写りが良くないが正確に造形された。僅かに糸引きが見られる。
次にPETG-Carbonで造形した。スライサーの設定は、先の造形で使った青色PETGと同じだ。
下の写真のように何のトラブルも発生せず造形を終えた。
若干の糸引きが見られ、全体に毛羽立っているような感じだが正確に造形されている。
PETG-Carbonでの造形では難しい問題が発生するのかと心配していたが杞憂だった。
普通のPETGと同じように扱ったが何の問題も起こらなかった。
PETG-Carbonフィラメントに触れた感じでは、通常のPETGよりも硬いので強度が高そうだ。
従前よりも3Dプリンターの応用範囲が広がるだろう。
好奇心からClone prusaをPETG-Carbon対応へ改造したが、簡単に済んだ。
しかし耐久性は判らない。改造前よりも向上した筈だが、そう在って欲しい。
部品を入手したAliExpressには各種の改造用部品が売られている。
玉石混交だが、適切に選ぶことができれば便利な店だ。
82. 二色造形の失敗 2023,12,08 実施
下の写真の様な
直立バックロードホーンのSPユニットを保護するカバーを造形した。
目的はSPユニットのコーンやセンターキャップに手で触れるのを防ぐ為だ。
機能的には一色で造形すれば済むのだが、格好良くしたかったので赤と黒の二色で造形した。
マルチマテリアル装置は持っていないのでスライサーでフィラメント交換位置を設定し
手動でフィラメントを交換して造形した。材質はPETGで温度は230℃/75℃だ。
造形は問題なく成功したのだが、造形後に格子の最下部を横に押したら赤と黒の接合部が外れてしまった。
充分に融着していなかった。この部分の融着する面積は1.2mm*2.4mmと小さい。融着が不完全だった理由は、
赤色のフィラメントを外し黒色のフィラメントを装填するまでの時間に赤色フィラメントが冷えた為と推察した。
対策は下図のように赤と黒の接合部に一辺が1.2mm小さなのサポートを45度の角度で追加した。
それに赤い円筒部の最上部の一層を黒色で造形し赤と黒の接合面積を増やした。
下の写真は対策を施した後の造形だ。接合部も充分に強く問題は解消した。
自分はサポートや鍔、筏は用いないように設計している。
成形後の除去が面倒なのとフィラメントを無駄にしたくないからだ。
しかし制約が多いのでドームのような形状になってしまった。
格好が良いかは微妙だが先ず音への影響を試す予定だ。
83. PETG-Carbonで造形 2023,12,10 実施
2017年にメジロ用餌台を3Dプリンターで作った。
その時期には以前のJGAURARO製のプリンターを使っていたので、
このホームページには記事が無いが
TingiverseにBird Food Table
という名称で掲示してある。
その中のBasket_catcherという鉄の枠を受ける部分が壊れた。
2019年にも壊れて作り直した。黒色のPETGは4年間も屋外で耐えてくれた。
今回の造形では、更なる寿命延長を狙いPETG-Carbonで造形した。
必要数は3個なので3個を一回で造形した。ちょっと糸引きが多いが設計どおり出来上がった。
材質はTINMORRY製のPETG-Carbonを使った。温度は230℃/75℃で造形した。
この部品は鉄の針金で作られた枠をプラスチックの弾性で挟み保持する。
その部分を指で押してみると従前のPLAやPETGに比べて硬く強い感じだ。
PETG-Carbonの耐候性は判らないが、大いに期待している。
84. ノズル用レンチの取っ手を再製作 2023,12,21 実施
今年の7月にノズルレンチの取っ手を設計製作し、その記事を
Printablesに掲示した。
すると読者から寸法が
hair tightだと指摘された。狭くて入らないという意味らしい。
自分のは問題無く収まっているのでレンチの寸法にバラツキが在るのではと疑った。
そこで新たに2個の同じレンチを購入して寸法を調べたところバラツイていた。
縦棒の太さは変わらなかったが、横棒の太さは0.2mm程度の誤差が在った。
また横棒の長さにも0.2mmほどのバラツキがあった。
従前の取っ手に差し込んで見たところ読者の指摘の通り入らなかった。
この問題に対処するために設計を修正した。確認のために造形したのが下の写真だ。
同じ色で造形しても面白くないので手持ちのフィラメントの中から青白赤を使った。
何れもPETGだ。造形条件は230℃/75℃だ。
下の写真は完成したノズル用レンチだ。フランス国旗の様に並べて撮影をした。
85. 腕時計用治具の製作 2024,01,26 実施
愛用している腕時計のベルトが壊れた。時計本体にベルトを固定するバネ棒が腐食したらしく外れたのだ。
この時計はカシオのPROTORECという商品で太陽電池を動力源として動き、自動的に電波で時刻を合せる。
特に陽光に曝したりせず普通に腕に着けているだけだが電力不足で止まった事や狂った事は一度も無い。
維持に手間も費用も掛からない優れ物だ。自分は滅多に使わないが、気圧測定の機能や方位測定の機能も備えている。
20年近く使っているので買い換えても良い時期だ。そこでカシオのカタログを見て好みの時計を探したのだが、
デザインが気に食わない。現在のモデルは液晶表示と長針短針を備えたデジアナが主流になっている。
技術的には素晴らしい物なのだが、デジタル表示が在れば針は要らない。前世紀の遺物だと思っている。
それに表示面のデザインがゴチャゴチャして好きになれなかった。
そこで気に入っている現在のPROTORECのバネ棒を交換し現役を継続する事にした。
amazonでバネ棒を探したところ長さの違うバネ棒が各15本ずつ入ったセットが494円で売られていた。
早速これを入手した。驚きの廉さだったので品質に不安が在ったが、実物には問題無かった。
届いたバネ棒を時計に組み込もうとしたら上手く入れられなかった。
この時計のベルトを固定する構造が特殊で簡単にはバネ棒を嵌められなかった。
対処するために時計の本体とベルトの位置を固定する治具を作った。
その治具の御蔭でバネ棒は上手く収まった。
フィラメントはPETGで積層厚は0.2mm、内部充填は15%で造形した。
この造形では糸引きは全く無かった。
3Dプリンターを持ってなかった当時は木材を削って治具を作っていた。
下の写真は電池を交換するためにネジ式の裏蓋を開けるための治具だ。
木材では正確に削りだす木工技術が必要だが、3Dプリンターならば設計するだけで作れる。
きわめて簡単な作業だ。3Dプリンターは必要不可欠な工作機械だ。
86. 電子機器用筐体の造形 2024,02,17 実施
3Dプリンターを導入した目的の一つは、電子回路を収納する筐体を3Dプリンターで作る事だった。
筐体作りは一連の電子工作の中で最も面倒な作業だ。
それを2月に行ったオーディオ用デジタルアンプの製作で実現できた。
アンプの基板はAliexpressから買ったので筐体を作れば大部分の工作は終わりだ。
3D-CADでの設計に2日ほど掛ったが造形は4時間で済んだ。
造形は何のトラブルも無く済んだが設計に不適切な部分が在った。
最大の失敗は厚さだ。上面も側面も厚さ1.2mmで設計した。
PETGフィラメントで作ってみると薄くて強度が足りずフカフカだ。
両側面のルーバーの部分は掴んだ際に割れてしまったので後日に補強した。
前面に取付けたボリュームはツマミを廻すと軸がフラフラする。
次に作る際には厚さを2.4mmで設計しようと考えている。
若干の問題は在ったがアンプは完成し御機嫌な音で鳴っている。
筐体以外に両脇の補強やボリュームのツマミもPETGで成形した。
底面のゴム脚はTPUフィラメントを使って成形した。
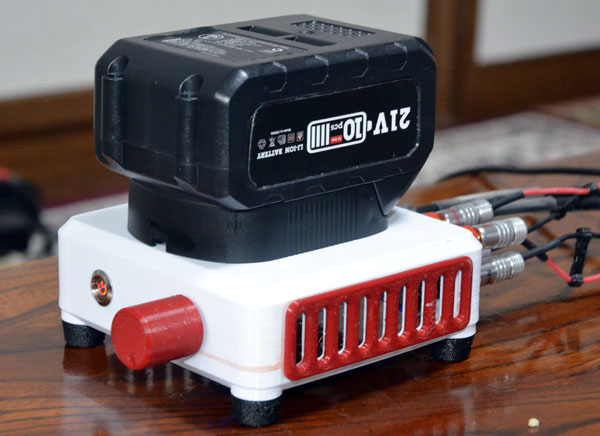
上の写真はアンプ本体に電動工具用Li二次電池を搭載した様子です。
製作の詳細はコチラです。
87. メジロ用餌台の補修 2024,04,20 実施
2017年にメジロ用の餌台を作った。屋根と皿はガーデニング用の皿を活用した。
メジロは蜜柑や果汁などを好むが、同じ嗜好のヒヨドリがメジロを蹴散らし
餌台を独占してしまうのでヒヨドリが入れない狭いピッチでナイロンのテグスを張った。
これが大成功でメジロは翼を窄め止まり木へ直接的に飛行できるが、
体の大きなヒヨドリは通り抜けられずヒヨドリを排除できた。。
3Dプリンターで作ったのは止り木の部分だ。フィラメントはABSを用いJGAURORAのA3プリンターを使った。
PRUSAに比べて手間の掛かる不便なプリンターだったが、騙し騙し使いこなしていた。
その止り木の部分が劣化して割れてしまった。
5年以上も野晒しで紫外線を浴びたので当然の結果だ。
屋根と皿も射出成型によるABS製だが割れるほどには劣化していない。白っぽくなっただけだ。
止り木に使ったフィラメントのABSは顔料が含まれないナチュラル色だったので弱かったのかもしれない。
ナイロンのテグスには劣化の気配は見えず切れたりしていない。
自分のClone PRUSAは炭素繊維を含むフィラメントに対応すべく送り歯車とノズルを硬化鋼に替えてある。
手元にCarbon Fiver PETGフィラメントが在ったので、それを使って止り木を造形した。
環の部分と脚は別々に造形しアクリサンデーを使って接着した。
造形温度は通常のPETGと同じ230℃/75℃だ。糸引きは皆無ではなかったが僅かだった。
Carbon Fiver PETGフィラメントで造形したので艶消し塗装を施したような独特の風合いに仕上がった。
使用したフィラメントは
TINMORRY社のCarbon Fiver PETGだ。造形に際して何も問題は無かった。
カーボンファイバー混入のフィラメントではカーボンファイバーが紫外線の内部への侵入を
防いでくれる筈と考えた。何年持つのか判らないが楽しみだ。
88. 鉛製ガスケットの製作 2024,04,24 実施
自分のClone PRUSAではスロート管とノズルの接合面に鉛で作ったガスケットを挟んでいる。
以下にそのガスケットの作り方を紹介する。
それはスロート管とノズルの接合面から溶けたフィラメントが漏れ出てネジの隙間を通り抜け造形物が汚すのを防ぐ為だ。
その現象は同じ色のフィラメントを使い続ければ判らないのだが黒色や青色から白色へ切替えると目立つ。
メーカー指定の組立て方ではスロート管とノズルの接合面は突き合わせて強く締めるだけだが、
自分の経験では、その方法で完全に漏れを止めるのは難しかった。
ガスケット用に鉛を選んだのは融点が327.5℃で軟らかく好都合な素材だった。
鉛ではなくガスケット用シートが市販されているがPETGの230℃に耐える物が見つからなかった。
そこで釣具用の鉛のシートから丸く小さな板を切り出し中心に穴を開けてガスケットを製作した。
下の写真は自作した外径5mm、内径3mm、厚さ0.5mmの鉛製ガスケットだ。
(1) 小円盤の切り出し
釣具用の鉛のシートから直径5mmの円盤を切り出した。
鉛のシートから直径5mmの丸い円板を切り出すのに鋏は手間が掛るのでハンドパンチを使った。
本来紙に丸穴を開ける道具でダイソーで買った。直径5mmと表示してあったが、実際には6mmだった。
その為に直径を削る作業が必要になったが、鋏で5mmの円板を削りだすより遥かに楽だった。
下の写真の様に厚さ1.0mmの鉛シートから直径6mmの円盤を切り抜いた。
(2) 鉛円盤の中央に穴あけ
電動ドライバーにドリル刃を取付けて位置決め治具を使って鉛円盤の中央に穴を開けた。
位置決め治具の台の中央の窪みに鉛円盤を嵌め穴つき帽子を被せM3のドリルで穴を開けた。
その後に鉛円盤の表面をヤスリで削り厚さを0.5mmにした。
(3) 直径を削る
穴の開いた鉛円盤は直径が6mmある。これを5mmまで削った。
直径6mmではノズルの頭部よりも広くて組み込めない。
そこで下の写真の左ような治具を作り穴開き鉛円盤を棒のステンレスとPETGの間に挟んだ。
出っ張った部分に鑢を掛け削ったのが写真の右だ。これで取外せば冒頭のガスケットが完成した。
上の写真のステンレスのガイドボルトは頭の直径が5mmだ。
これはM3のキャップビスの頭をを削って直径5mmにしたものだ。
長さ25mmのキャップビスを電動ドリル頭に取り付け廻しながら鑢掛けした。
僅か0.6mm削って細くするだけだがステンレスのビスは削りにくく難渋した。
100均でダイヤモンド鑢を買ってきて何とか凌いだ。
注:ガスケットとは接合面に挟んで液体や気体の漏れを止める部品の名称です。
同じ目的ですが、水道の蛇口のように滑る部分に使う場合にはパッキンと呼びます。
89. 家具配置検討用模型の製作 2024,05,04 実施
リビングの家具が老朽化したので新しい家具へ入替えようとしている。
買い換える家具の候補は決まったのだが、置く位置と方向が決まらない。
そこで部屋と家具の縮小模型を作って検討している。
下の写真で黒い枠は部屋の輪郭で、1 / 20 に縮尺した。最も長い辺が200mmだ。
当然家具類も1 / 20 に縮尺した。PRUSAで造形できる限界に近い寸法だ。
左側の液晶TVが載っている台はブラウン管時代の古いものなので、買い換えようと考えている。
写真の下の方が南なので画面に陽光が入らない置き場所は左下の角なのだが、
妻の合意が得られない。
妻は、この模型が解り易いと評価したが、黒い部屋の輪郭板が薄いとクレームが付いた。
家具を載せた状態で輪郭板を持ち上げると、撓んで家具が落ちてしまう。
材料を節約するために厚さ0.6mmで設計したのだが、薄く作り過ぎたようだ。
そこで輪郭板の裏側に格子状の補強を接着した。下の写真は補強格子を造形している様子だ。
補強格子を接着した結果ペナペナと撓らず良い感じになった。
格子は2cmピッチで高さ5mmにした。PETGで造形に2時間半ほど要した。
90. 池掃除用ゴミ取りザルの製作 2024,05,13 実施
実家の庭に二畳程の池が在る。以前は鯉を飼っておりポンプと濾過器を使って水を浄化していた。
現在は鯉が死に絶えメダカが棲んでいるだけだ。水のにごりも少ないのでポンプは使っていない。
ところが枯れた水草などが底に堆積しヘドロ状になってしまう。
水中ポンプを使って取り除こうとした場合に、メダカを吸い込んでしまう危険性が在る。
そこで写真のように柄の長い掃除用のゴミ取りザルを作った。
柄の棒は掃除用具の柄で先端のナイロン製?のブラシが消耗し、妻が捨てようとしていた物を活用した。
先端部の着脱ボタンをブラシの部分が押すと外れる構造になっていた。
その機構を活用してザルをはめ込み固定した。
ザルは料理用で鍋の縁に引っ掛けて揚げ物を調理する道具のようだ。
先端が直線状の”D”字形になっているところが目的に合致していた。
もう少し大きな物を探したが、大きなザルは丸形ばかりで”D”字形は見つからなかった。
3Dプリンターで造形したのはザルと柄を繋ぐためのカップラーだ。
柄の部分に嵌るパイプの部分は内径15mm、厚さ1.8mmに設計した。
ザルの握りは直径4mmのステンレス棒を曲げて作られていた。
カップラーにはステンレス棒が嵌る半円状の溝を設けた。
要所の造形寸法を確認する為に、部分的な造形を行い柄と組み合わ合せて寸法を修正した。
左から3個は柄の部分に嵌るパイプの太さや着脱ボタンの具合をデバッグ、
右の3個はザルの握りが嵌る溝のデバッグを行った。
当初は強度が必要なコネクターなので炭素繊維入りPETGフィラメントで造形しようと考えていた。
炭素繊維入りPETGは値が張るので先ず普通のPETGで試作の造形を行った。
試作品に触った感じは、とても強そうだったので試作品を実用品にした。
実際に使ってみて折れたり割れたりしたら炭素繊維入りPETGで再製作する。
91. TPUの造形でノズル詰り 2024,05,29 実施
TPUフィラメントを使って直立円筒形SP用の靴を成形していた際にトラブルが起こった。
フィラメントを送り出す歯車にフィラメントが絡んで送れなくなってしまった。
当然造形は失敗だ。何故か初層の造形を済ませ2層目でTPUフィラメントが出なくなった。
下の写真は送り歯車の扉を開け、絡んだフィラメントをラジオペンチで引き抜いた物だ。
絡みつき曲がった痕跡が見える。原因が判らず何度も繰り返した。
下の写真は絡みつき5回分の残骸だ。上手く造形できず何度も失敗を繰り返した。
絡み付かずに下の写真の様にエクストルーダーのフィラメントを送り出す歯車の横の窓から
TPUフィラメントが溢れ出てしまった場合もあった。しかしノズルは詰まっていなかった。
この場合も初層の造形を済ませ2層目でTPUフィラメントが出なくなった。
何度も詰りを経験して興味深い事に気づいた。
詰まるのは1層目ではなく2層目なのだ。
1層目で毛羽立ったTPUが2層目の造形でノズルの穴を塞いでしまう様だ。
上の写真でも1層目を終え毛羽立っているのが写っている。
TPUは射出温度が高いと毛羽立つ傾向だ。
一層目の定着を良くしようと考えノズル温度を5℃高めの220℃に設定したのだが、これが失敗だった。
これを215℃に下げてから詰まらなくなった。
下の写真は造形に成功した直立円筒バックロードホーン用の靴だ。
92. Dyson SV21 フィルタ掃除用ノズルの製作 2024,06,08 実施
我が家では写真の様なDyson製のコードレス掃除機を使っている。
吸引した塵は遠心力で分離され無色透明の容器に溜まる。故に塵袋は無い。
遠心力で分離できなかった微細な塵は右端のフィルターで補足される仕組みだ。
過日、掃除中にモーターが停まった。原因は微細塵フィルターが目詰まりした事に拠る。
買ってから1年間も微細塵フィルターの掃除を怠っていたので当然の結果だ。
微細塵フィルターは2段階で構成されている。下の写真では見えないが、
左半分は目の粗い一次フィルターで見えている白い部分は更に細かな二次HEPAフィルターだ。
一次フィルター部は円筒形の外部から内側へと空気が流れるので外側に塵が溜まる。
塵は外側にあるので別の掃除機で吸引すれば簡単に掃除できる。
問題は二次HEPAフィルターだ。この部分は円筒の内部から外部へ空気が流れる。
その為に円筒の内部に塵が溜まる。その為に手が届かず容易には掃除できない。
また微細塵フィルターの左端から掃除機の吸引パイプをあてても一次フィルターから
空気を吸い込んで肝心の二次HEPAフィルターからは充分なに吸引されない。
この問題を回避するために二次HEPAフィルター専用の掃除ノズルを作った。
ノズルをフィルター部へ差込むと一次フィルター部を覆って空気の流れを止め
二次HEPAフィルター部から集中的に空気を吸い込み円筒内部に付着した微細な塵を排除する。
製作したノズルをフィルターへ挿し込んでみた。
太さ等はピッタリだったが、掃除機側のノッチ用溝の位置が間違っていた。
正しくは掃除機側から40mmの位置だが、フィルター側から40mmにしてしまった。
実際に使ってみた感じでは、このノッチは必要無い事が判った。
下の写真は100V電源の掃除機と接続して二次HEPAフィルターの掃除を行った様子だ。
一部に間違いが在ったが問題無く使えた。使っている間は二次HEPAフィルターの排気口から
風が吸い込まれ塵を掃除しているのが伺えた。しかし掃除の能力を客観的に評価する手段を
持っていないので能力の復活具合は解らない。
造形に使用したフィラメントはPETGで内部充填率は20%で造形した。
パイプ部分の厚さは3.8mmで設計したが、厚過ぎるようだ。3.2mmで充分な強度が出るだろう。
筏、鍔、サポートは使用せずに済む様に予め設計した。造形には3.5時間を費した。
93. Dyson SV21用フィルタ変換リングの製作 2024,07,22 実施
Dyson製掃除機のフィルタは消耗品だ。先月に掃除用ノズルを製作したので暫くは問題なく使える。
しかし何れ交換が必要になる筈だ。そこでAmazonで安価な互換フィルターを探した。
Amazonには沢山の種類のフィルターが売られていたが、オリジナルと同じ外観のフィルターが見つからない。
そこで合いそうな互換フィルターを買ったのだが、問題が在った。少しずつ寸法が違うのだ。
下の写真で右端がオリジナルのフィルターで左の2個は安価な互換フィルターだ。
フィルター部の直径は同じだったのでコードレス掃除機の本体に互換フィルターを差し込んだところ
10mm程の隙間が出来てしまった。オリジナルに比べてフィルター部が長いのだ。
これでは空気が漏れてしまう。またバヨネットの形も互換性が無かった。
10mmの隙間を埋めれば互換フィルターを使えそうだったので隙間を埋める変換リングを作った。
本体側にはバヨネットが在るがフィルター側は設計が面倒だったのでストレートだ。
素材はPETGで積層厚は0.2mm、内部充填15%、筏無し、鍔無し、サポート無しで造形した。
造形時間は30分程度だ。設計には長期間に亘って知恵を絞ったが、造形は簡単だった。
作った変換リングを用いて互換フィルターを掃除機の本体へ取り付けてみた。
変換リングのフィルター側にはバヨネットが無いのでオリジナルの様にカッチッと固定できないが、
ゴムパッキンの御蔭で実用上問題ない程度に固定できた。
上の写真の状態で掃除機の電源ボタンを押したがモーターは回らなかった。
調べた所、フィルターの先端に磁石が仕込まれており、
その位置と本体側の磁気センサーの位置が合わないと本体側に内蔵されたコンピュータが
フィルタ未装着と判断しモーターを回さなかった。
そこでフィルターを手で少しずつ回し掃除機の電源ボタンを押して起動する位置を探ったところ
簡単に合致する位置が見つかった。
変換リングとフィルターの間にバヨネットが無いのでフィルターを回せる。手抜きの功名だ。
その状態でフィルター後部の排気口から風が出て掃除機として機能しているのが確認できた。
このフィルター変換リングで安価な互換フィルターが使えるようになった。
このフィルター変換リングの造形データをPrintablesへ掲示した。
URLは下記だ。
https://www.printables.com/model/951786-filter-conversion-ring-for-dyson-sv21
94. PETG-CFによる大物の造形 2024,08,10 実施
従来は直立円筒バックロードホーンをPETGフィラメントで造形していた。
付帯音の抑制に成功し腹に響く低音も出る。人の声も生々しく聞こえ充分に良い音と感じている。
PETGフィラメントよりも強度が高いPETG-CF(炭素繊維混入)フィラメントで造形したら
更に良い音に変わるのかと興味が湧いた。そこで好奇心から製作に着手した。
そこでTINMORRY製のPETG-CFフィラメントを使用して円筒部の造形を開始した。
TINMORRY製のPETG-CFフィラメントはamazonで\3,999-だった。
通常の3Dプリンターではノズルとフィラメントを送り出す歯車が磨耗すると言われているので
予め硬化鋼製に変えてあるが、硬化鋼製での耐久力は判らない。
過去にPETGフィラメントで造形に使ったgcodeファイルを使い造形を試みたところ、
下の写真のように失敗した。原因はフィラメントの吐き出し量が少なくスカスカになった為だった。
数日前に造形した脚部では画層の厚さを0.2mmに設定して成功している。
今回の失敗では画層の厚さを0.3mmにした。0.2mmと0.3mmでは必要供給量が1.5倍になる。
PETG-CFフィラメントは流動性が低く0.3mm画層の必要量を供給できないようだ。
造形速度を下げれば問題を解消できるが造形時間が長くなるのは避けたかった。
そこでノズルの温度を上げて溶けたPETG-CFの流動性を上げる方法を試みた。
従前の230℃を235℃に変更して運転したが、フィラメント供給モーターが脱調し異音を出した。
更に
240℃に上げてみたところ脱調の異音は止まった。下の写真は試行錯誤の結果だ。
下の写真は240℃での造形に成功した直立円筒バックロードホーンの筒の部分だ。
プラスチック製とは思えない質感で艶消し塗装を施したような風合いだ。
造形時間は左端の大きな物の場合で13時間31分だった。
写真では判らないが
従前の230℃ー0.2mmの造形に比べて
240℃ー0.3mmの造形は、
細かな綿のような糸引きが多いように見える。しかし造形が早いのは魅力だ。
95. PETG-CFによる糸引きの処理 2024,08,26 実施
PETG-CFを積層厚0.3mm、温度240℃で造形した場合に糸引きが多く発生した。
Youtubeに対処方法を求めたところ
麦茶の逸般人工作室に
糸引きを無くすには??【3Dプリンターを快適に!】という記事があった。
内容はターボライターで糸引きを溶かして除去する方法の紹介の動画だった。
動画で使われているターボライタをamazonで探したが同じ物は見つからなかった。
外観の酷似した
スライドガストーチ ST-480Cという物を購入した。
実際に使ってみると火口が延びるのでパイプの中のような奥まった所で使い易い。
また普通のライターと違って炎が横方向に出せるので糸引きの除去に向いていた。
但し連続使用時間が30秒と限定されているので超過しないように注意しなければならない。
下の写真で左は糸引きを処理する前で、右は処理後だ。実害の無い程度まで除去できた。
PETG-CFの場合には糸引きを熱風に曝すとPETGは消えるが炭素繊維の部分が残るようだ。
更に時間を掛けて過熱すると炭素繊維の部分が炎になり消えるが造形物の変形が心配で止めた。
96. インサートナットの埋め込みに適した半田鏝 2024,08,28 実施
自分は3Dプリンターを使った工作でインサートナットを使うのでM3用を備蓄している。
その埋め込みに半田鏝を使うのだが、手元に在ったコードレス半田鏝を使ったところ具合が良かった。
自分はAliexpressから\1,500-程度で入手したが今はもっと廉くなっているようだ。
最近Li二次電池を内蔵したコードレス半田鏝が市販されている。自分も好奇心から購入した。
当初は力不足ではないかと疑ったが、インサートナットを埋め込むには充分な発熱量が得られた。
電力は3段階に設定できるが、最小の緑ランプで充分だった。
実際に使ってみると取っ手の部分が直径15mmと細く、電源コードが無いので扱いやすかった。
先端のテーパー部の最も太い部分の直径が3mmでM3のインサートナットに差し込んだ場合に据わりが良かった。
その後部の拡がりが大きくインサートナットが止まるのも具合が良かった。
下の写真は直立円筒バックロードホーンのパイプをM3のキャップネジとインサートナットを
用いて結合させた様子だ。この作業で電動ドライバーを用いたが強く締めすぎてしまった。
強く締めたらインサートナットが抜けると考えていたが、積層部に罅が入った。
インサートナットには異常は見られなかった。インサートナットは強いようだ。
その後、罅の入った部分はアクリサンデー(接着剤)で補修した。
97. PETG-CFで位置ずれ発生 2024,10,09 実施
直立円筒バックロードホーンのPETG-CF化を進めている。
既に1本は完成しモノラルで良い感じの音が出た。
気をよくしてステレオ化すべく2本目を製作中だ。
その2本目を造形した際にトラブルが起こった。
下の写真の様に造形の途中でX軸が僅かにズレてしまった。
右側の細いパイプでは顕著だが、左側の太いパイプでも下端から40mmの位置にズレが見られる。
状況からX軸駆動系の脱調を疑いベルトの聴力を高めたり歯車の芋ネジを増し締めした。
これで解決した筈と考え右側の細いパイプを再造形したところ全く同じ位置に位置ズレが見られた。
結果からClone Prusaの脱調ではなくスライサーの問題のようだ。
既に完成しているホーンではそのような問題は発生していない。
一本目と2本目の差異はスライサーだ。PrusaSlicerの新版が出たので乗り換えたのだ。
新版はPrusaSlicer2.8.0だ。これが疑わしかったので以前のPrusaSlicer2.7.2へ戻した。
今のところ問題は再発していない。
98. 造形物の剥離事故が発生 2024,11,12 実施
PETGでソファー用の脚カバーを設計し造形した際に造形物の剥離事故が発生した。
原因が判らず造形の条件を変えて10回ほど試したが、剥離は止まらなかった。
自分は造形の際にスティック糊を使っている。失敗した造形物を剥がしてみたら
白く四角に残るはずの糊の跡が欠けている部分が在った。その部分で剥離が見られた。
スティック糊がビルドプレートから剥がれてしまうのが剥離の原因のようだ。
自分が使ったスティック糊はダイソーで入手した水溶性の物だ。
後の掃除が水で流して簡単に済むので気に入っている。
ビルドプレートを斜め方向から撮影したのが下の写真だ。
造形で頻繁に使う中央部が変色し表面のザラザラが磨耗しているのが伺える。
このビルドプレートで数え切れない程に沢山の造形を行ったので磨耗は仕方ない。
ソファー用の脚カバーを中央部を避けて右手前で造形したところ問題なく成功した。
使用したフィラメントはPETG黒だ。
最近ソファーに横になってカウチポテトよろしくYoutubeを見ることが多い。
古く痛んだソファーを新しい物に買い換えたのだが、その脚にロボット掃除機ルンバが乗り上げてしまう。
また鉄製脚の幅が10mmしかなく絨毯に食い込んでしまう。
それを防ぐ為に底面積が5cm*5cmのソファー用脚カバーを製作した。
底面は厚さ2.4mmで充填率30%で設計製作したが、今のところ割れずに使えている。
99. PETGとABSの接着実験 2024,11,18 実施
3Dプリンターを活用して工作を行うと他の素材と接着したい場合が出現する。
今回はPETG-CFで造形した試料と射出成型で作ったと思われるABS製リモコンケースを用いて接着の実験を行った。
その結果、PETG-CFとABSの接着にはコニシ株式会社製の
ウルトラ多用 SVソフトが強く着くと解った。
以下に実験の様子を説明する。
実験に使用した材料は下の写真の様だ。
使用した接着剤はコニシ株式会社製の
ウルトラ多用 SVソフトとという物だ。
適用素材の説明にPETとABSと在ったので、この実験には適していると考えた。
接着対象はPanasonicの照明用リモコンだ。
塵を捨てに集積場へ行ったら不燃塵の籠にあったので拾ってきた。
電池ケースの内側にABSと陽刻されていたので本実験に好適だった。
接着面を無水エタノールで清浄にして使用した。
左端の黒いのが3Dプリンターで作ったテストピースだ。
下の写真は3Dプリンターで造形した実験用のテストピースだ。
素材はPETG-CF(炭素繊維入り)で造形条件は積層厚:0.2mm、温度240℃/75℃、内部充填は15%にした。
テストピースの表面に炭素繊維が突き出ているようで通常のPETGの様に艶が無い。艶消しだ。
造形物の大きさは長さ45mm、幅20mm、高さ20mmだ。形は車用の右足用フットレストを想定している。
実験用のテストピースの接着面に
ウルトラ多用 SVソフトを塗りを接着対象のABS製ケースに載せた。
テストピースの周囲に接着剤がはみ出している。
接着剤は塗ってから10分程度で固まりだすが、それまでは動かないように固定が必要だ。
最終的な固さになるのには12時間程度掛かった。
固まっても2液混合エポキシ接着剤のようには固くならず爪の先で押すと凹む程度の軟らかさだった。
しかし爪を離すと元の形に戻る弾力性さを備えていた。
接着強度を試すため接着後24時間経過した時点でゴムハンマーを使ってテストピースを叩いてみた。
力一杯に叩いたのだが剥がれる様子は全く無かった。
金属製ハンマーを使ったらテストピースが割れるかABS製ケースが割れただろう。
ウルトラ多用 SVソフトの接着力は想定よりも充分に強かった。
これならば3Dプリンターを利用した工作に活用できるだろう。
100. パソコンの更新 2025,1,13 実施
3Dプリンターでの造形物の設計や『趣味の工作』に使っているパソコンが老朽化した。
OSがWin7だったのでWin11へと切り替えるべく新しく”中古のパソコン”をオークションで購入した。
右が従前のDELL OPTIPLEX980、左が今回購入したDELLOptiPlex7090だ。
今度のは8コア16スレッドなので自分の用途には十分な能力だ。
自分の用途には足りないと思われた16GBのメモリーを32GBに増やした。
これもヤフオクで3,100の出費だった。8GB*2だ。
本体の前面にはSDカード用の穴が在るが蓋で閉じられていた。
当然にSDカードリーダーの回路基板が無かった。
Amazonを探したが見つからずAliexpressで見つけたので中国から調達して取り付けた。
それに消耗の程度が判らないHDDをSSDに交換した。
OptiPlex7090の横蓋を開けてみたところ3.5インチのHDDが使われていた。
手持ちのSSDは2.5インチなので寸法が合わず取り付けられない。
自分と同じ問題を3Dプリンターで解決した人が居るのではないかと考えた。
3Dプリンターでの作品の掲示板
Printablesを調べたところピッタリの作品が在った。
大きさを変換するアダプターだ。早速ダウンロードして造形したのが下の写真だ。
使用したフィラメントはPETGだ。
造形した変換アダプターにSSDを搭載したのが下の写真だ。SSDの容量は1Tだ。
裏側で見えないがSSDを変換アダプターへ固定するのにM3*5mmのビスを4本使った。
これをOptiPlex7090へ組み込んだのが下の写真だ。
HDDが在った場所にSSDがスッポリと収まった。
OptiPlex7090の設計が素晴らしく蓋を開けるのもHDDの交換も工具を使わないで済む設計だった。
OptiPlex7090 のハードの改造は済み快調に動いている。残る作業はソフトの引っ越しだ。
101. スティック糊用スタンドの製作 2025,2,20 実施
3Dプリンターを用いた造形の際に、造形板への定着を改善する為にスティック糊を使っている。
造形板に糊を塗り終えた後に所定の位置へ戻すのが煩わしく、その辺に置いてしまう為にスティック糊が、
毎回行方不明になってしまう。その対策としてスティック糊用スタンドを作り、プリンターのフレームへ取り付けた。
これでスティック糊が行方不明になる事は無くなる筈だ。
素材はPETGで内部充填15%で造形した。1.5時間で造形を終えた。
下記のPrintablesに設計を開示した。STLだけでなくFreeCADの設計図も開示したので
各自の棒糊に合わせて修正して利用して下さい。
https://www.printables.com/model/1199350-glue-stick-stand/files
102. 初めてのSilk PLA 2025,3,04 実施
好奇心から金色のSilk PLAフィラメントを使ってみた。
Amazonで安かったCC3Dという聞いたこ事の無いメーカー製で2千円弱 / Kgだった。
しかし3月4日の時点では、Amazonの商品一覧から消えていた。廉くて良いので少し残念だ。
このところPETGばかり使っていてPLAについては印刷条件を忘れていた。
そこでPrusaSlicer2.9にデフォルトで登録されていたGeneric PLAを選びGコードを作成した。
下の写真のように直立円筒バックロードホーンの部品を造形してみたのだが、
まったく失敗無く造形できた。写真には5個の部品が写っているが他に円錐を2個作った。
造形物は金属のような光沢を持っており美しく気に入った。
印刷条件は、普通のPLAと違いはなく簡単に造形できた。設定値は下記の通りだ。
ノズル温度 1番目の画層
215℃
ノズル温度 1番目の以降の画層 205℃
ベッド温度 1番目の画層
60℃
ベッド温度 1番目の以降の画層
60℃
103. PETG-CFで造形に失敗 2025,5,01
我が家では大きな物を造形する際には3Dプリンターを団地のベランダに出して運転している。
理由は騒音と微粒子飛散の問題を回避する為だ。ところが昨年の11月から団地の大規模修繕が始まり
ベランダへの立入りが制限され大きな物の造形は出来なくなってしまった。
先日5か月ぶりに建物の足場が外されベランダで3Dプリンターを運転できるようになった。
早速直立円筒バックロードホーン・スピーカーの問題が在った部分の再製作に取り組んだ。
行ったのはホーンの最下端の最も太い部分で直径が208mm、高さが206mmだ。
使用したフィラメントはPETG-CFで温度245℃で積層高0.3mm、内部充填15%で造形した。
造形時間は17時間14分だった。出来上がった造形物は表面がガサガサで失敗だった。
下の写真で左側が造形に失敗した作品だ。表面を良く見るとノズルが吐き出したPETG-CFの糸が
太くなったり細くなったりしていて糸を巻いたような感じだ。
原因はエクストルーダのフィラメントを押し出す歯車が滑ったためと推定した。
普段は積層高が0.2mmで造形していて問題は無かったが、今回は0.3mmにしたため押し出し量が増えた。
それにフィラメントの太さを測ったら1.70mmで規格よりも0.05mm細かった。
それらの悪条件が重なってフィラメント押し出し歯車が滑ったようだ。
フィラメントの滑りに対処するために押し出し歯車の押しつけネジを1/3回転だけ締め付けた。
その状態で運転した結果が下の写真の右側だ。造形物の表面は平滑になりビロードのような風合いだ。
問題は解消した様だ。
104. 空スプールの重量測定 2025,6,03
TINMORRY社のフィラメントが巻かれていた空のスプールが3本溜まった。捨てる前に各スプールの重量を測ってみた。
その結果 A:PETG-W 188g、B:PETG-CF 190g、C:PETG-CF 190gだった。
重量の差は縁の部分の形が少し違う事に起因したようだ。
使いかけのフィラメントを使い造形する場合に、使いかけのフィラメントの残量で賄えるか計算する。
PurusaSlicerを使ってSTLファイルをGコードファイルへ変換する際に、造形に使用するフィラメントの重量が示される。
使いかけのフィラメントの総重量を測っておいて
190gを減算すれば造形に必要なフィラメントの量を把握できる。
Purusaの場合は造形の途中でフィラメントが空になった場合には、造形を中断しフィラメント交換を促してくれる。
しかしフィラメントを戻し排出する過程でフィラメントを引っ掛かり取り出せなくなる事故が時折起こる。
それを避けるために半自動のフィラメント交換を行わないようにしている。