Front Page 2015,01,22 掲載開始
CNC3020 Auto Tool Zero
卓上CNCフライス(CNC3020)を買ってから2年近く経過した。大変便利で今や不可欠な道具だ。
切削作業において面倒なのがエンドミルの刃先を加工対象の上面に合わせる作業だ。
Mach3には
Auto Tool Zeroのボタンが用意されているが、駆動ソフトが組み込まれておらず、そのままでは機能しない。
我がCNC3020 は安価な基本モデルなので対応する検出回路もプローブも無い。プローブを自作し駆動ソフトを組み込んだ。
注意: ①製作には下記に挙げた先達の記事を参考にさせて戴きました。殆んど丸写しです。感謝。
http://www.instructables.com/id/Mach3-Zero-Probe-Tool/
http://www.cncrouterparts.com/auto-z-touch-plate-instructions-p-291.html
②当方の記事には間違いがあるかもしれません。上の記事をお読みになると確実でしょう。
③この記事を参考に製作される方は自己責任です。当方は一切の責任を負いません。
1. 検出原理
加工対象物の上に平板状のプローブ(電極)を置き、
蓑虫クリップで給電したエンドミルを徐々に降下させ刃先とプローブの接触を電気の導通で検出する。
プローブの厚みは駆動ソフトが自動的に補正する。
2. 制御箱の改造
2-1 コネクターの取り付け
我がCNC3020には YOOCNC-NT65-3X基板が使われている。
その基板には検出用の回路は在るが、PROBEと印字された部分にジャックが無い。
そこへ2.1mm 標準ジャックを半田付けした。一般的にはDC電源を供給する為のジャックだ。

ケースには
当初からプラグを差し込む穴が開いていたので金属加工は不要だった。
2-2 検索電圧の変更
YOOCNC-NT65-3Xの
回路図を見るとプローブに加わる電圧はDC5Vだ。
そのままでも動いたのだが、DC5Vでは接触不良が懸念され不安なので24Vに改造した。
①電流制限抵抗R12を330Ωから2.2kΩへ変更した。検索電流は10mA程度になる筈だ。
②下の写真で右端のPROBE用ジャックに5Vを給電するパターンをカットしDC24V迄ジャンパーを配線した。
金属は電気を流しやすい良導体だが、表面にできる酸化皮膜は通しにくい。
酸化皮膜が厚くなったり表面が汚れるとDC5Vでは流れにくくなり接触不良を起こす。
またエンドミルの刃先に油がついていた場合にも接触不良を起こしやすい。
接触不良を起こしエンドミルとプローブの接触が検出されない場合には、
エンドミルがプローブに食い込んだりエンドミルを折損したりする恐れが在る。
3. プローブの製作
ガラスエポキシのプリント基板に半田メッキを施し、これに誤操作対策を加えた構造にした。
3-1 エンドミル折損対策
エンドミルが接触する部分には両面プリント基板を使い、その裏側の中心部を削って0.5mmの薄さにした。
誤操作した場合には、エンドミルがプローブを突き抜け折損を回避する。
突き抜けた場合に、エンドミルが加工対象に食い込まないように直径32mmの平ワッシャーを2枚重ねて接着し、
下部に高さ約5.6mmの空間を確保した。またワッシャーには重石の役割も在る。
プローブ全体は、プリント基板の厚さを加え6.18mm になった。
CNC3020のZ軸は50mm程度しか動かないので、必要最小限の厚みに抑えた。
3-2 動作表示LED
エンドミルがプローブに接触した際に点灯する黄色のLEDを取り付けた。
Auto Tool Zeroを実行する前にプローブを手で持ち上げてエンドミルへ接触させ、電気的な機能を確認できる。
4. Mach3の設定
Mach3の設定は
入力ピンの割付と
駆動ソフトの書き込みの2箇所だけだ。
4-1 入力ピンの割付
YOOCNC-NT65-3Xでは、プローブの入力ピンは15番と決まっていて変えられない。これを下図のように設定した。
4-2 駆動ソフトの書き込み
ゼロ点を検出する為の操作を定義した駆動ソフトをMach3へ書き込まねばならない。以下の手順で行った。
①Mach3画面の最上部に横一線に並んだスイッチの中の
Operatorをクリック。
②プルダウンメニューが現れるので、
Edit Button Scriptをクリック。
③幾つかのスイッチが点滅するので
Auto Tool Zeroをクリック。
すると下のような窓が現れる。ここに駆動ソフトを書き込む。
④駆動ソフトを書くのは面倒なので、先達がWebで開示しているのを使わせて戴いた。良くできている。
http://www.instructables.com/id/Mach3-Zero-Probe-Tool/
その中に在るVB Source codeをコピーし上の窓へペーストした。もちろん当初のMessageは消す。
コピーしたのは上下に在る破線の間だけだ。
⑤CNC3020に合わせて必要な部分を修正する。
ZMove =
10.00 'Total lenght of Probe to move before Stop or no Contact Made.
ZOffset =
6.18 ' Plate Hight
Code "G0 Z10" を Code "G0 Z
-5"
⑥
File保存する。名前は変更しなかった。
以上で駆動ソフトの書き込みは完了だ。
5. 試運転
5-1 検出失敗時の確認
Z軸を最上部へ異動し、Auto Tool Zeroをクリックして起動。
Z軸が降下開始。その後に駆動ソフトで設定した10mmに達して停止しProbe **ERROR**と表示された窓が現れた。
エンドミルがテーブルに突き刺さる心配は無さそうだ。
5-2 基本動作の確認
Z軸を最上部へ異動し、Auto Tool Zeroをクリックして起動。
Z軸が降下開始。手でプローブを持ち上げてエンドミルと接触させたところLEDが点灯し、降下停止。
直後、僅かに上昇(2mmの筈)。
Mach3のZ位置表示窓に8.18mmと標示された。
駆動ソフトも正しく動くことが確認できた。
5-3 実働試験
試験用プリント基板の上へプローブを乗せ、エンドミルの先端をプローブとの間隔が5mm程度になるよう移動させた。
Auto Tool Zeroをクリックして起動。
Z軸が降下開始。刃先がプローブへ接触した瞬間だけLEDが点灯。直後にZ軸がプローブの上2mmまで上昇。
Mach3のZ位置表示窓に8.18mmと標示された。これで自動Zゼロの動作を確認できた。
確認の為GO TO ZEROをクリックし、Z軸をゼロ位置へ移動。
プローブを上下反対にして電極が試験用プリント基板へ接触する状態でLEDの点滅を見てZ軸の位置表示を読んだ。
LEDの点灯は0.0225mm、消灯は0.0275mmだった。何と0.0050mmのヒステリシスがある。
我がCNC3020は台形ネジを使っている。そのバックラッシュかもしれない。
プローブの厚みの設定に0.025mmの誤差があるようなので、再度測定し必要なら駆動ソフトを修正する予定だ。
これで自動Zゼロの機能を確認できた。我が工作用には充分な精度が在る。
6. 使用感など
まだ実際の切削には使っていないが、動作試験を何度も行った。
動作は安定しており信頼できる。
ただプローブの裏や切削対象の上にゴミが付いていると0.01mm位は簡単にズレるので要注意だ。
動作表示LEDは大変便利で不可欠と思える。簡単に機能試験ができるし、
Auto Tool Zeroを実行し刃先がプローブに接触した一瞬だけ輝き、ゼロ位置を検出したのが解り安心感がある。
eBayなどで売られている既成品のプローブはLEDが無い物が殆んどだ。不特定の検出回路を対象としているので
付けたくとも付けられないのだろう。
検索電圧を24Vにしたのは効果的だった。
当初は5Vを用い手動操作で試したのだが、LEDが点滅する不安定な状態が何度も出現した。
24Vでは、点滅のような不安定な接触は全く見られず極めて安定だった。24Vのほうが断然信頼できる。
7. 鰐口クリップへ変更 ('15,01,23 実施)
エンドミルへ給電する為の蓑虫クリップは使い辛い。
蓑の部分が大きく邪魔だ。この部分に絶縁カバーは不要だ。
またエンドミルを挟む先端の幅が狭く脱落の懸念がある。
そこで蓑虫クリップを鰐口クリップへと替えた。鰐口クリップの型式はELPA PU-36NH。
スーパービバホームで160円(2個入り)だった。理想的とは言えないが、蓑虫に比べて小さくて邪魔にならない。
自分の場合には、3.175mmと4mmのシャンク径の刃しか買わないようにしているので、これで充分だ。
写真はエンドミルがプローブへ接触した瞬間だ。エンドミルは直径2mmの荒削り用?だ。
下のプリント基板は、プローブを切り抜いた残骸だ。
8. プローブの改良 ('15,01,25 実施)
プローブが電線の影響で座りが悪い事があった。特に部屋が冷えているときに電線のビニール被覆が硬くなる為だ。
温度の影響を受けず軟らかいシリコンゴム被覆の電線を使えば良かったのだが、手元に無いし替えるのも面倒だ。
そこで手っ取り早く重石のワッシャーを増やした。重量感があって良い具合になった。
従前は2枚のワッシャーを使っており、全体の重量は約30gだった。
ワッシャー1枚は13gだ。それを2枚増やして
56gにした。
2枚を下に重ねるのではなく、一枚は電極の上に接着した。
使う際に位置合わせの目印にするマジックで描いた黒い円が、僅か2日で消えかかってしまったので、
その代わりにワッシャーの穴を使った。実際に使って見るとXY方向だけでなく段差がZ方向の目安になり具合が良かった。
またワッシャーがLEDよりも高くなったので、逆さにしてプリント基板に給電する際の座りが良くなった。
ワッシャーの追加によって駆動ソフトの設定を下記のように変更した。
ZOffset =
8.52 ' Plate Hight
9. 問題発覚 ('15,01,31 追記)
検出精度を向上させようと、何度も
Auto Tool ZeroとGOTO ZEROを繰り返した際に異常な動きが見られた。
正常な場合には、
Auto Tool Zeroを実行後に
GOTO ZERO操作を行うとZ軸が降下しゼロ点に移動する。
ところが少し上に移動してからゼロ点へと下降する事があった。酷い場合には上がったり下がったりを繰り返す。
上はPlate Hightの位置で、下はゼロ点だ。何回か往復してゼロ点に収斂するが稀に止まらない場合も在った。
原因が駆動ソフトに在るのではと疑い、何度も修正したが解消できなかった。
仕方ないので
Auto Tool Zeroの直後には
GOTO ZEROを使わないことにした。
その原因を追求する過程で頭が混乱したらしくエンドミルをプローブに突き刺してしまった。
プローブを壊してしまったがエンドミルは無傷だった。プローブの折損対策に想定通りの機能が在る。
後日プローブを修理した。また壊す事を想定し予備も作った。
NCファイルが残っていれば同じ物を簡単に切り出せる。CNCフライスは素晴らしい。
原因判明:後日、異常動作の原因が解りました。
Mach3には機械基点と切削基点があります。
コンピューターにた例えれば絶対アドレスと相対アドレスのようなものです。
Auto_Tool_Zeroは切削基点を自動的に設定します。
Auto_Tool_Zero実行した結果、切削基点が機械基点を下回った場合に異常な動きをします。
機械基点が正しく設定されていれば発生しない現象です。
自分の場合には機械基点を全く設定せず、
加工の際に素材の適当な位置をXYZ軸の切削基点と決めています。
その為にMach3の異常な動きを誘発しました。つまり想定外の使い方だったのです。
機械基点に注意すれば防げる問題です。
10. 新型プローブの製作 (`15,04,25 追記 )
従前のプローブは厚さが10.52mmもある。
厚さ10mmの素材では下敷きの厚さ9mmを加えるとプローブの検出面は高さは30mm近くになる。
刃物の長さが15mm程度は在るのでZ軸の余裕が少なく使い辛かった。
そこで薄いプローブを作った。
従前は電線の重さと硬さでプローブが浮き上がり誤差が増えるのを防ぐ為に、
4枚の鉄製ワッシャーを重ねて重量を稼いでいた。
そこで電線を細くて柔軟なシリコン被覆電線に変えた。
その結果、最初に作った2枚の鉄製ワッシャーで充分に安定なプローブになった。
厚さは6.2mmだ。僅か4mm程度の改良だが使い勝手は良くなった。
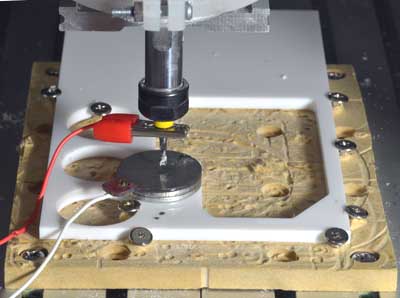
上の写真は、評価試験の様子です。集塵ノズルは外しています。
Auto Tool Zeroを実行した後に、刃の先端がプローブの上方2mmで停止した。
Mach3のZ軸位置表示は8.2mmだった。
プローブの厚み6.2mmにプローブを引抜く為の隙間2mmを加えた高さだ。
駆動ソフトの
プローブ厚み自動補正計算は正しく機能した。
確認の為、手動操作で刃先がアクリル板に接触するまで下げると
Mach3のZ軸位置表示がゼロ付近になった。Auto Tool Zeroは実際と合っている。
白い板は
ふくろうの眼や
3Dプリンター用ブラケットを切り抜
いたアクリルの残骸です。
その下は、下敷きにしている厚さ9mmのMDF板です。
何度も切削に使ったので表面がガサガサです。そろそろ交換時期でしょうか。
Auto Tool Zeroは総ての切削で使っており、使用率は100%です。
特にアクリル等の電気を通さない素材の場合には大変便利です。
ペンダント、
集塵システムと共に不可欠なア
クセサリーになりました。